CallMeAL
Member
- Joined
- Mar 29, 2008
- Messages
- 118
- Reaction score
- 40
Hello,
In my wandering on the net and in tool catalogs, I have seen various renditions of a tapping guide machines. I thought it would be interesting to try to make one, more of a challenge to use my foundry and machine tools rather than something I really need. My intention is to cast a guide arm that will attach to the column of my drill press and use the adjustable table to allow a great deal of flexibility. Also, since I have a small shop, I will be able to combine two tools in one without taking up a lot more space!
Here is the model of the pattern I came up with in Sketchup:
I chopped up some scrap wood to turn parts for this pattern
This will be a split pattern so here is what the glue up looks like with a sheet of paper glue into the mid-line.
Here is the main body turned with the ends left square so I could drill the hole for the arm with the biggest forester bit I have.
The other two pieces of the split pattern.
Hole drilled for the arm and test fit.
Ends trimmed off, patterns split apart, and glued up. Locating dowel holes were drilled before splitting apart.
The holes were drilled into the protrusions for the core print.
Pattern glued up.
.
Sanded, a little spackle filler in places, and primer applied.
Glued up the core box and drilled out the hole with the same forester bit.
Mixed up some sand and sodium silicate, tamped it into the core box, and put it in a plastic bag with CO2 from my wire feed welder and made the core for the hole in the casting for the drill press column. The hole in the center is to allow the CO2 get into the middle of the core.
Now that I have the pattern done I hope to ram it up and cast the arm tomorrow. It's a long process to get to this point, but if the pour goes well it is worth it. It's fun to see the casting come out of the sand!
More to come!
Thanks for your interest.
In my wandering on the net and in tool catalogs, I have seen various renditions of a tapping guide machines. I thought it would be interesting to try to make one, more of a challenge to use my foundry and machine tools rather than something I really need. My intention is to cast a guide arm that will attach to the column of my drill press and use the adjustable table to allow a great deal of flexibility. Also, since I have a small shop, I will be able to combine two tools in one without taking up a lot more space!
Here is the model of the pattern I came up with in Sketchup:
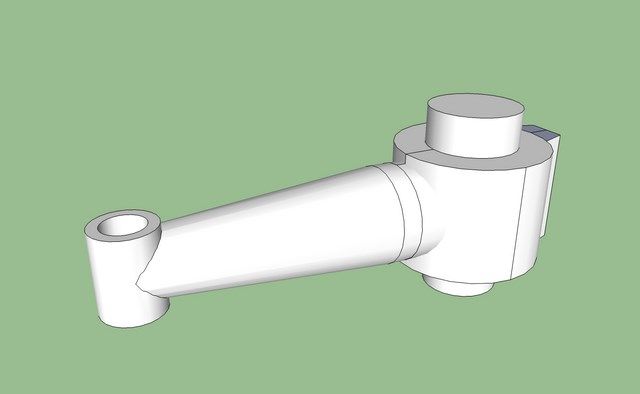
I chopped up some scrap wood to turn parts for this pattern
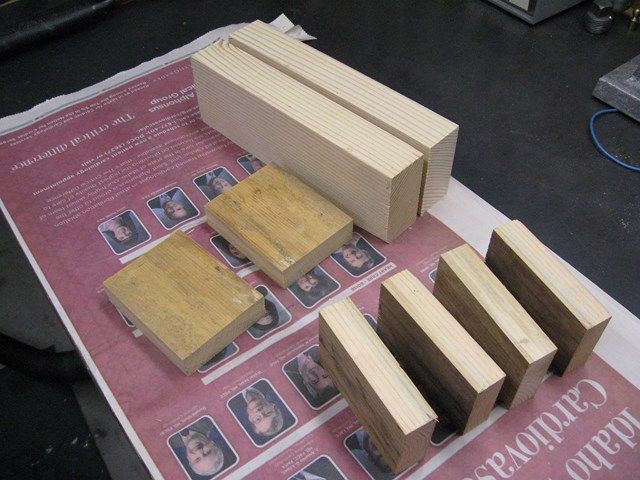
This will be a split pattern so here is what the glue up looks like with a sheet of paper glue into the mid-line.
