My first engine build.
I have been wanting to build an IC engine for years, never had the time or tools to do this. Last year I got myself a lathe and this year got myself a mill.
Now I have the tools, I looked for a simpleish build I came across the Upshur Single Vertical 4 stroke engine and ordered all the back issues of Strictly IC that cover the build.
Now with all the plans, read everything I could find on it I got to work. First thing I do not work with imperial very well so started to convert everything to metric. Lots of discussion on here about how to do the conversion, ended up leaving some of what I call the critical stuff, piston, crank, crank shaft, cams etc in imperial and the rest to metric.
Even though I was determined to build it as the plans and not to change anything I ended up changing a few bits before I even started. First thing was the main body crank case. The plans show six separate parts to the body plus extra parts to make the gear cover that sticks out the side, I have cut that down to two parts by making almost a casting from a solid block and making a cover (back). In doing this I cant make the cylinder as the plans as it was to solder onto the top cover. This is good as I did not like the idea of this anyway and made up the fins to come all the way down to bolt onto the main body, this also allows me to make the cylinder out of cast iron as it now just a liner.
So a couple of significant changes to the build, the other change was to replace the bearings on the two shafts with ball races, I had a big selection in the draw and was a simple (ish) task and as the bearings where quite thin there was enough room to counter bore then in from the inside of the housing.
First entry - The crank case
Take one big chunk of Ali
Cut a lump off, (must buy a bandsaw, that was hard work..)
Trim it all up on the mill and the cover all to size
Start milling out the inside
Until you get this
Then start forming space for the gear
end up with this
Then start shaping the outside
Finaly I ended up with
and with the cover off
It's a start, more photos and updates soon.
Dave
I have been wanting to build an IC engine for years, never had the time or tools to do this. Last year I got myself a lathe and this year got myself a mill.
Now I have the tools, I looked for a simpleish build I came across the Upshur Single Vertical 4 stroke engine and ordered all the back issues of Strictly IC that cover the build.
Now with all the plans, read everything I could find on it I got to work. First thing I do not work with imperial very well so started to convert everything to metric. Lots of discussion on here about how to do the conversion, ended up leaving some of what I call the critical stuff, piston, crank, crank shaft, cams etc in imperial and the rest to metric.
Even though I was determined to build it as the plans and not to change anything I ended up changing a few bits before I even started. First thing was the main body crank case. The plans show six separate parts to the body plus extra parts to make the gear cover that sticks out the side, I have cut that down to two parts by making almost a casting from a solid block and making a cover (back). In doing this I cant make the cylinder as the plans as it was to solder onto the top cover. This is good as I did not like the idea of this anyway and made up the fins to come all the way down to bolt onto the main body, this also allows me to make the cylinder out of cast iron as it now just a liner.
So a couple of significant changes to the build, the other change was to replace the bearings on the two shafts with ball races, I had a big selection in the draw and was a simple (ish) task and as the bearings where quite thin there was enough room to counter bore then in from the inside of the housing.
