RManley
Well-Known Member
- Joined
- Jan 6, 2011
- Messages
- 113
- Reaction score
- 38
Hey all, I found this forum through the model engineer magazines website and it has stolen hours from me. There is some really amazing stuff being produced on here and im jealous that I cant produce stuff like i've seen here.
A bit of background before I describe my project, I like anything with character. So, when I had the opportunity to purchase a friends 1930's douglas motorcycle I leapt at the chance - even though I didnt have a bike license then! I restored it, rode it and now I dont have the time and the gearbox needs fixing so its been in the garage in bits for a while. It didn't take me long to think that a model of the bike would be nice. A complete one, not just the engine. So, thats where it started, a single offcut of aluminium and an old crankcase from a dead engine. 3D cad was used to model everything and some parts were machined on a home-converted cnc mill using Mach3 software. Everything else was machined on a ML7 lathe, Tom Senior mill or a friends Super 7 or colchester.
I have a website which is updated when work is complete and descriptions are added when I can. It can be found https://sites.google.com/site/halfsizedouglasmotorcycle/. Say Hi
As others have done I will post photographs on here with short descriptions. Hope you like it.
Crankcase:
A 3D model was made my measuring the full size crankcase. It's so easy when you have something to turn over and look at.
The block was milled square on the manual and then bolted to the raised aluminium table. The timing case was rouch machined using 1.5" long 1/4" dia ball end mills. It took hours - and just because it was done on the cnc doesnt mean it wasnt scary!
Profiling the top arch. This had to blend with the already machined sides....
The tapped holes on the first face were then used to accuratly bolt the block upside down to machine the back without losing the datum. The tapped holes were M3 and by having almost no clearence on the matching holes in the raised aluminium plate, the block was less than half a thou off datum!
The crankcase plus cam gears next to the full size dead engine.
Machining the 'inside' of the crankcase
A bit of background before I describe my project, I like anything with character. So, when I had the opportunity to purchase a friends 1930's douglas motorcycle I leapt at the chance - even though I didnt have a bike license then! I restored it, rode it and now I dont have the time and the gearbox needs fixing so its been in the garage in bits for a while. It didn't take me long to think that a model of the bike would be nice. A complete one, not just the engine. So, thats where it started, a single offcut of aluminium and an old crankcase from a dead engine. 3D cad was used to model everything and some parts were machined on a home-converted cnc mill using Mach3 software. Everything else was machined on a ML7 lathe, Tom Senior mill or a friends Super 7 or colchester.
I have a website which is updated when work is complete and descriptions are added when I can. It can be found https://sites.google.com/site/halfsizedouglasmotorcycle/. Say Hi
As others have done I will post photographs on here with short descriptions. Hope you like it.
Crankcase:
A 3D model was made my measuring the full size crankcase. It's so easy when you have something to turn over and look at.

The block was milled square on the manual and then bolted to the raised aluminium table. The timing case was rouch machined using 1.5" long 1/4" dia ball end mills. It took hours - and just because it was done on the cnc doesnt mean it wasnt scary!
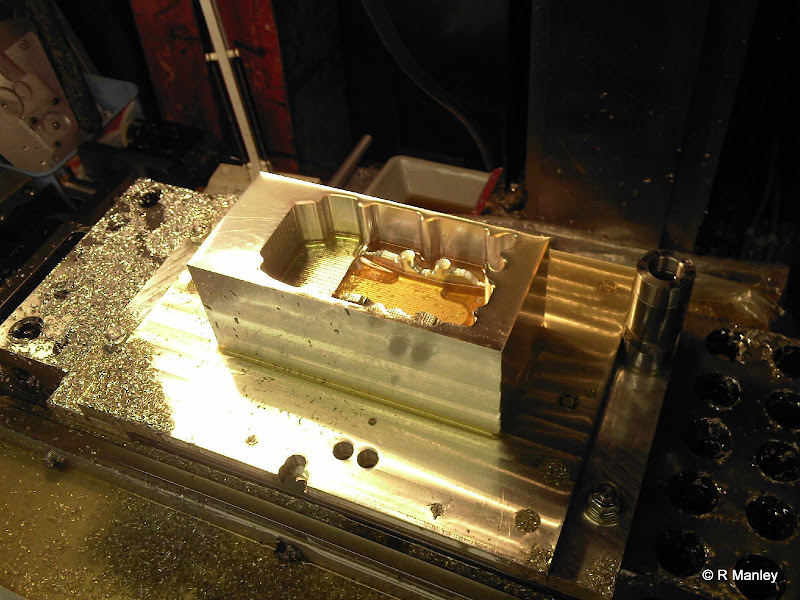
Profiling the top arch. This had to blend with the already machined sides....

