I want to post this picture for two reasons, I did it and all you fellow helped me get to the point where it was possible, starting back early when Rick and other helped me through the fear of threading, you all said it was easy but I could not see that at the time but practice did bring me to the point that I am able to dive in now, still would like to get the picking up threads but that will come, my thanks to all of you for the help and still learning in my shop and here twice a day, this is a lot better that the news, I can learn here, I wanted to test a Kabota engine on my scag mower, it won't start and thing the compression might be low, went to Harbor Freight and got the compression tester, with all the crossovers there was not one to fit the Kabota engine, what will I do, make one the fellow on the page makes everything, put the short brass in the Mini Lathe, change gears set to 1.5 MM, cut the internal threads till the injector threaded in, put the brass in and turned it till it fit the female, cut the Hex on the mill and drill through with the threads to accept the gauge, don't really know if that is they was it should be done but most of that I learned here the
right things that is, so with all that said, thanks to all who share because you do care about helping people along to learn, this is the fruits of your labor, thanks again, Lathe Nut
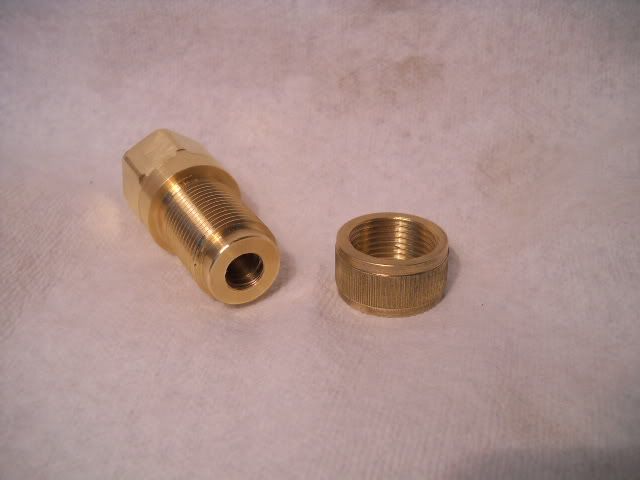