First entry - The crank case
Take one big chunk of Ali
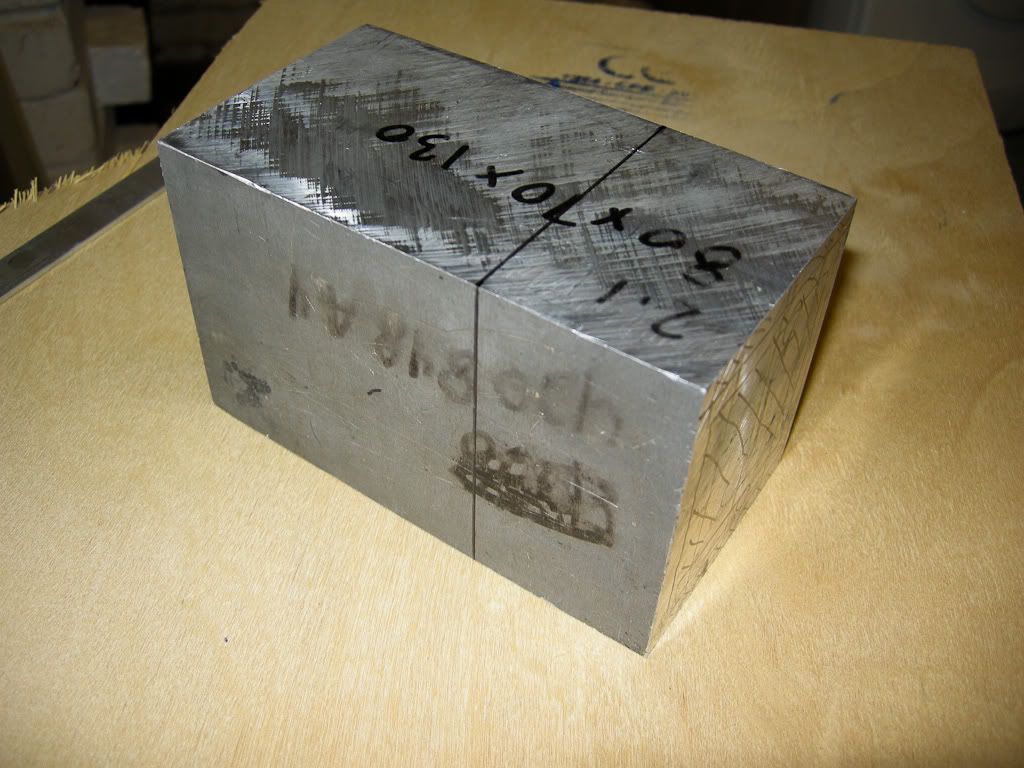
Cut a lump off, (must buy a bandsaw, that