RManley
Well-Known Member
- Joined
- Jan 6, 2011
- Messages
- 113
- Reaction score
- 38
A few of you might recognise the subject title from another thread that I started about the engine of my bike project. Well, rather than bring that one back for the gearbox, I started a new one.
The whole reason I started this bike project in the first place is because the gearbox was locking in 1st gear - not very good in modern traffic that likes to punish those who hesitate! So, whilst taking the box apart, I started to measure bits and make parts.
The first thing I started was the kickstart lever. This was fabricated from 2 pieces becuase the large 'end' has a tapered splined bore which was easier to do in the lathe when in bar form.
The setup for cutting the splines. The chuck was indexed using a pointer on the change wheels on the back of the machine. There are 40, 90degree splines in total.
This boss was then silver soldered to the 'arm' of the lever and profiled.
Then lots and lots of filing...
The kink was put in the lever using a 2ft bar and the vice. Not very pretty but it worked a treat!
The peg was then rivited to the small end trying not to put any dings in it with the hammer.
With its stub axle ready for its 120degree segmented gear, it looks quite good against the full size one! The splines on the stub axle were cut in the same way except the angle is slightly different to allow for the change in mating face diameters. I will have a go at casting all the rubber parts in one hit so that will have to wait a while.
Rob.
The whole reason I started this bike project in the first place is because the gearbox was locking in 1st gear - not very good in modern traffic that likes to punish those who hesitate! So, whilst taking the box apart, I started to measure bits and make parts.
The first thing I started was the kickstart lever. This was fabricated from 2 pieces becuase the large 'end' has a tapered splined bore which was easier to do in the lathe when in bar form.
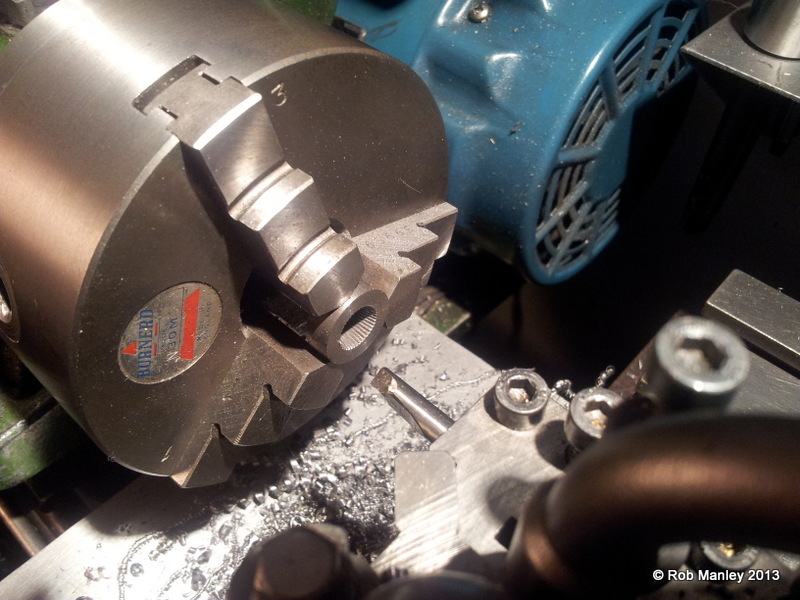
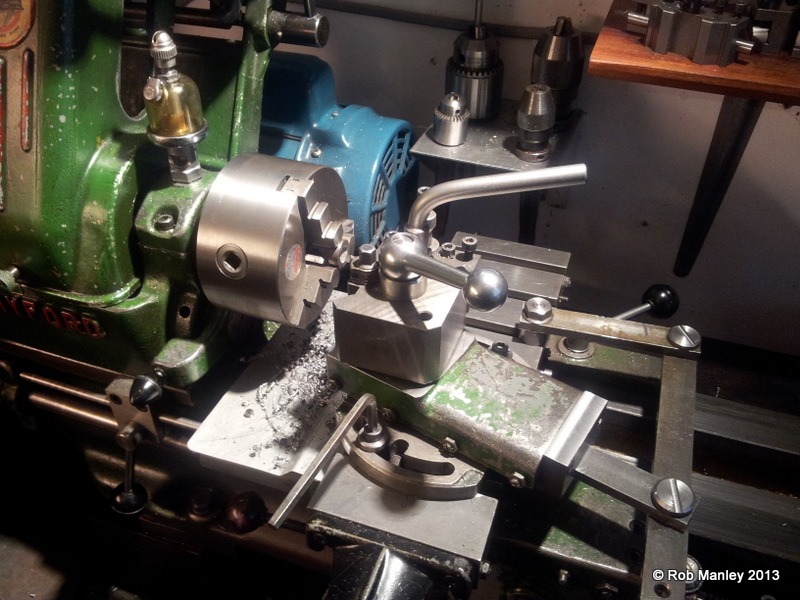
This boss was then silver soldered to the 'arm' of the lever and profiled.
