- Joined
- Jan 19, 2010
- Messages
- 1,193
- Reaction score
- 41
I Got these plans about 5 years ago from Littlemachineshop.com shortly after purchasing my Mini Lathe at the cummins tool show. I had an attempt at it back then and failed miserably, Ill blame lack of experience, and the plans have been sitting in my bottom drawer ever since. So I got a wild hair up my A@# this morning and decided it was time to give it another go.
I am just building the engine for now, maybee the boiler later, and I plan on putting it on something with wheels instead of a boat.
Here is a pic of the plans cover page and what the engine should look like. (Sorry for the crappy pics, a new camera just aint in the budget right now)
I started by making the Cylinders. I am using 1 inch brass instead of the 1/2 x 3/4 the plans call for. I will be taking off most of the material.
I turned the middle down to 5/8"
Then it was time to mill a little material down and make some flat spots for the steam ports.
Since there was not much material left over to thread a hole I decided to impliment a trick that Steve is doing on his build of the Tandem.
By first using an end mill to make a 1/4" pocket
I then soldered in a 1/4 inch piece of brass.
Here they are after milling the 1/4" stub down and drilling and tapping the holes.
Drilling the holes through the caps and into the cylinder. These will be for 2-56 screws. (sorry no pics of the end caps)
It was then time to mill it down to look good. Off the the rotary table I go.
Here is the before and after.
Thats it for now fellas.
Kel
I am just building the engine for now, maybee the boiler later, and I plan on putting it on something with wheels instead of a boat.
Here is a pic of the plans cover page and what the engine should look like. (Sorry for the crappy pics, a new camera just aint in the budget right now)
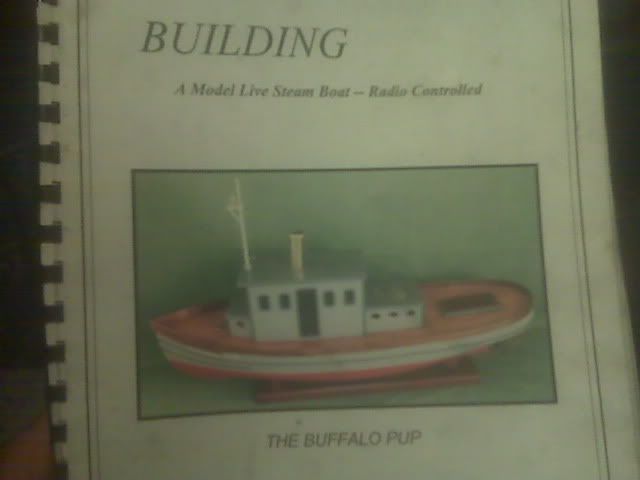
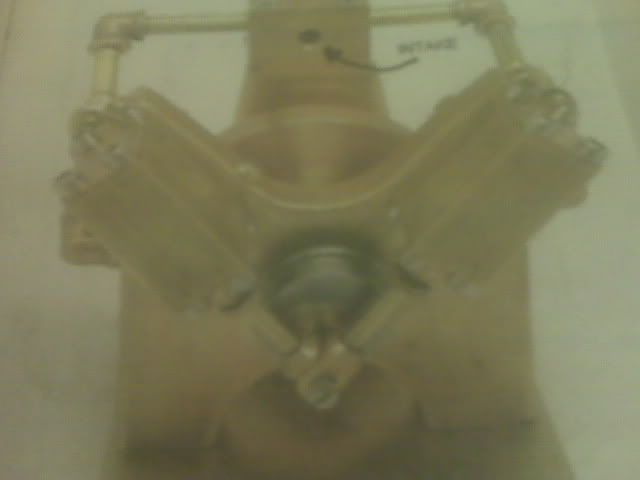
I started by making the Cylinders. I am using 1 inch brass instead of the 1/2 x 3/4 the plans call for. I will be taking off most of the material.