was hard work..)
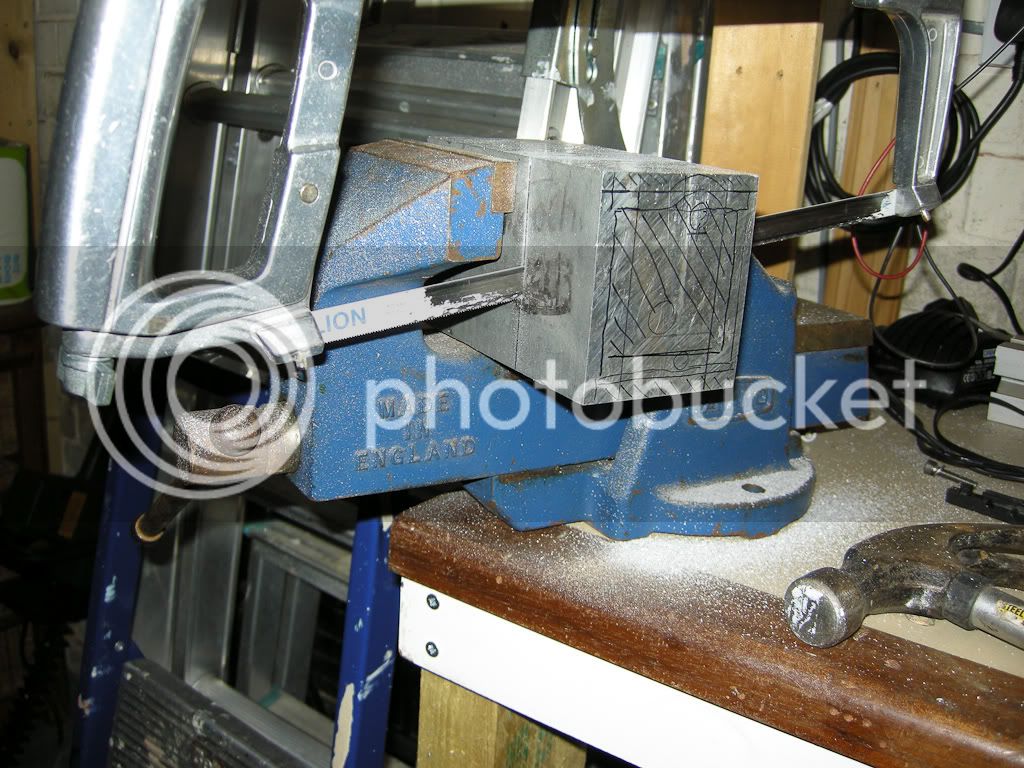
Trim it all up on the mill and the cover all to size
