I needed to put a 6" diameter hole in some 3/16" thick steel plates today. These are nothing critical, none of the dimensions are fussy, they are just support plates for machinery. I've made stuff like this in the mill by laying out the hole and cutting close to the line with an end mill, then taking a clean-up cut with the boring head. I figured that was a waste of material for a 6" hole, so I trepanned them on the lathe.
Since these plates weren't fussy, I just scribed a line corner to corner and used the tailstock center as a reference to line up the intersection of the lines on center in the four jaw chuck.
I dug out a HSS tool that was close to what I wanted and dressed it up a little. It looks basically like a parting tool, but you need to watch the side clearance angles. The side toward the center of the hole isn't too much of a problem, but the side toward the outer diameter needs a little more clearance to avoid dragging. I get away from some of the clearance problems by grinding the bottom of the tool away.
The pic doesn't show it too well, but there is a land below the cutting edge that has a lot less clearance to help support the cutting edge. A word of caution about a tool ground this way; it is very easy to over feed and make the tool dig in and break or pull your work out of the chuck.
A quick eyeball on the diameter and plunge in a few thousandths to get a witness line gets a starting point. I measured the first cut and just moved the cross-slide out what I needed by using the dial.
Plunge in to make another witness line to verify my size, and then have at it.
Low speed, a steady feed, and brushing on some sulphurized cutting oil occasionally, and it cut right through. The slug will usually just drop back into the chuck and rattle around a bit, but turning slow like this, it usually stays in there. This slug was big enough that it couldn't get out anyway.
Just a note on the tool, if you angle the cutting edge slightly, you can control where the burr ends up. I angled the edge so the outer diameter cut through first and the burr was on the inner scrap piece.
So, in the end, my 6" hole to size, and another piece of steel for the scrap bin to be used for other things, all in one pass.
I use this method a good bit to save material.
It's a little scary at first, but taking your time with the setup and grinding the tool makes it pretty much routine. Just be extra careful on the break-through though. Like drilling thin material, the tool can grab and ruin your day, so lighten up on the feed when it starts to go through.
Kevin
Since these plates weren't fussy, I just scribed a line corner to corner and used the tailstock center as a reference to line up the intersection of the lines on center in the four jaw chuck.
I dug out a HSS tool that was close to what I wanted and dressed it up a little. It looks basically like a parting tool, but you need to watch the side clearance angles. The side toward the center of the hole isn't too much of a problem, but the side toward the outer diameter needs a little more clearance to avoid dragging. I get away from some of the clearance problems by grinding the bottom of the tool away.

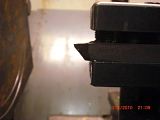
The pic doesn't show it too well, but there is a land below the cutting edge that has a lot less clearance to help support the cutting edge. A word of caution about a tool ground this way; it is very easy to over feed and make the tool dig in and break or pull your work out of the chuck.
A quick eyeball on the diameter and plunge in a few thousandths to get a witness line gets a starting point. I measured the first cut and just moved the cross-slide out what I needed by using the dial.

Plunge in to make another witness line to verify my size, and then have at it.
Low speed, a steady feed, and brushing on some sulphurized cutting oil occasionally, and it cut right through. The slug will usually just drop back into the chuck and rattle around a bit, but turning slow like this, it usually stays in there. This slug was big enough that it couldn't get out anyway.

Just a note on the tool, if you angle the cutting edge slightly, you can control where the burr ends up. I angled the edge so the outer diameter cut through first and the burr was on the inner scrap piece.
So, in the end, my 6" hole to size, and another piece of steel for the scrap bin to be used for other things, all in one pass.
I use this method a good bit to save material.
It's a little scary at first, but taking your time with the setup and grinding the tool makes it pretty much routine. Just be extra careful on the break-through though. Like drilling thin material, the tool can grab and ruin your day, so lighten up on the feed when it starts to go through.
Kevin