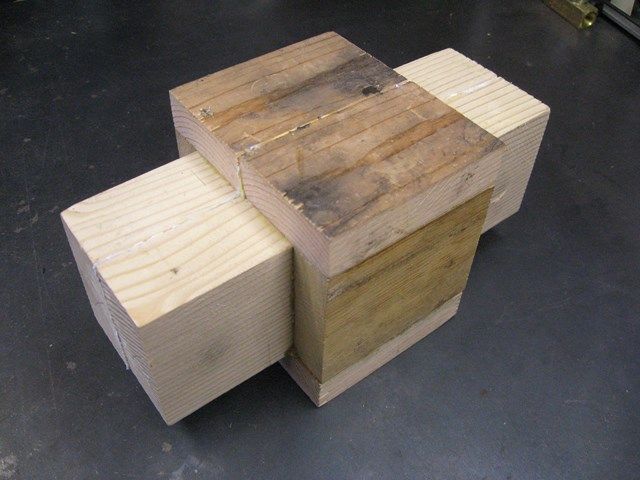
Here is the main body turned with the ends left square so I could drill the hole for the arm with the biggest forester bit I have.
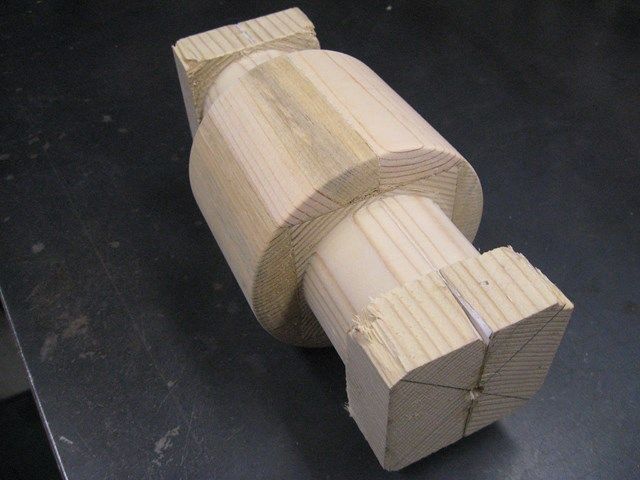
The other two pieces of the split pattern.
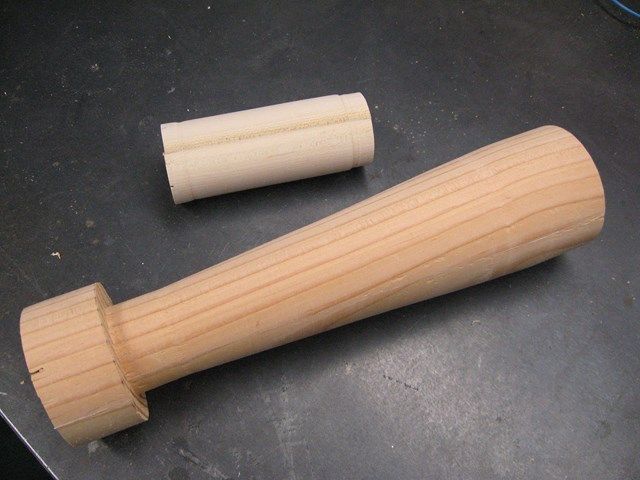
Hole drilled for the arm and test fit.
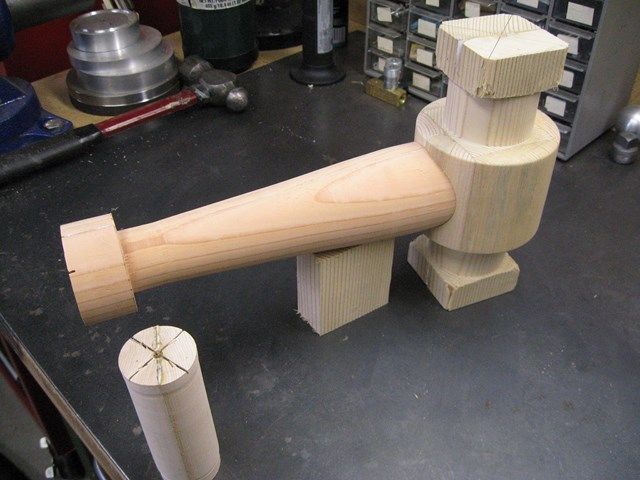
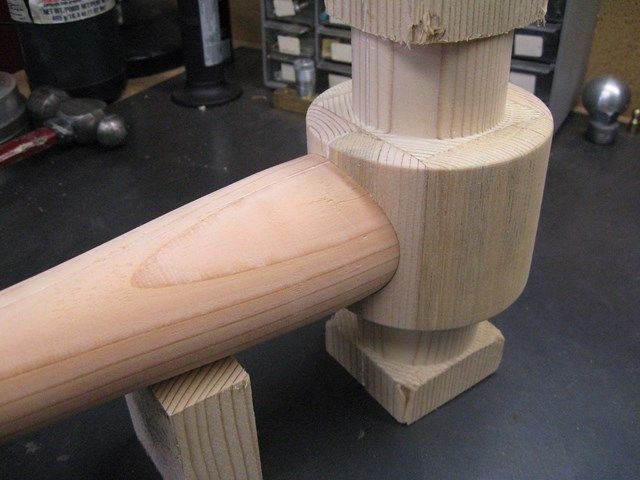
Ends trimmed off, patterns split apart, and glued up. Locating dowel holes were drilled before splitting apart.
