Making curved spoked flywheel.
Spokes cut out of 3/16" thick steel using 1/8" carbide end mill on little cnc mill.
Roughing out radius on spokes with carbide burr on a flex-shaft tool.
Sanding the spokes. Shoe polish style sanding.
Turning and boring rim for the spokes. OD of flywheel will be 3.300 inches.
Spokes and the two parts of the rim.
Rim and spokes held by Loctite and the two part hub insert ready to be held also by Loctite.
Adding some metal filled epoxy (J-B Weld) to finish fillets on outside edge of spokes at the rim.
Hub insert has been Loctited in placed and bored to size. Rim sanded and buffed.
Spokes cut out of 3/16" thick steel using 1/8" carbide end mill on little cnc mill.
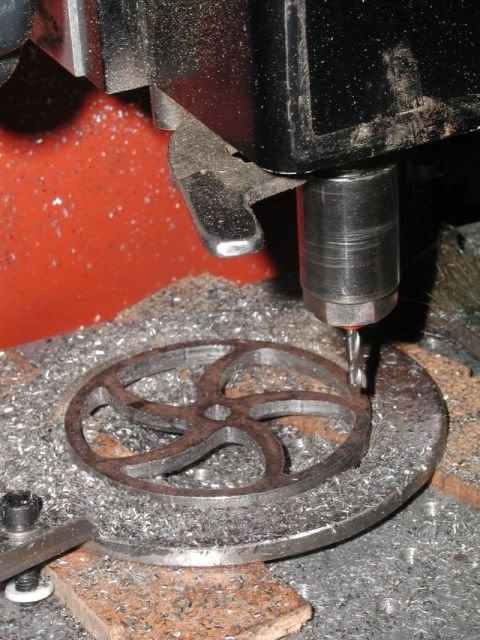
Roughing out radius on spokes with carbide burr on a flex-shaft tool.
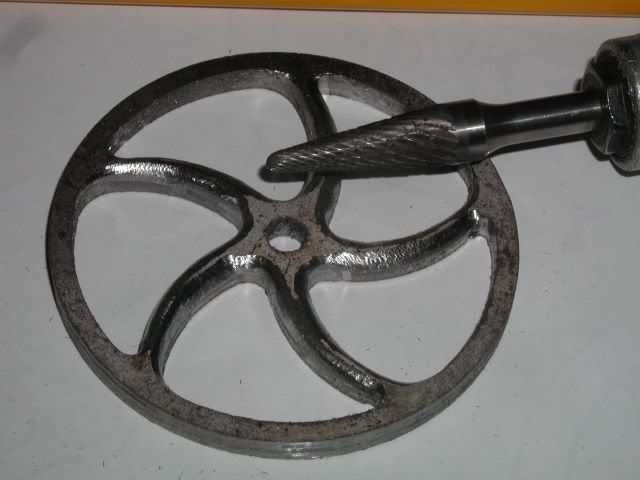
Sanding the spokes. Shoe polish style sanding.
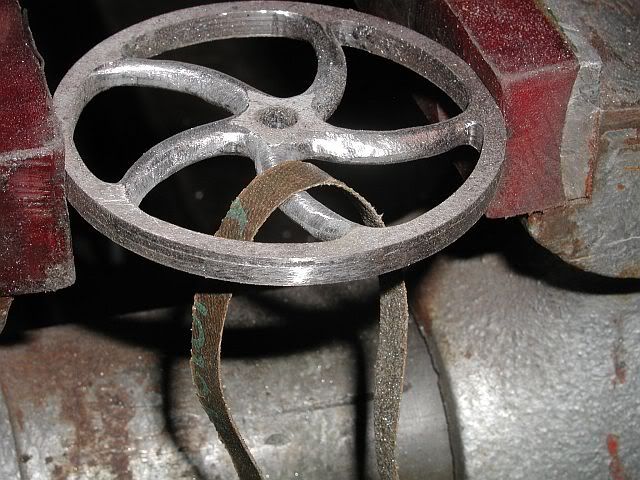
Turning and boring rim for the spokes. OD of flywheel will be 3.300 inches.
