So i am pretty happy with myself i cut my first thread on my lathe ;D. When i was done the nut threaded on nice and was tight but i do have a question. OK first i will tell you the set up. We are working with 9" southbend lathe quick change tool holder high speed steel tool bit very sharp all screws tight for compound and crossfeed angles set. I was holding work between centres, live centre on tail stock side 3/8 16 thread 6 inches long cutting fluid speed about 130rpms advancing compound .003 to .005 last three cuts and i ended up with a chatter look on the threads i don't know if you can see it in the picture what would cause this? Thanks. Just added i think the steel was cold rolled but not a 100%.
Thanks Bronson
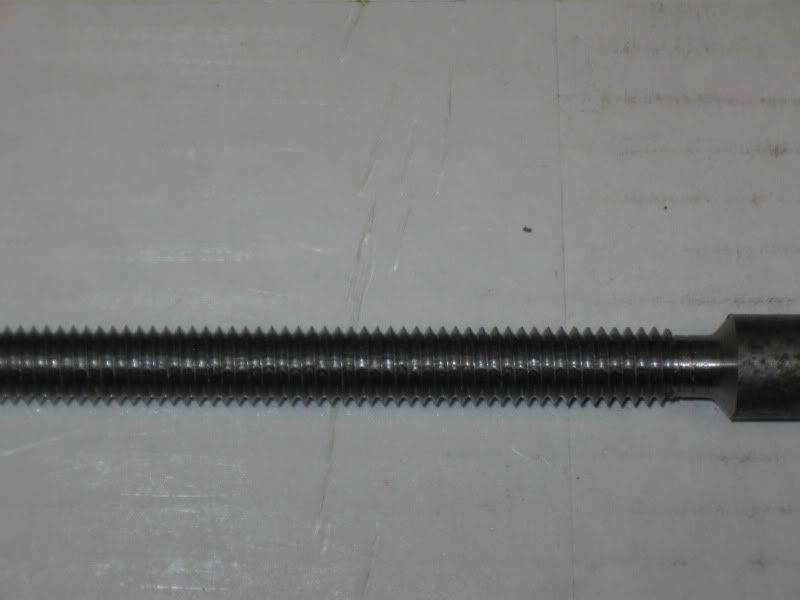
Thanks Bronson