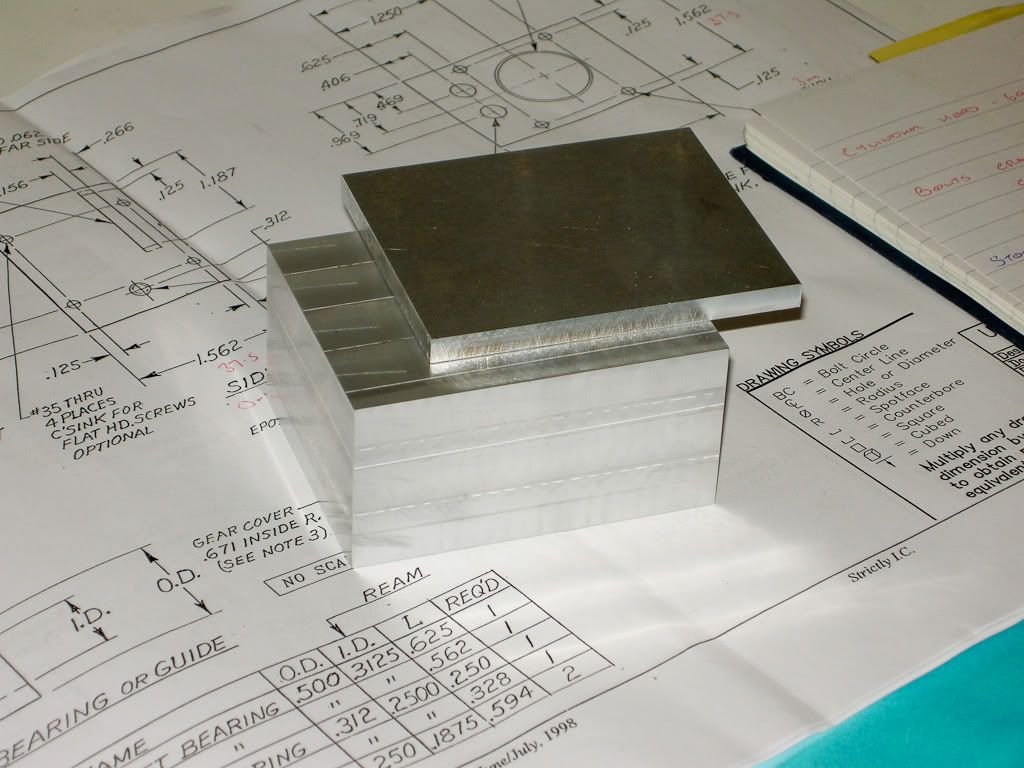
Start milling out the inside
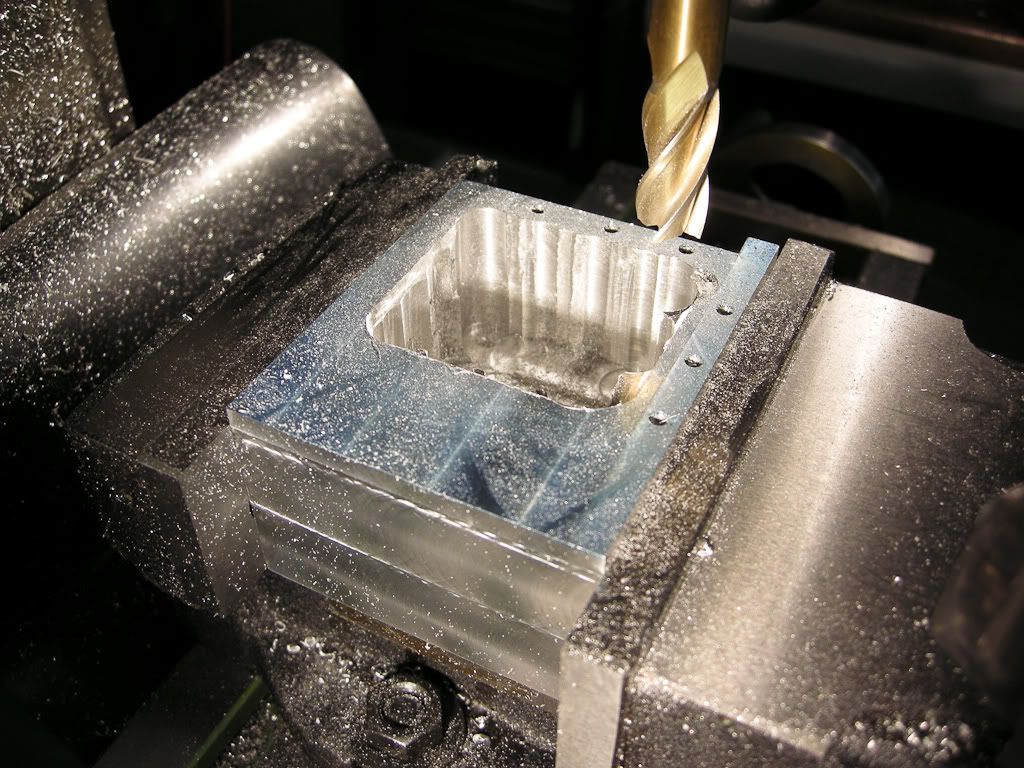
Until you get this
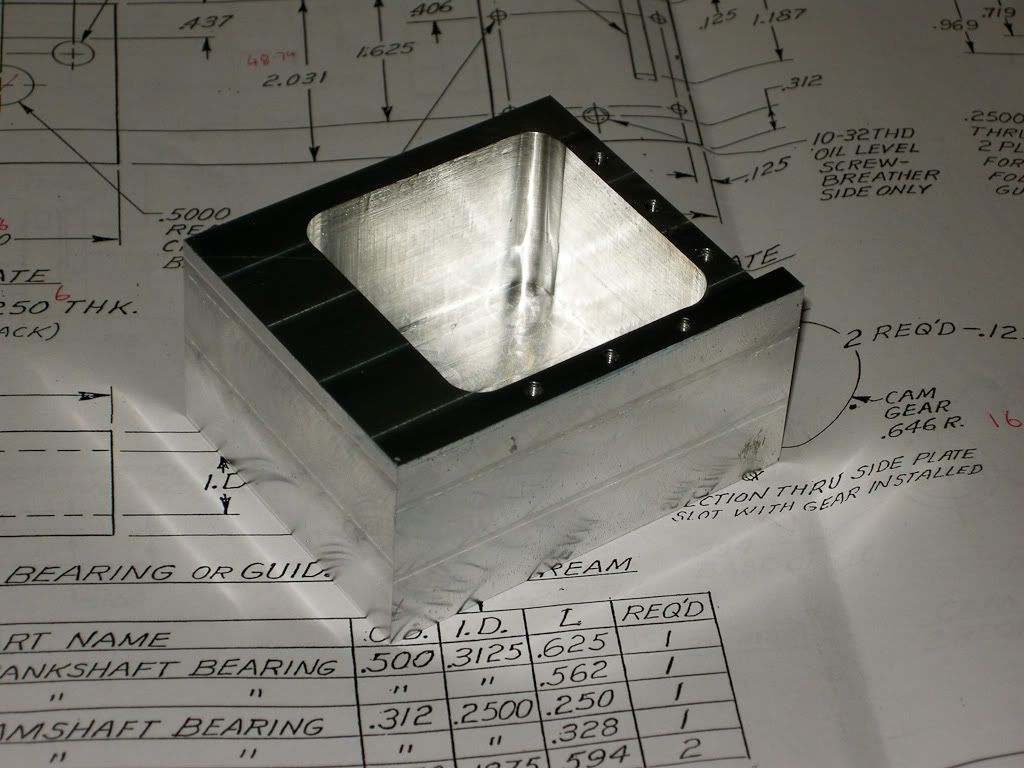
