- Joined
- Jun 4, 2008
- Messages
- 3,285
- Reaction score
- 630
After browsing a bit deciding which should be my second model, I found this one. I decided to build it double scale until I found a 2.5x2.5x3 block of aluminum in the school scrap bin. So not it will be triple scale. 8)
The block, which will become the crankcase, had been flycut on 5 sides. One side had some "oops cuts, so that side will be the one where the flywheel will live.
Since there is extra material in the Z direction I center drilled the crank location 1/2" higher than the plan would indicate. So the engine will have a thicker base, allowing it to sit level and clearing the flywheel. Once I had a hole to locate with, it was on to the lathe to mount the 4-jaw.
I am now a member of the Maryak fan club having removed large amount of swarf from a block of Al:
I don't trust the flatness of the chuck face, so the bearing was left slightly oversize. I'll drill the hole for the crankshaft on the mill since the opposite side is flycut flat.
I had some steel rod that was a suitable size for the pistons, so I decided to attach these next. They will be .75" x .75". I cut one a couple of thousands too small and the other a couple too large, but since the cylinders will be bored and lapped they can be made to fit.
After turning the diameter, I drilled them .5" deep with a 3/8" bit. Then parted off slightly long:
Finished them at the mill. First I milled to length, then using a 3/8" roughing mill I made the bottom square at .54" deep and then elongated the holes to give clearance for the connecting rod. Finally I drilled and reamed the holes for the wrist pins.
I didn't drill holes for the "valve" pin as I'm not sure what size steel ball I will find for the valve. It will probably be 1/8" drill rod.
The block, which will become the crankcase, had been flycut on 5 sides. One side had some "oops cuts, so that side will be the one where the flywheel will live.
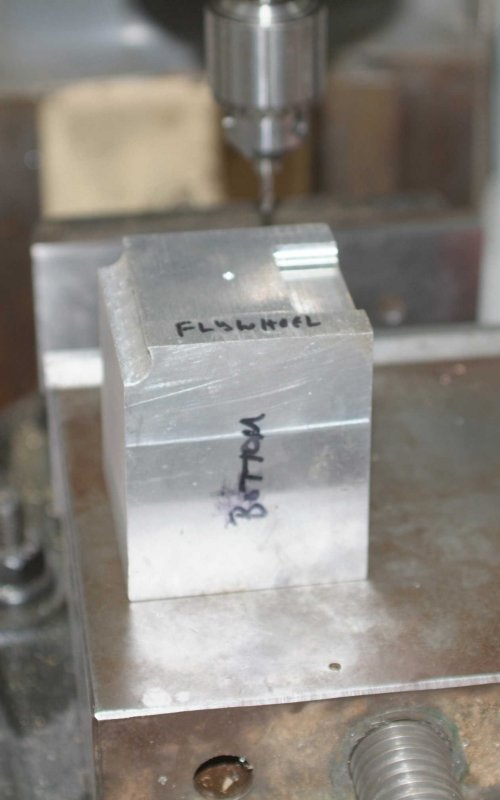
Since there is extra material in the Z direction I center drilled the crank location 1/2" higher than the plan would indicate. So the engine will have a thicker base, allowing it to sit level and clearing the flywheel. Once I had a hole to locate with, it was on to the lathe to mount the 4-jaw.
I am now a member of the Maryak fan club having removed large amount of swarf from a block of Al:
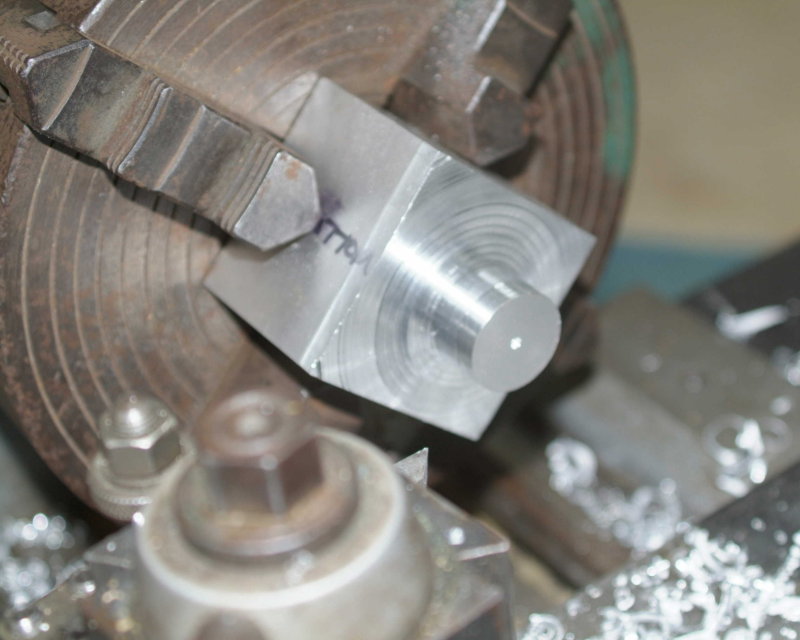
I don't trust the flatness of the chuck face, so the bearing was left slightly oversize. I'll drill the hole for the crankshaft on the mill since the opposite side is flycut flat.
