Powder keg
Well-Known Member
- Joined
- Oct 10, 2007
- Messages
- 1,091
- Reaction score
- 3
WARNING - BEFORE GOING ANY FURTHER, PART OF THIS POST IS ABOUT USING MOLTEN OR HOT METAL. IF YOU DO NOT KNOW ALL THE SAFETY PRECAUTIONS AND CORRECT PROTECTIVE EQUIPMENT THAT THIS ENTAILS, AND YOU ARE NOT WILLING TO FOLLOW ALL THE CORRECT PROCEDURES WHEN HANDLING MOLTEN OR HOT METALS, DO NOT TRY ANY OF THE HOT METAL PROCEDURES MENTIONED IN THIS POST. THE SAFETY PRECAUTIONS IN THIS POST MIGHT NOT BE CORRECT, IT IS UP TO YOURSELF TO FAMILIARISE YOURSELF WITH THE CORRECT ONES.
NO-ONE ON THIS SITE CAN BE HELD RESPONSIBLE FOR ANY OF YOUR ACTIONS IF YOU HURT YOURSELF.
THIS WARNING WAS ADDED BY ADMINISTRATION OF THIS SITE.
While I'm going to school, I'm trying to take advantage of what is there. They have the full blown version of Mastercam and some neat machines. I've always admired those gorgeous flywheels with unique spokes. I decided to design and machine my own. This flywheel is 5.125" in diameter. I'm going to try and make one that is 3.0625 next week with the same drawing.
Here is the flywheel appearing out of the wood.
I'm a little deeper now. The spokes are starting to appear. This is still in rough cutting mode. I am taking .125" deep X .125" wide cuts with a .250" Dia. ball end mill.
Here the finish passes are started. There are many back and forth movements! I think only .025" was left overall for cleanup.
Here is an overall view.
After this was done I mirrored the image and made the reverse so I would have a 2 part pattern. It took 3 hours to machine the 2 half's. I'll post some more pictures soon.
I would be interested in seeing any pictures of unique flywheels.
Later, Wes
NO-ONE ON THIS SITE CAN BE HELD RESPONSIBLE FOR ANY OF YOUR ACTIONS IF YOU HURT YOURSELF.
THIS WARNING WAS ADDED BY ADMINISTRATION OF THIS SITE.
While I'm going to school, I'm trying to take advantage of what is there. They have the full blown version of Mastercam and some neat machines. I've always admired those gorgeous flywheels with unique spokes. I decided to design and machine my own. This flywheel is 5.125" in diameter. I'm going to try and make one that is 3.0625 next week with the same drawing.
Here is the flywheel appearing out of the wood.
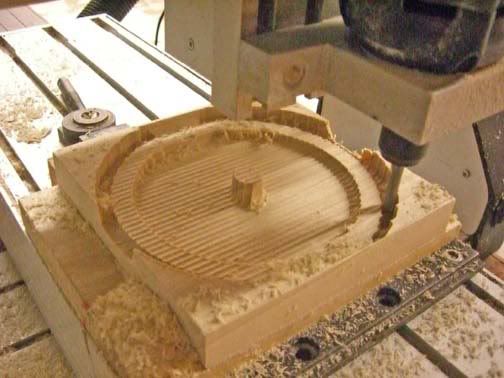
I'm a little deeper now. The spokes are starting to appear. This is still in rough cutting mode. I am taking .125" deep X .125" wide cuts with a .250" Dia. ball end mill.
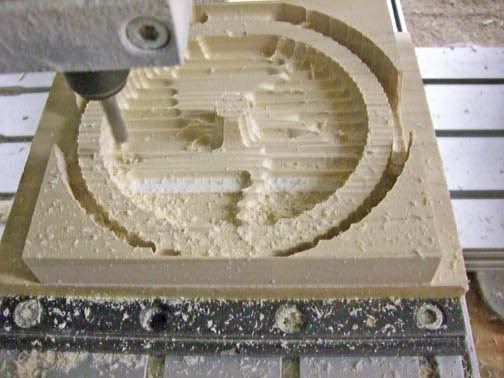
Here the finish passes are started. There are many back and forth movements! I think only .025" was left overall for cleanup.
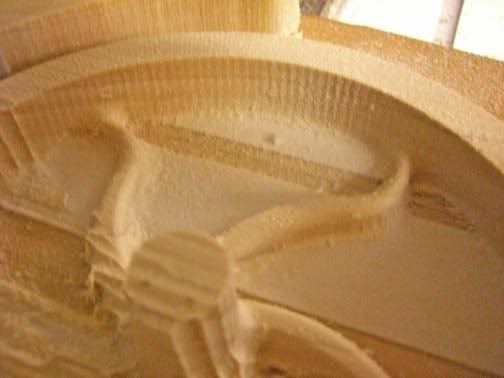
Here is an overall view.
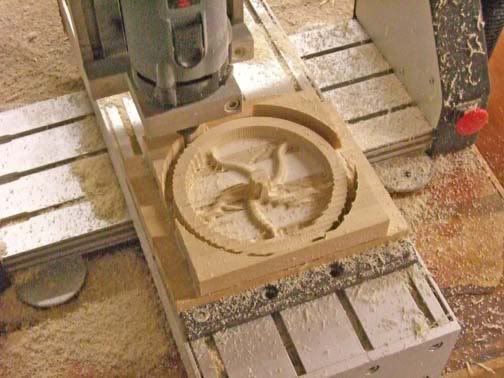
After this was done I mirrored the image and made the reverse so I would have a 2 part pattern. It took 3 hours to machine the 2 half's. I'll post some more pictures soon.
I would be interested in seeing any pictures of unique flywheels.
Later, Wes