Metal Mickey
Well-Known Member
- Joined
- Jul 5, 2008
- Messages
- 612
- Reaction score
- 6
Today I started on the building of a 15cc, 4cylinder, petrol engine from a design by Edgar T Westbury. I won't say the design is old but the construction article was published in the British magazine, Model Engineer. In fact it was over 62 years ago!
Having said that, it is a well known design, supported by comprehensive set of castings (available from Hemingway's in the UK http://www.hemingwaykits.com/acatalog/The_Seal___Edgar_T_Westbury.html
Since I have been a little unwell the total amount of work done today was to laminate the article pages, check castings over to see the tolerances (which are huge!). I also got to use one of my new Christmas presents, a granite surface plate. However I wouldn't call it a real start unless I turned some metal (that's not a true statement in my mind -preparation pays). Also I have been in correspondence with Steve Huck (camshaft fame) so thought that getting the camshaft made would get one large hurdle out of the way now.
So I turned down a steel bar to 0.500" for 5". Yup, that's as far as I got. I didn't trust myself to play with any castings but I have more than one steel bar. Anyway a couple of photo's are always usefull.........
Quite a large tolerance for the head and base cuts......
The start of the camshaft.........
However I have a couple of questions to ask of you...........
1) The granite surface plate seems to be scratching, however lightly......is this normal?
2) Would you fly cut the cylinder block on the milling machine or turn it on a face plate on a lathe?
Anyway....its a start.......
Having said that, it is a well known design, supported by comprehensive set of castings (available from Hemingway's in the UK http://www.hemingwaykits.com/acatalog/The_Seal___Edgar_T_Westbury.html
Since I have been a little unwell the total amount of work done today was to laminate the article pages, check castings over to see the tolerances (which are huge!). I also got to use one of my new Christmas presents, a granite surface plate. However I wouldn't call it a real start unless I turned some metal (that's not a true statement in my mind -preparation pays). Also I have been in correspondence with Steve Huck (camshaft fame) so thought that getting the camshaft made would get one large hurdle out of the way now.
So I turned down a steel bar to 0.500" for 5". Yup, that's as far as I got. I didn't trust myself to play with any castings but I have more than one steel bar. Anyway a couple of photo's are always usefull.........
Quite a large tolerance for the head and base cuts......
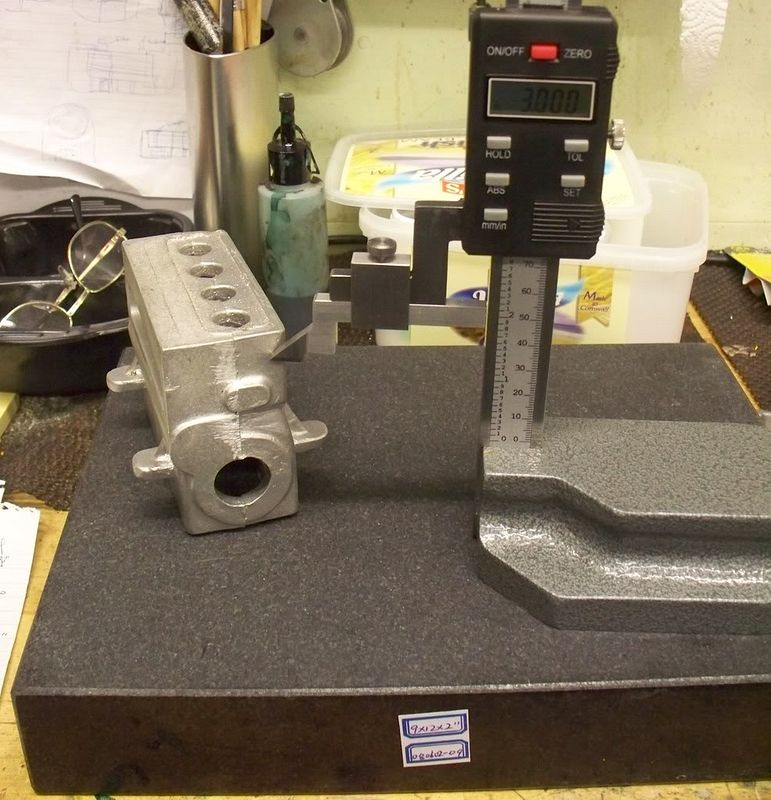
The start of the camshaft.........
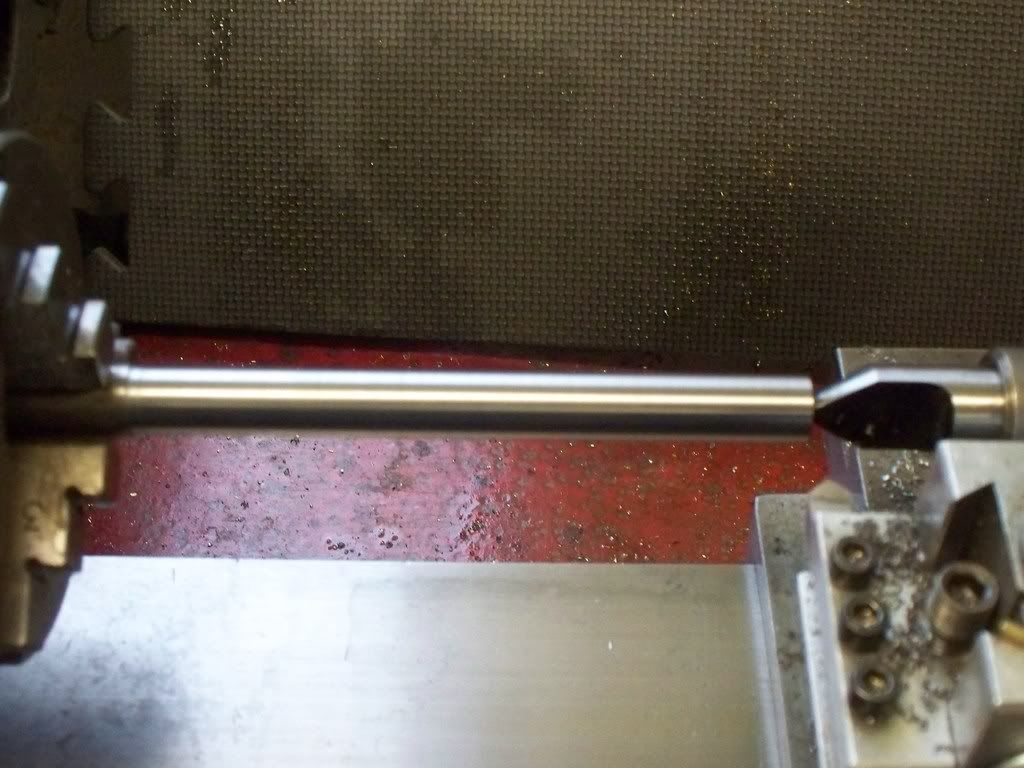
However I have a couple of questions to ask of you...........
1) The granite surface plate seems to be scratching, however lightly......is this normal?
2) Would you fly cut the cylinder block on the milling machine or turn it on a face plate on a lathe?
Anyway....its a start.......