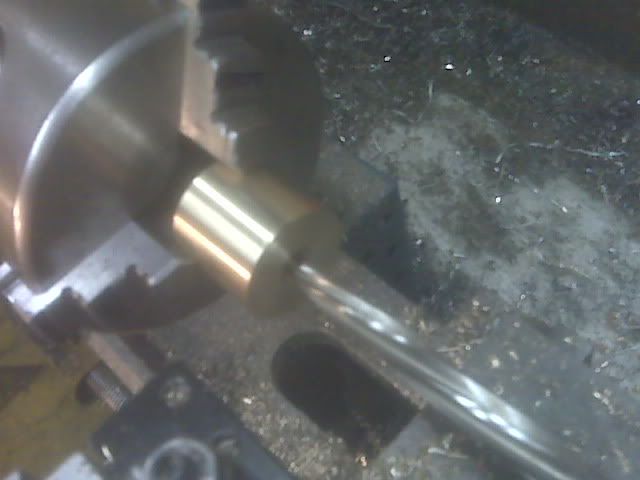
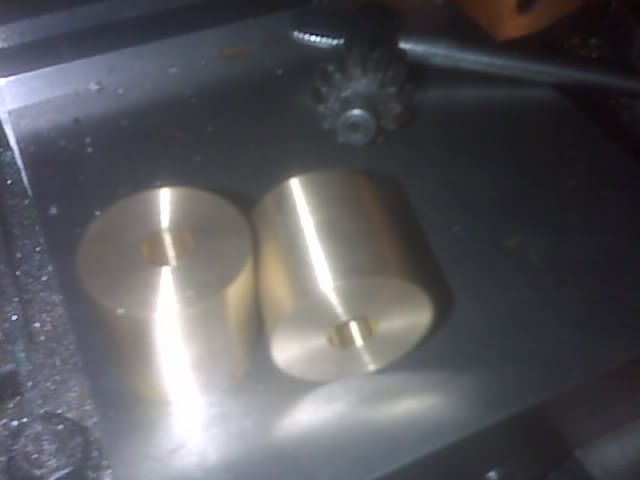
I turned the middle down to 5/8"
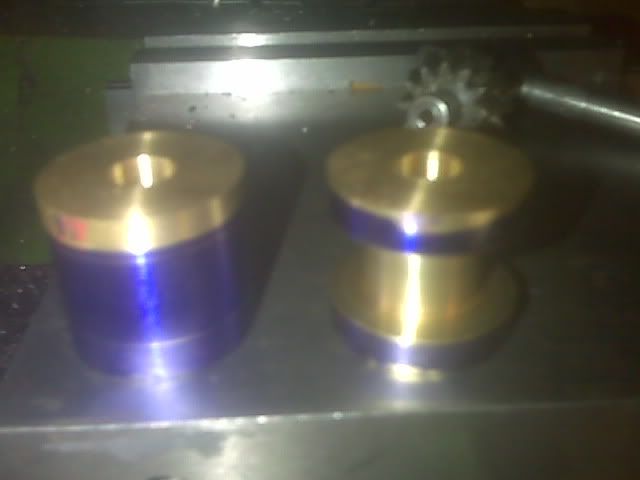
Then it was time to mill a little material down and make some flat spots for the steam ports.
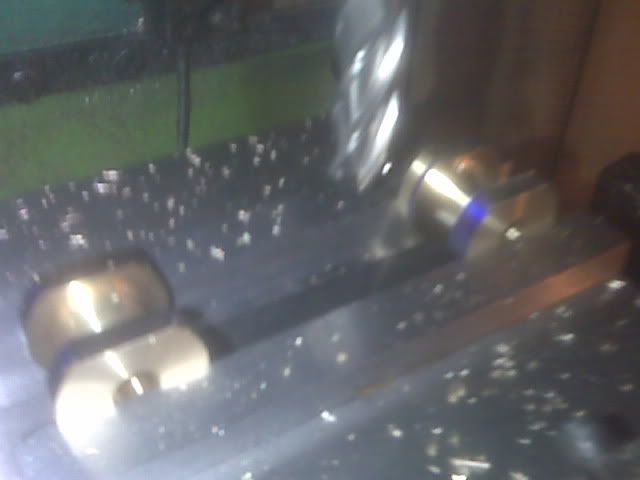
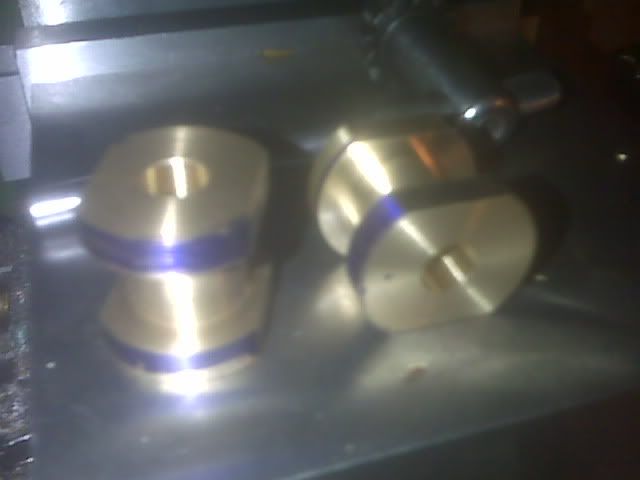
Since there was not much material left over to thread a hole I decided to impliment a trick that Steve is doing on his build of the Tandem.
