Metal Mickey
Well-Known Member
- Joined
- Jul 5, 2008
- Messages
- 612
- Reaction score
- 6
I am making a long lever for my Fowler A7 2" scale traction engine and after milling one side of the lever, after releasing it form the clamps it had bowed.
I remember reading somewhere that this could be caused by tension in the metal and heating it and letting it cool down slowly would remove these stresses.
After heating.......
it returned to normal with no hitting with a big or small hammer.......
Did I do the right thing? Did I cause the problem when I milled it? I took light cuts because of the clamping and used cutting oil. I was not conscious of generating a great deal of heat........
Whilst there isn't a problem with the outcome I would like to know what happend, why and what I should do in future......
I remember reading somewhere that this could be caused by tension in the metal and heating it and letting it cool down slowly would remove these stresses.
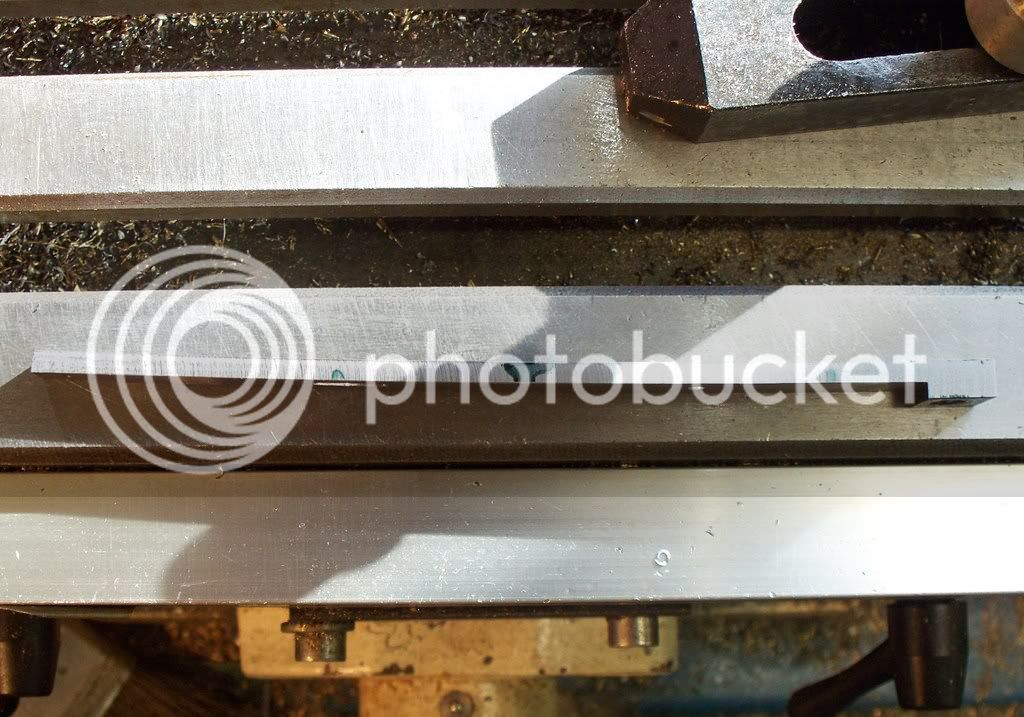
After heating.......