The tapped holes on the first face were then used to accuratly bolt the block upside down to machine the back without losing the datum. The tapped holes were M3 and by having almost no clearence on the matching holes in the raised aluminium plate, the block was less than half a thou off datum!
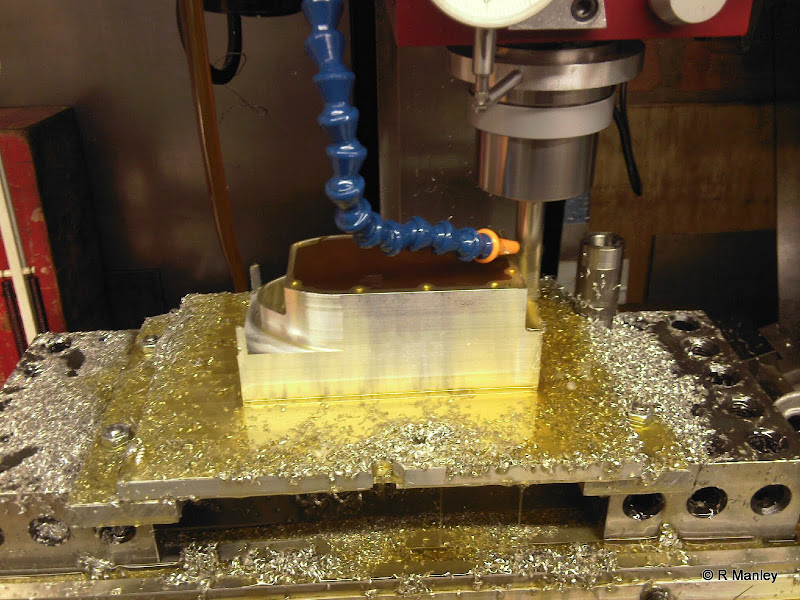
The crankcase plus cam gears next to the full size dead engine.
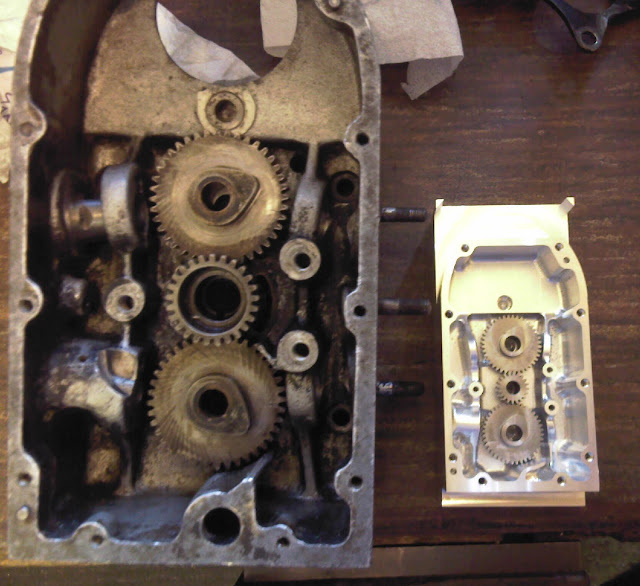
Machining the 'inside' of the crankcase
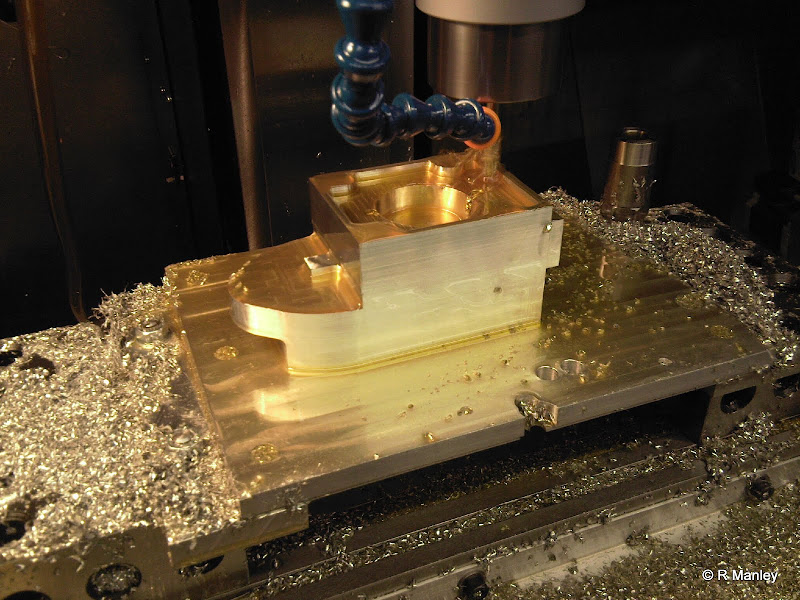