toolznthings
Project of the Month Winner
Found a new project in " Steam & Stirling " by Elmer Verburg. Decided to build the engine 2 X scale from original drawings with some modifications. Obvious starting point was to draw all the parts actual size in AutoCad LT and then scale up two times. Fastener sizes and other features are sized as work progressed.
Will start with the cylinder that will be made from 12L14 round stock. Rough drilling thru the stock and taking a boring bar to do a short clean up for reference later.
Spot drill and drill thru ....
Next step is to rough square up the 1.500 x 1.500 x 4.000 long cylinder size leaving stock.
A quick layout for reference.
Set up at the mill lining up to the layout for the first milling cuts.
Continue the milling until the stock is roughed out.
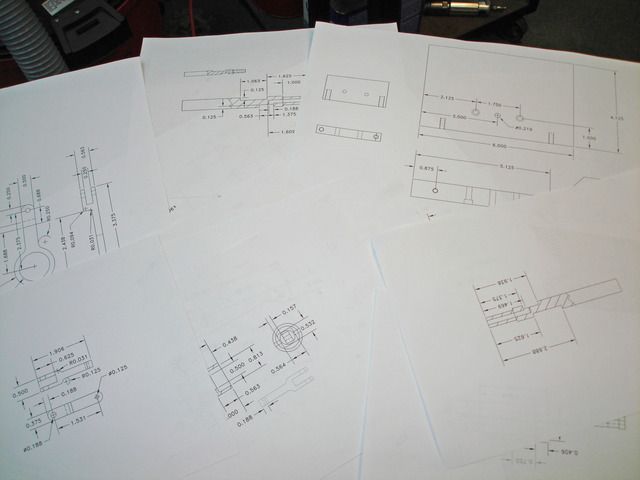
Will start with the cylinder that will be made from 12L14 round stock. Rough drilling thru the stock and taking a boring bar to do a short clean up for reference later.
Spot drill and drill thru ....
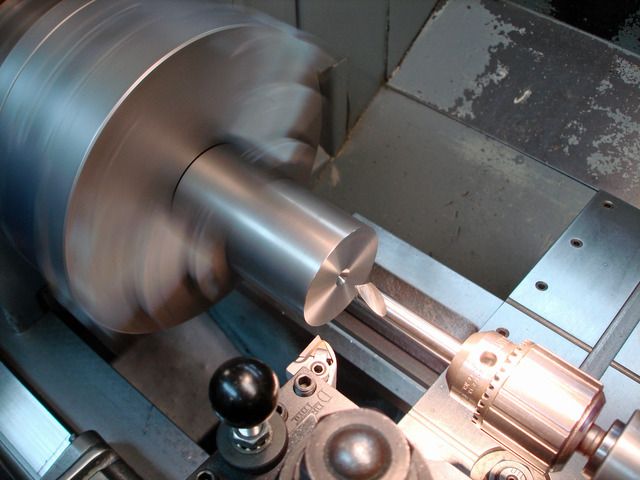
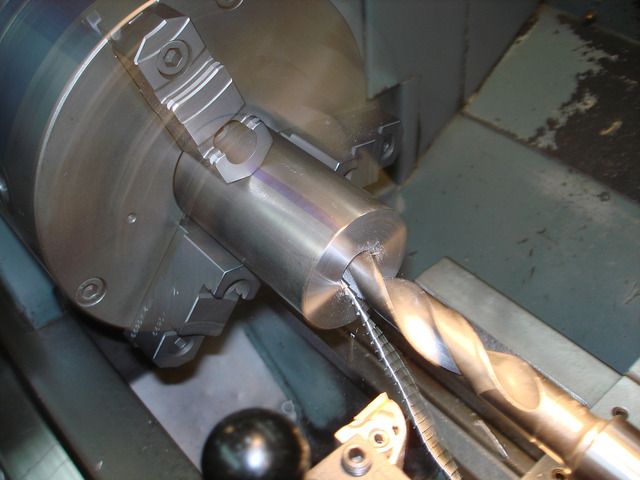
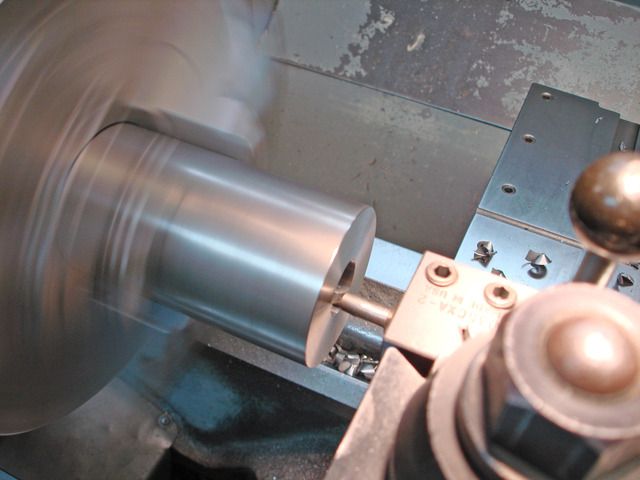
Next step is to rough square up the 1.500 x 1.500 x 4.000 long cylinder size leaving stock.
A quick layout for reference.
