zeeprogrammer
Well-Known Member
- Joined
- Mar 14, 2009
- Messages
- 3,362
- Reaction score
- 13
This is a picture of two parts I need to cut. I've done tapers but I can't get my head around this. The first is a cylinder. The second is a cross-section of a flywheel. Both have similar cuts but from two different directions (the first as a turning operation and the other like a facing operation).
The instruction booklet (for those of you following the thread on the open column launch engine) is silent about this.
The 1st part requires angles of 45 deg and the 2nd part is 30 deg.
I'm thinking it should be 'simple', and maybe it is to the knowledgeable ones here, but if it's more than two types of operation...it ain't simple to me.
Help would be greatly appreciated.
I tried doing an attachment...but when I hit post...my browser went blank and didn't come back. I'm hoping I'm not asking the same question twice.
Thank you.
The instruction booklet (for those of you following the thread on the open column launch engine) is silent about this.
The 1st part requires angles of 45 deg and the 2nd part is 30 deg.
I'm thinking it should be 'simple', and maybe it is to the knowledgeable ones here, but if it's more than two types of operation...it ain't simple to me.
Help would be greatly appreciated.
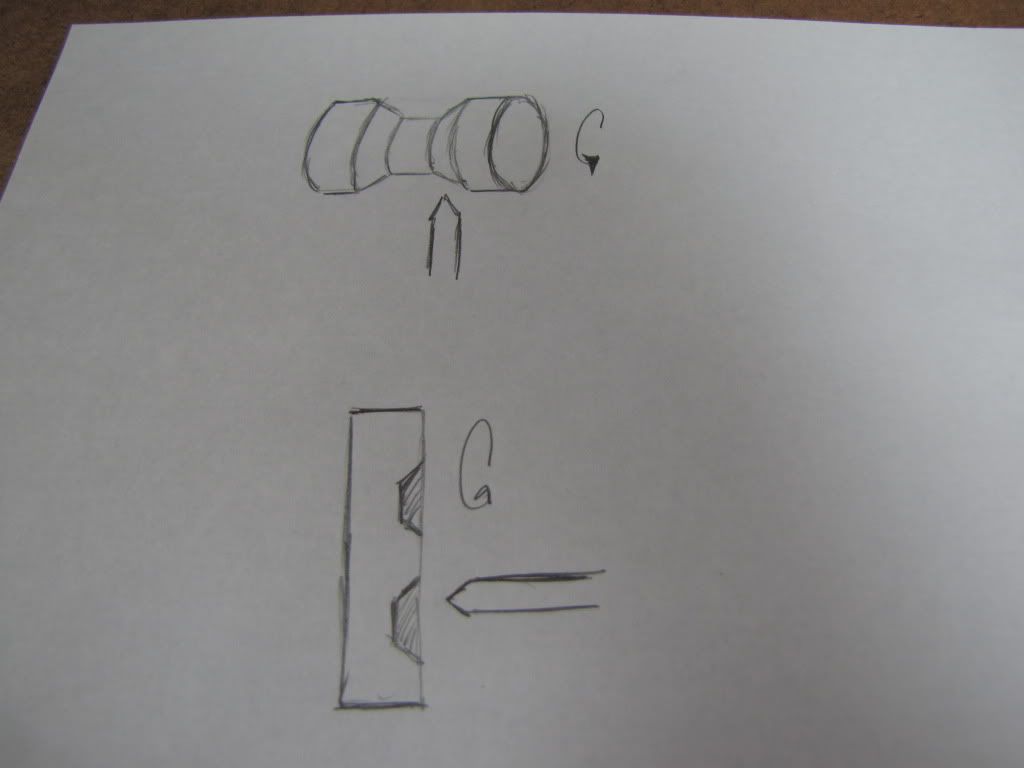
I tried doing an attachment...but when I hit post...my browser went blank and didn't come back. I'm hoping I'm not asking the same question twice.
Thank you.