By first using an end mill to make a 1/4" pocket
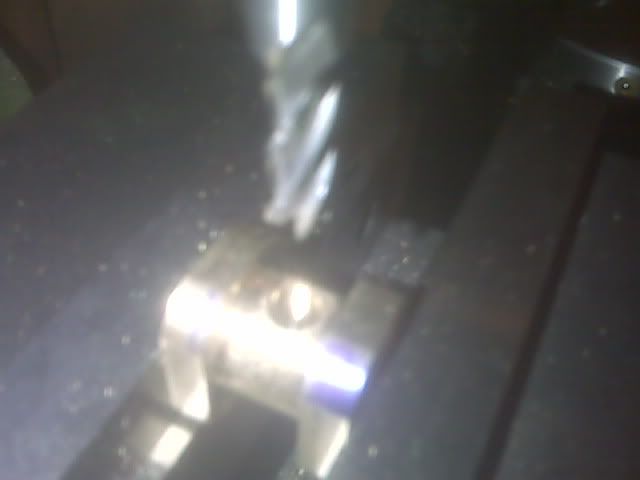
I then soldered in a 1/4 inch piece of brass.
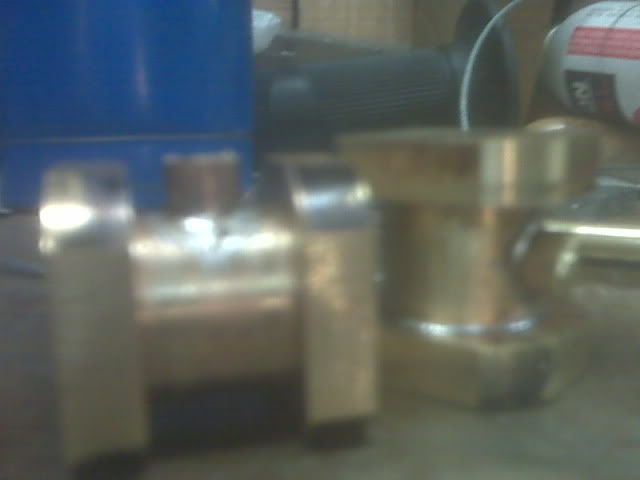
Here they are after milling the 1/4" stub down and drilling and tapping the holes.
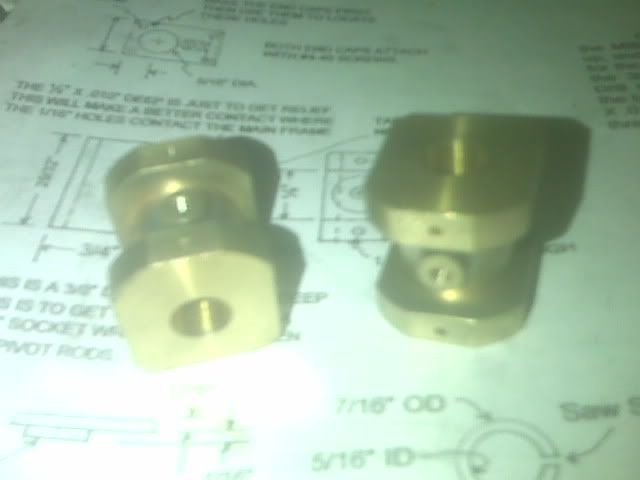
Drilling the holes through the caps and into the cylinder. These will be for 2-56 screws. (sorry no pics of the end caps)
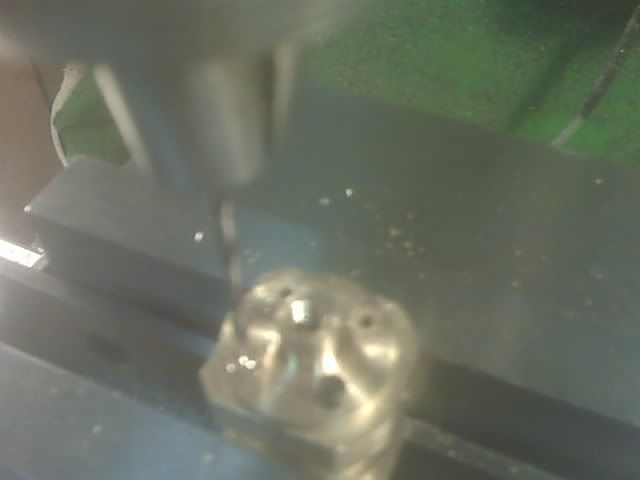
It was then time to mill it down to look good. Off the the rotary table I go.