Then start forming space for the gear
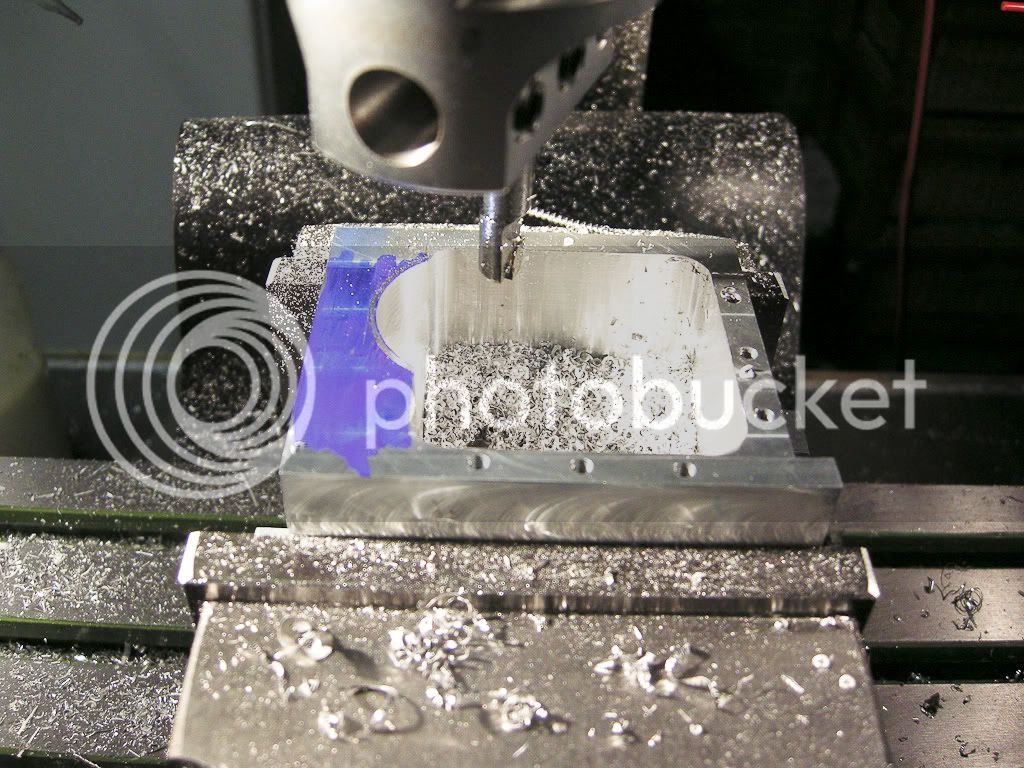
end up with this
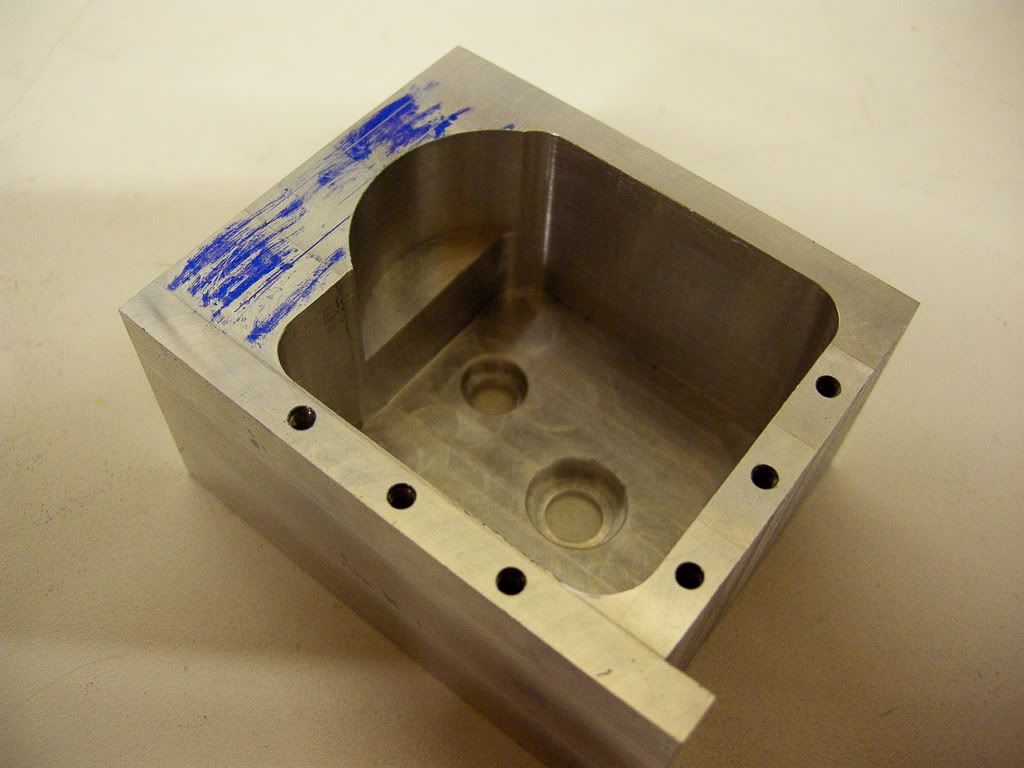