I had some steel rod that was a suitable size for the pistons, so I decided to attach these next. They will be .75" x .75". I cut one a couple of thousands too small and the other a couple too large, but since the cylinders will be bored and lapped they can be made to fit.
After turning the diameter, I drilled them .5" deep with a 3/8" bit. Then parted off slightly long:
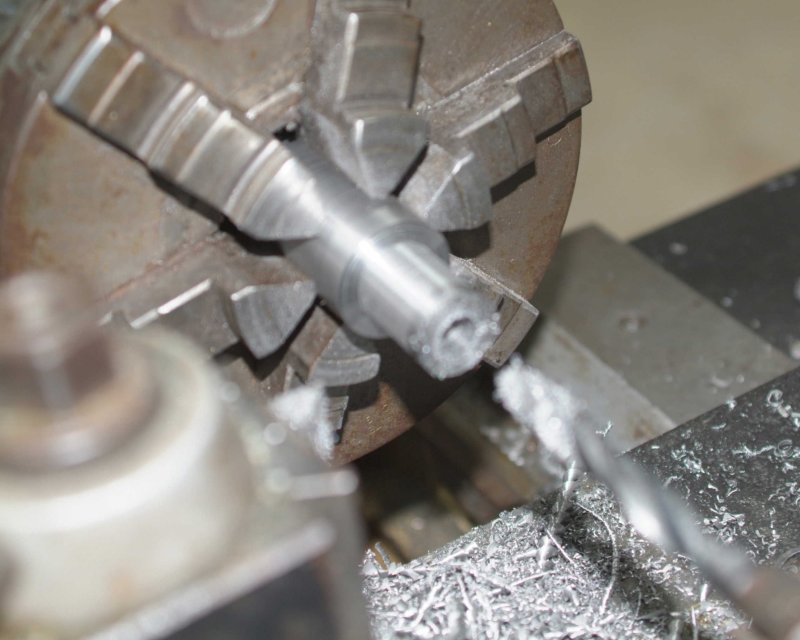
Finished them at the mill. First I milled to length, then using a 3/8" roughing mill I made the bottom square at .54" deep and then elongated the holes to give clearance for the connecting rod. Finally I drilled and reamed the holes for the wrist pins.
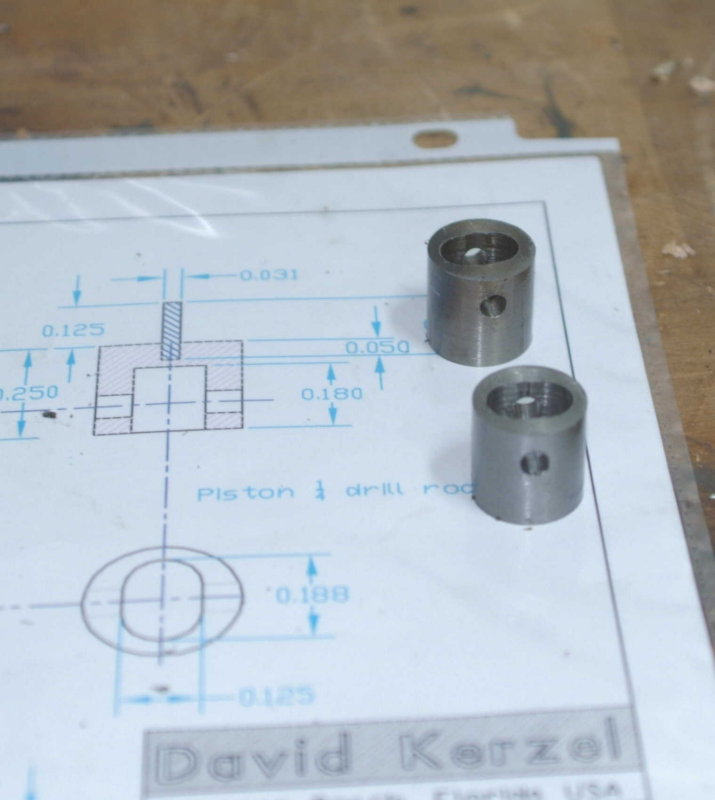
I didn't drill holes for the "valve" pin as I'm not sure what size steel ball I will find for the valve. It will probably be 1/8" drill rod.