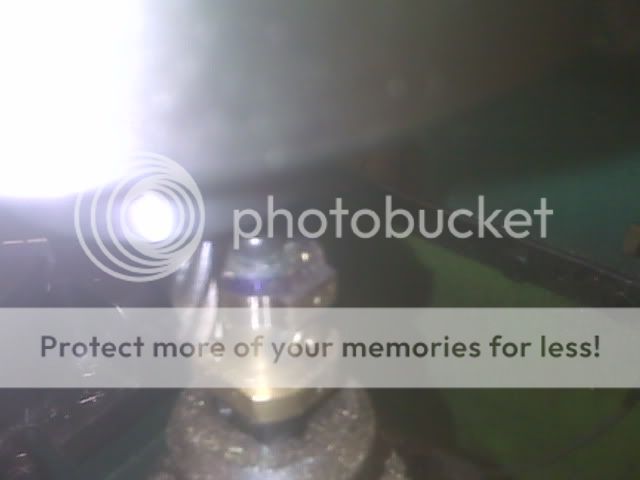
Here is the before and after.
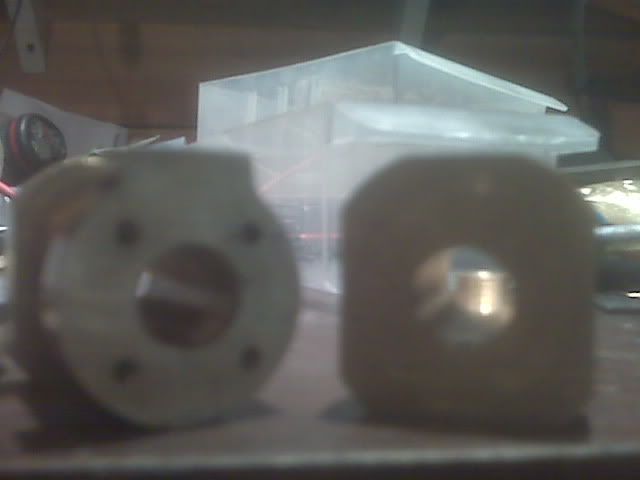
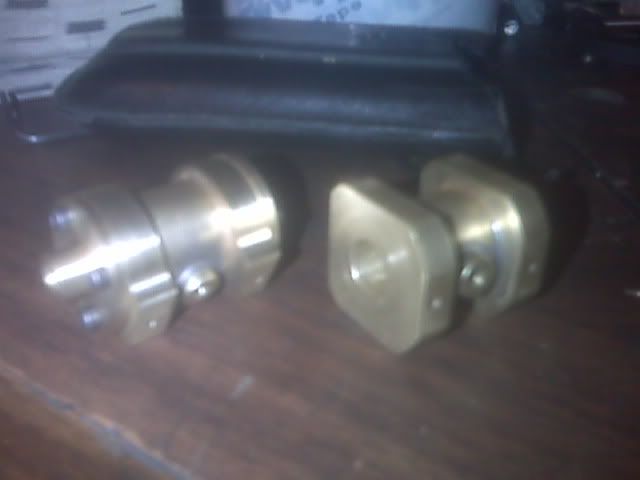
Thats it for now fellas.
Kel