Then start shaping the outside
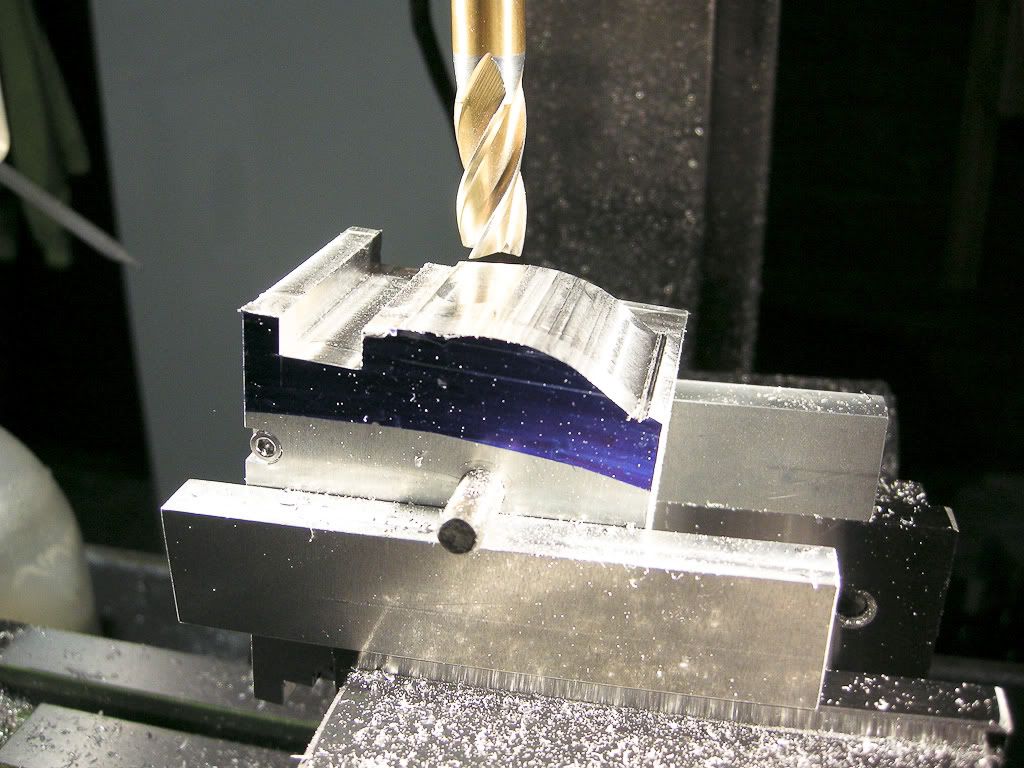
Finaly I ended up with