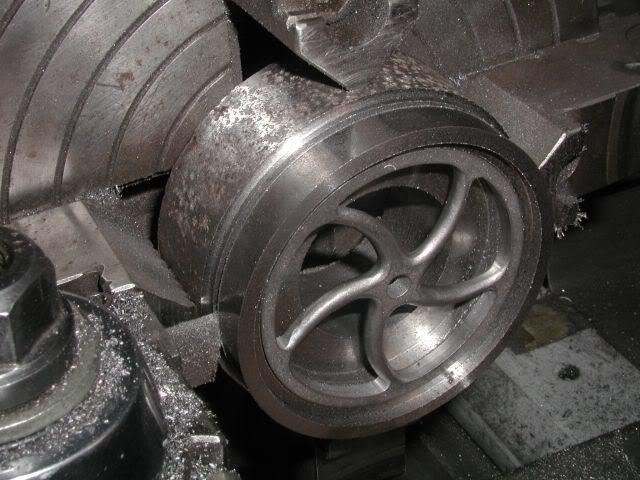
Spokes and the two parts of the rim.
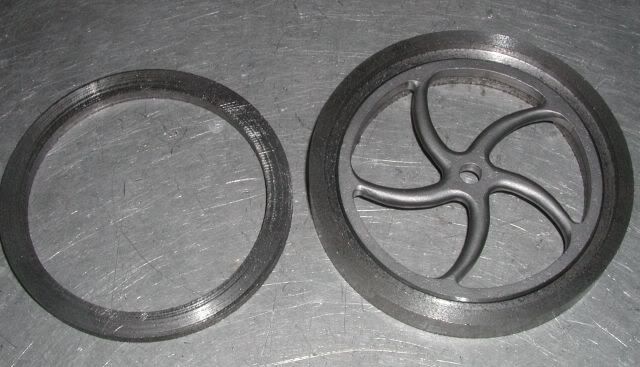
Rim and spokes held by Loctite and the two part hub insert ready to be held also by Loctite.
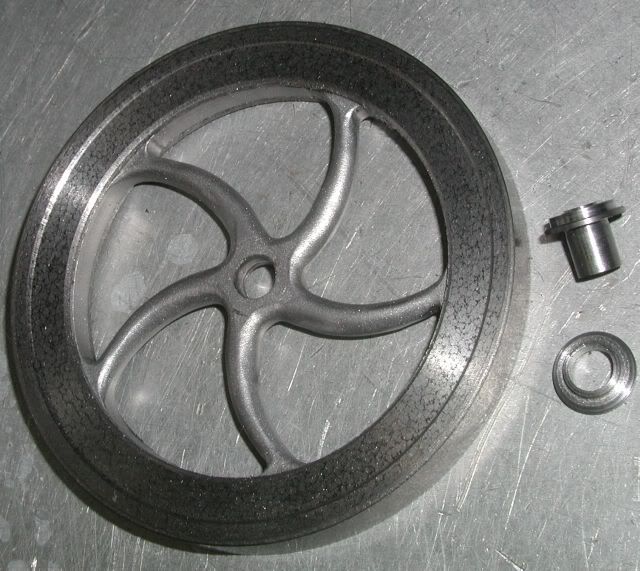
Adding some metal filled epoxy (J-B Weld) to finish fillets on outside edge of spokes at the rim.

Hub insert has been Loctited in placed and bored to size. Rim sanded and buffed.
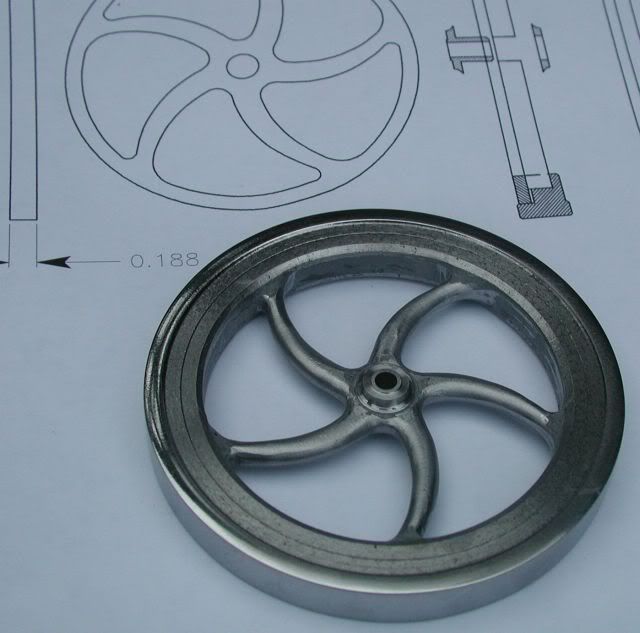