rudydubya
Well-Known Member
- Joined
- Nov 26, 2008
- Messages
- 337
- Reaction score
- 7
Hi folks. Thought you might be interested in seeing how my Upshur hit-and-miss runs with different governor weights and springs. Nothing much new here. I just wanted to look at light weights and heavy weights, weak springs and strong springs, and see how different combinations affected how my engine runs.
Here's a picture of the weights and springs I'll be trying. I've used the bottom set of light weights and the top set of weak springs (as shown at the right) since I built the engine a couple of years ago, so I'm calling that combination my "standard" configuration. The standard weights are half as long, and half the weight, as the longer, heavier weights shown at the top. The standard springs are much weaker than the stronger springs shown at the bottom (the stronger springs have a spring constant about 5 times that of my standard springs).
Here's the video. It starts off with my standard configuration: light weights and weak springs. Then I change the weight/spring combination for each next run. It's self explanatory. Not a professional narration. I tried to fire the guy, but he has tenure.
The stronger springs clearly made the engine run faster, and the engine slowed to a stall with the heavy weights and single weak spring. Between those extremes the engine ran pretty good no matter what combination of springs and weights it had. Maybe if I wanted to tune it for power I'd look at some combination with stronger springs. Or if I wanted a slower runner I might consider heavier weights or even weaker springs.
Hope you enjoyed it.
Regards,
Rudy
Here's a picture of the weights and springs I'll be trying. I've used the bottom set of light weights and the top set of weak springs (as shown at the right) since I built the engine a couple of years ago, so I'm calling that combination my "standard" configuration. The standard weights are half as long, and half the weight, as the longer, heavier weights shown at the top. The standard springs are much weaker than the stronger springs shown at the bottom (the stronger springs have a spring constant about 5 times that of my standard springs).
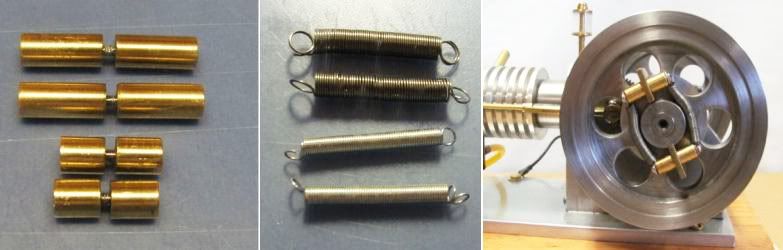
Here's the video. It starts off with my standard configuration: light weights and weak springs. Then I change the weight/spring combination for each next run. It's self explanatory. Not a professional narration. I tried to fire the guy, but he has tenure.
The stronger springs clearly made the engine run faster, and the engine slowed to a stall with the heavy weights and single weak spring. Between those extremes the engine ran pretty good no matter what combination of springs and weights it had. Maybe if I wanted to tune it for power I'd look at some combination with stronger springs. Or if I wanted a slower runner I might consider heavier weights or even weaker springs.
Hope you enjoyed it.
Regards,
Rudy