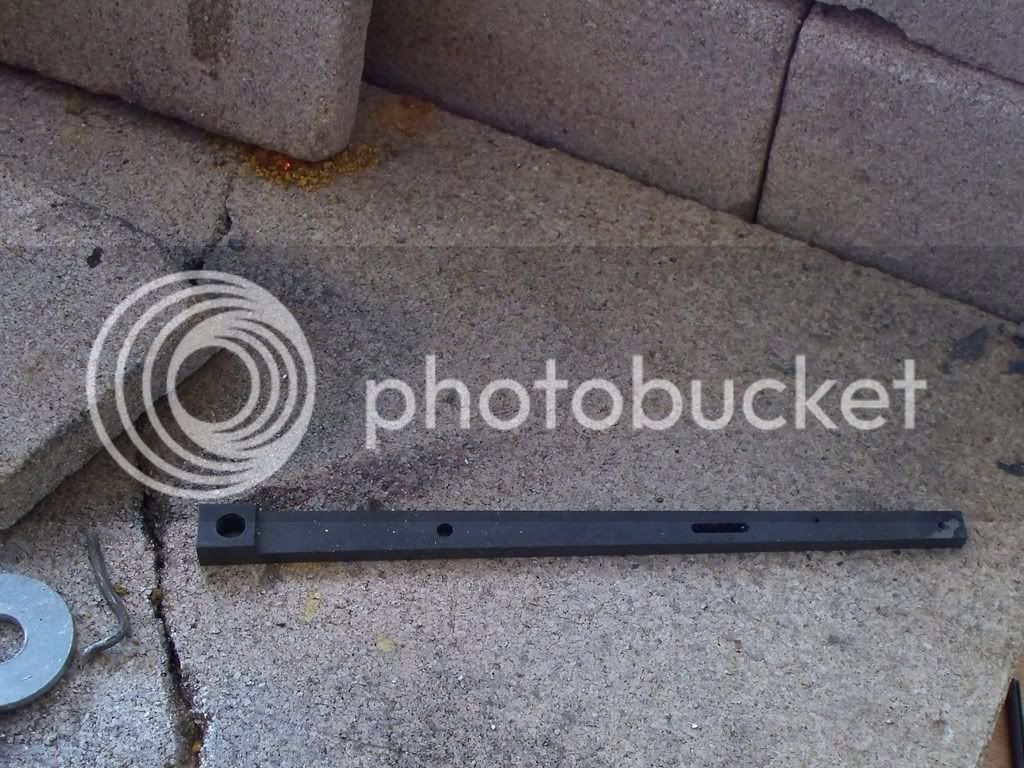
it returned to normal with no hitting with a big or small hammer.......
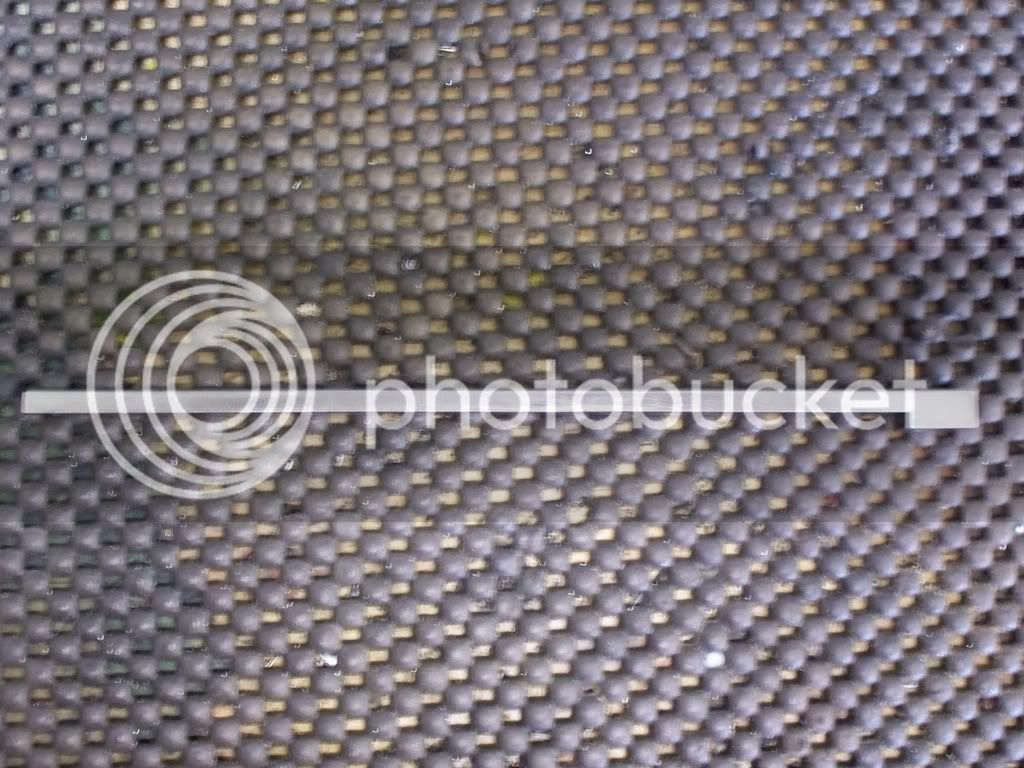
Did I do the right thing? Did I cause the problem when I milled it? I took light cuts because of the clamping and used cutting oil. I was not conscious of generating a great deal of heat........
Whilst there isn't a problem with the outcome I would like to know what happend, why and what I should do in future......