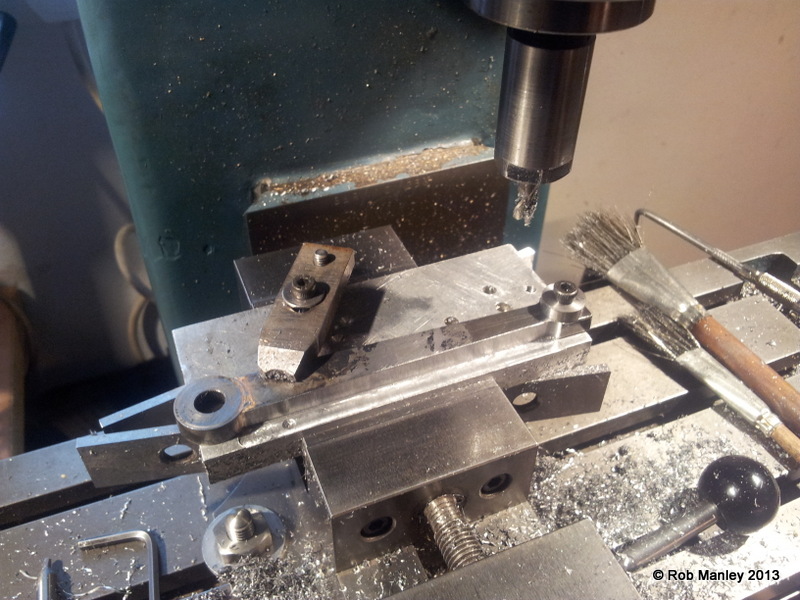
Then lots and lots of filing...
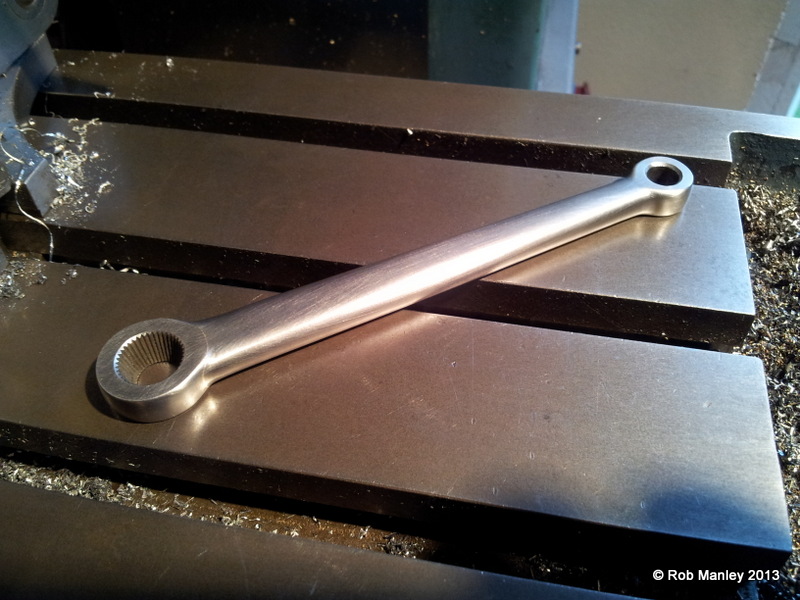
The kink was put in the lever using a 2ft bar and the vice. Not very pretty but it worked a treat!