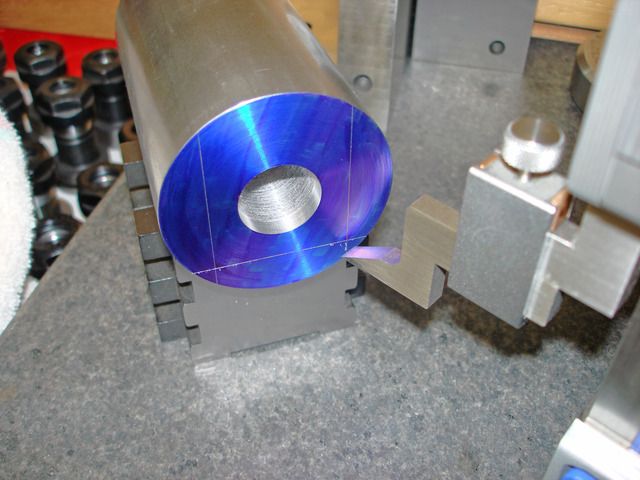
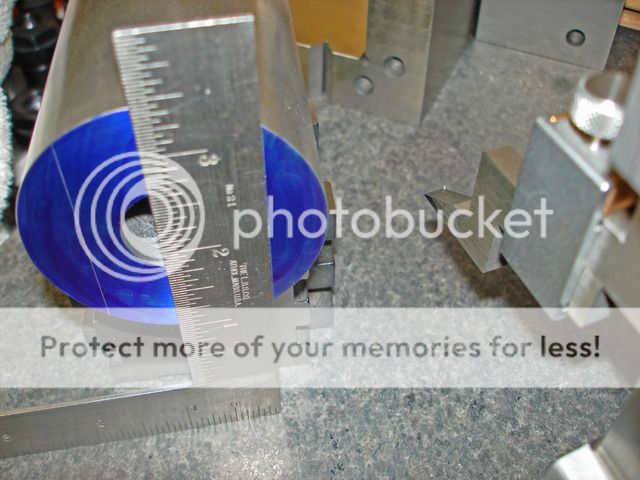
Set up at the mill lining up to the layout for the first milling cuts.
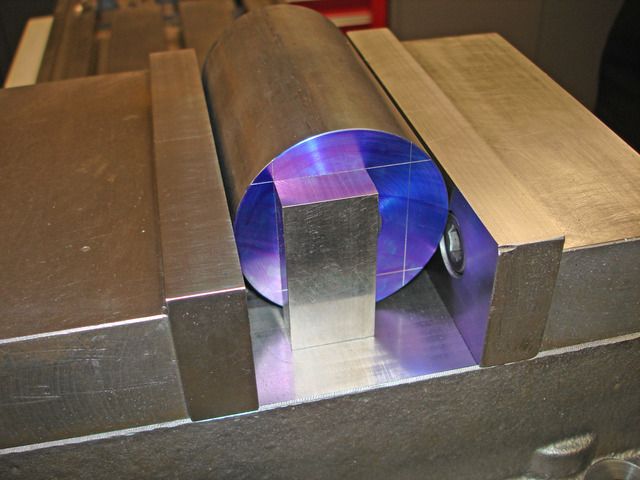

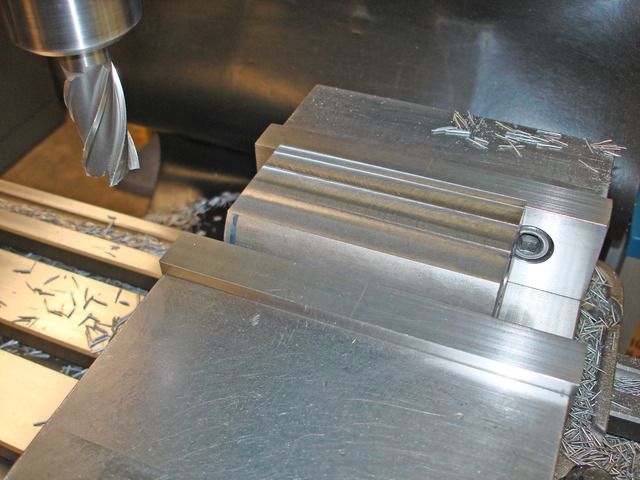
Continue the milling until the stock is roughed out.
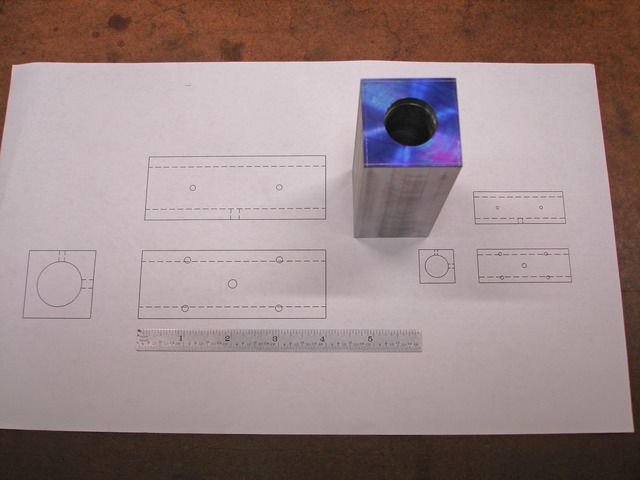