rake60
Well-Known Member
- Joined
- Jul 8, 2007
- Messages
- 4,756
- Reaction score
- 124
The thread "To plan, or just to fit?" got me to thinking.
Here's an example that really ticked me off at the time I did it.
I'm a big Elmer fan and have built most of the designs from the
Elmer's Engines book. The cylinders are the same in many of the
models. They start from 1" square brass stock chucked up is a 4 jaw
with a .030" offset on the flats in one axis. Do it right and the finished
rough assemble ends up looking something like this.
On my 3ed Elmer build I was turning the flange end on the second side
and realized something just didn't look right. D@^N! I forgot to offset
the stock when I did the first side!
The partially machined cylinder
was tossed into the recycle box and I started over.
A couple months later I was working on another Elmer engine and went to
the brass stock box to find a piece of 1" square to make the cylinder.
There I see that cylinder that I screwed up two months prior.
It was half way done and would take a day or two off the build time of
this project, could salvage it. The valve plate on Elmer's engines is 1/16
thick. If I made a valve plate 3/32 thick, I'd make up the .030" lost to my
error in failing to offset the stock. It worked out just fine.
We've all done it at some point.
How did you save yourself from having to make a whole new part?
(Those close up pictures are showing just how sloppy of a home machinist I am!
)
Rick
Here's an example that really ticked me off at the time I did it.
I'm a big Elmer fan and have built most of the designs from the
Elmer's Engines book. The cylinders are the same in many of the
models. They start from 1" square brass stock chucked up is a 4 jaw
with a .030" offset on the flats in one axis. Do it right and the finished
rough assemble ends up looking something like this.
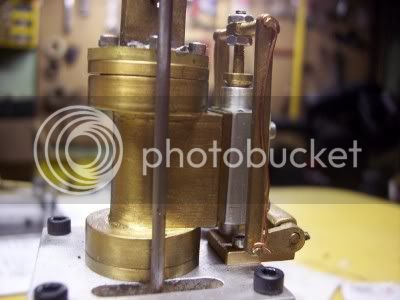
On my 3ed Elmer build I was turning the flange end on the second side
and realized something just didn't look right. D@^N! I forgot to offset
the stock when I did the first side!

was tossed into the recycle box and I started over.
A couple months later I was working on another Elmer engine and went to
the brass stock box to find a piece of 1" square to make the cylinder.
There I see that cylinder that I screwed up two months prior.
It was half way done and would take a day or two off the build time of
this project, could salvage it. The valve plate on Elmer's engines is 1/16
thick. If I made a valve plate 3/32 thick, I'd make up the .030" lost to my
error in failing to offset the stock. It worked out just fine.
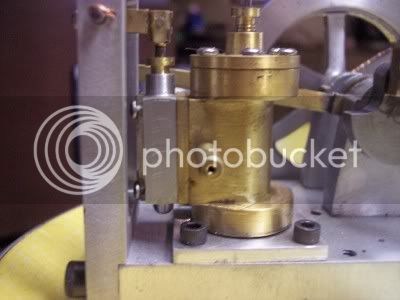
We've all done it at some point.
How did you save yourself from having to make a whole new part?
(Those close up pictures are showing just how sloppy of a home machinist I am!

Rick