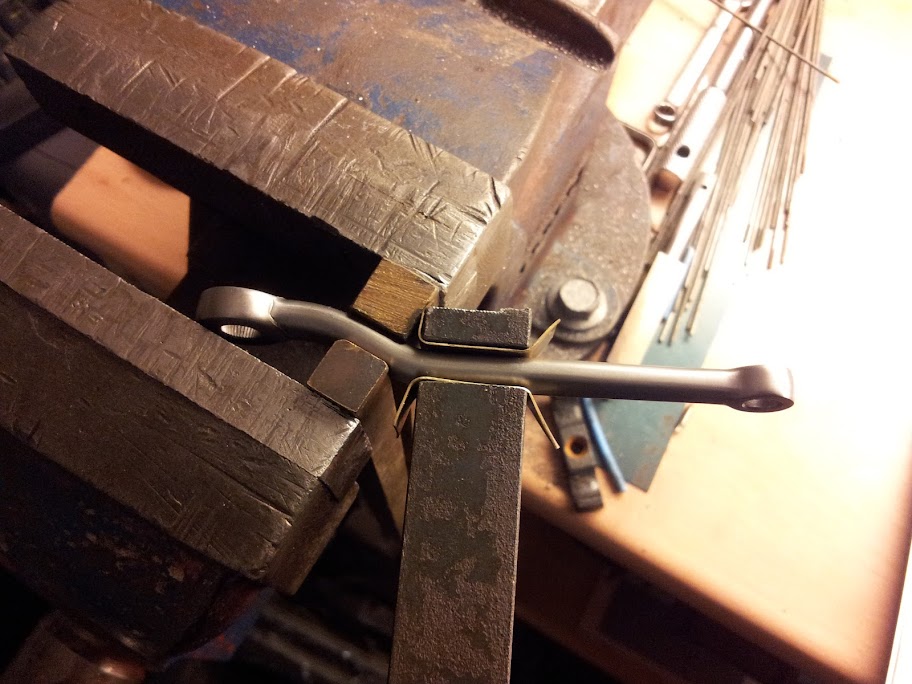
The peg was then rivited to the small end trying not to put any dings in it with the hammer.
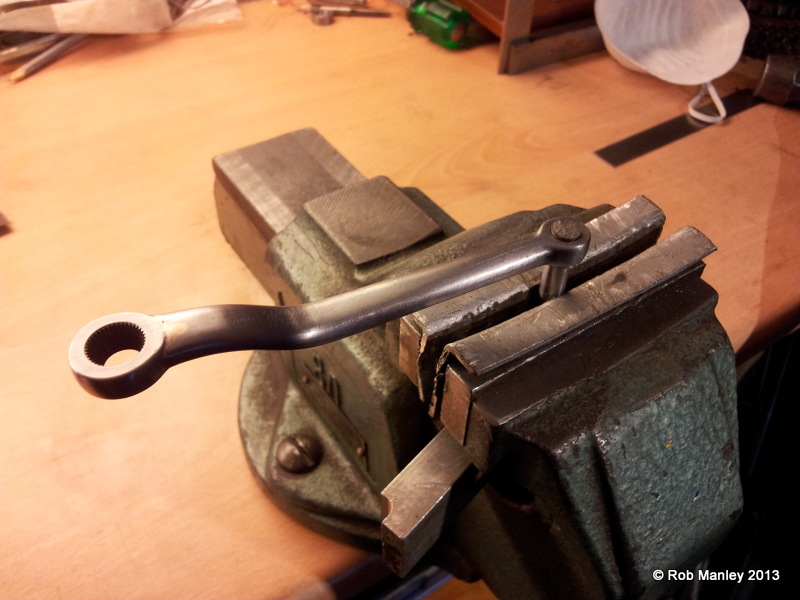
With its stub axle ready for its 120degree segmented gear, it looks quite good against the full size one! The splines on the stub axle were cut in the same way except the angle is slightly different to allow for the change in mating face diameters. I will have a go at casting all the rubber parts in one hit so that will have to wait a while.
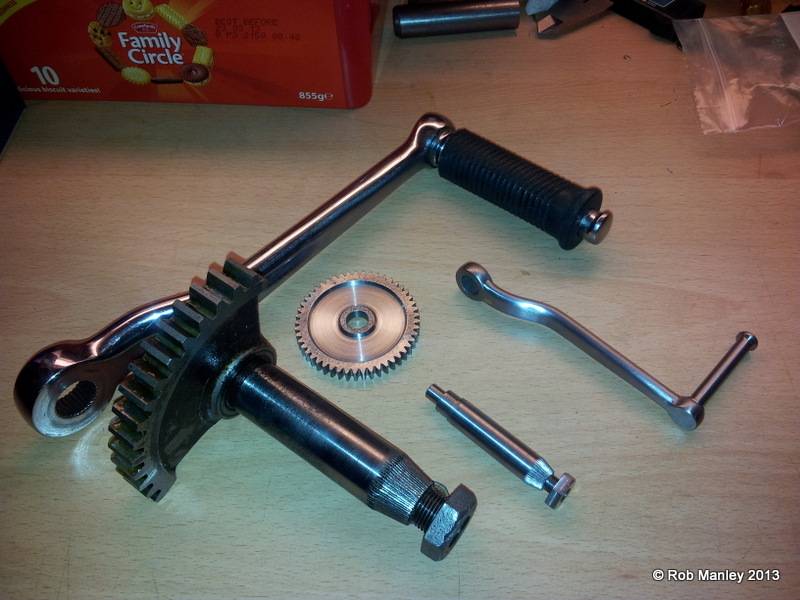
Rob.
Last edited: