GaryK
Well-Known Member
- Joined
- Mar 19, 2013
- Messages
- 73
- Reaction score
- 80
Today after a lot of time with my CAD software I am starting work on a modified steam engine from a Jan. 1953 Popular Science magazine.
You have all probably seen this engine at some time.
I saw a video of one of these running and it had a very unique sound.
https://www.youtube.com/watch?v=_TwRhMlzf58
I have decided to make a modified version. Mine will have a reverse lever and other modifications, but basically the same overall design.
Today I cut my first chips. I am starting with the heart of the engine. The cylinder block. If you have ever looked at the drawings you will see that they call out drilling steam passages from the end into the cylinder. which later get blocked off.
I didn't really like that so I divided the cylinder block into 3 pieces. Cutting off the steam chests from end. This allows me to drill the passages into the facing parts which will later be screwed together concealing them.
Here you can see the 3 pieces:
And here the two passages. They lead nowhere right now the will before I am done with this part. You can also see a dimple I added to each surface so that everything always goes back together the same way.
I lapped the surfaces for a perfect fit.
Here you can see the entire cylinder block assembled. I plan on leaving them assembled until everything is completed. Then I will take a very light pass on all the surfaces and polish them. Not sure if I want a matte or shiny finish. But either way it will hide the seems.
Anyway that's my first day and the start of my new project.
Gary
You have all probably seen this engine at some time.
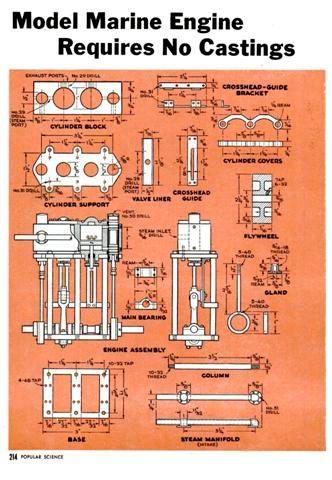
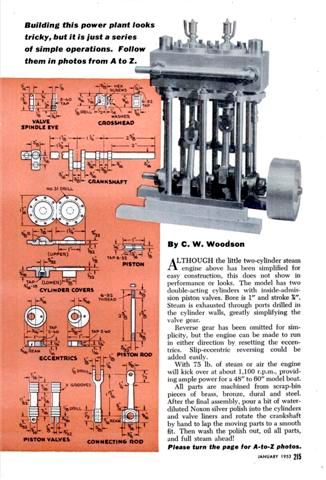
I saw a video of one of these running and it had a very unique sound.
https://www.youtube.com/watch?v=_TwRhMlzf58
I have decided to make a modified version. Mine will have a reverse lever and other modifications, but basically the same overall design.
Today I cut my first chips. I am starting with the heart of the engine. The cylinder block. If you have ever looked at the drawings you will see that they call out drilling steam passages from the end into the cylinder. which later get blocked off.
I didn't really like that so I divided the cylinder block into 3 pieces. Cutting off the steam chests from end. This allows me to drill the passages into the facing parts which will later be screwed together concealing them.
Here you can see the 3 pieces:
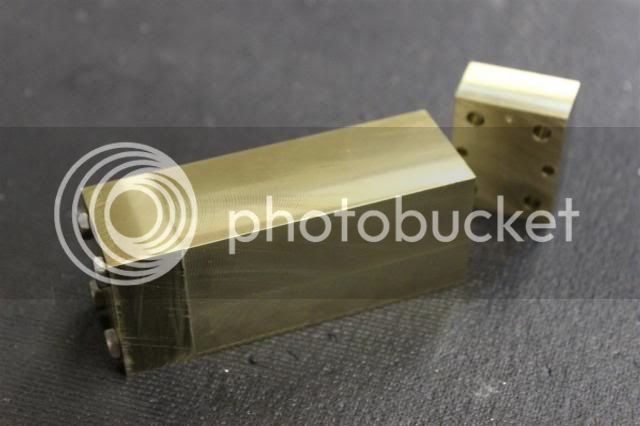
And here the two passages. They lead nowhere right now the will before I am done with this part. You can also see a dimple I added to each surface so that everything always goes back together the same way.
I lapped the surfaces for a perfect fit.
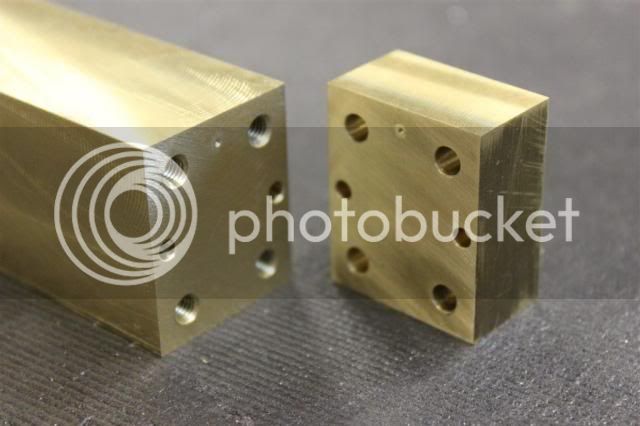
Here you can see the entire cylinder block assembled. I plan on leaving them assembled until everything is completed. Then I will take a very light pass on all the surfaces and polish them. Not sure if I want a matte or shiny finish. But either way it will hide the seems.
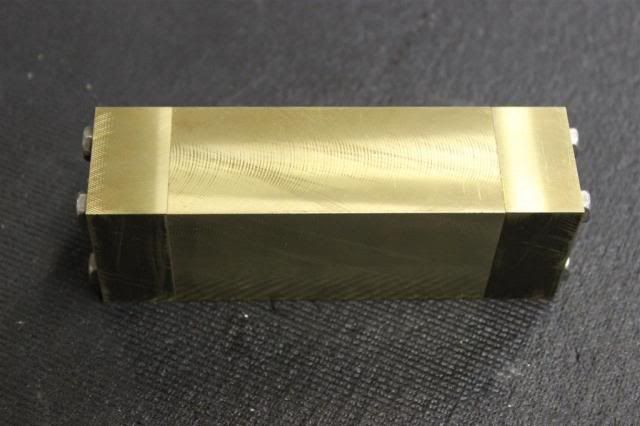
Anyway that's my first day and the start of my new project.
Gary