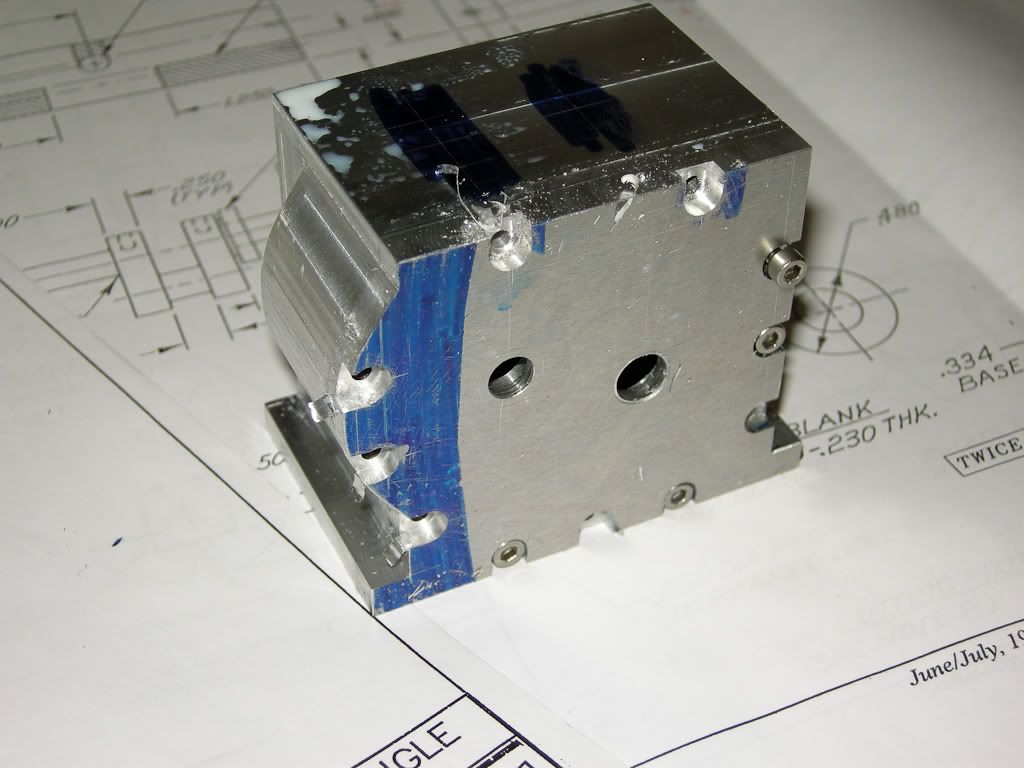
and with the cover off
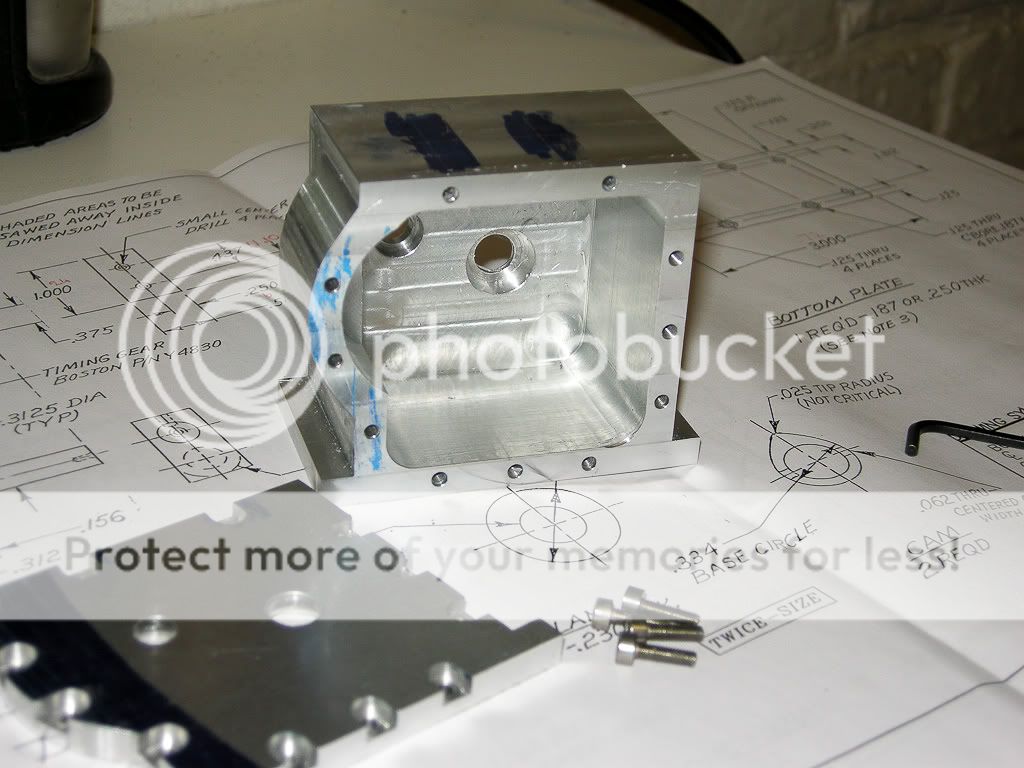
It's a start, more photos and updates soon.
Dave