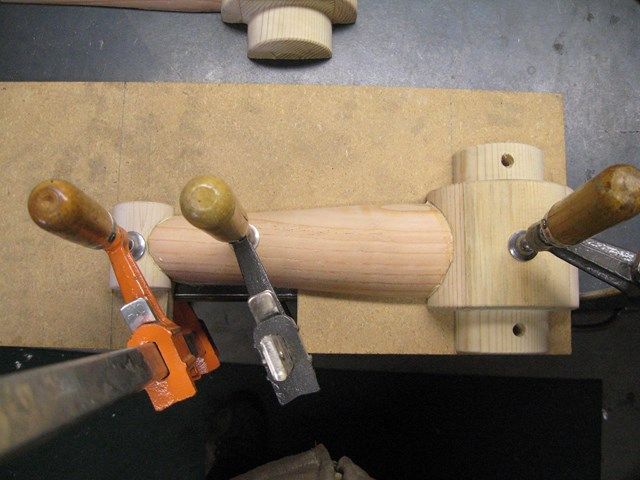
The holes were drilled into the protrusions for the core print.
Pattern glued up.
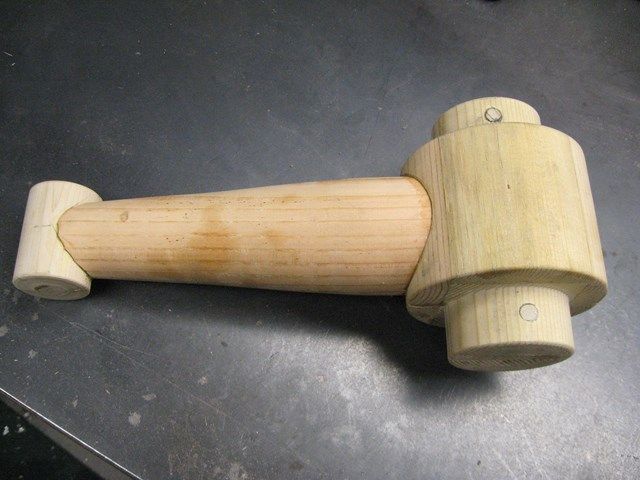

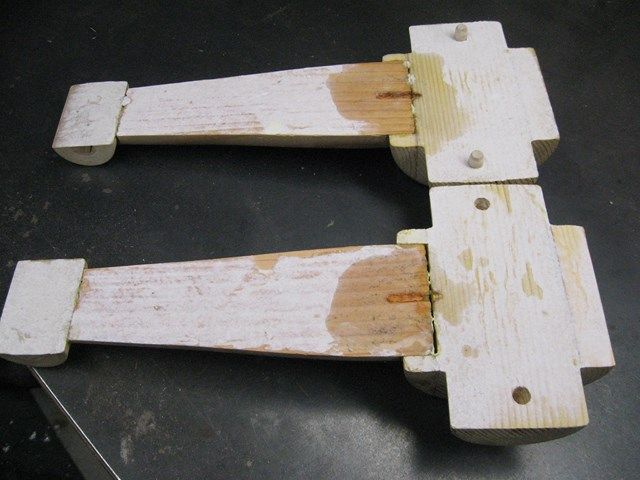
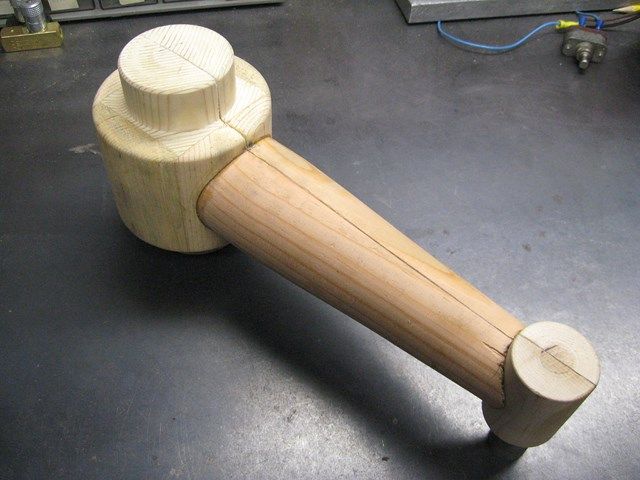
Sanded, a little spackle filler in places, and primer applied.
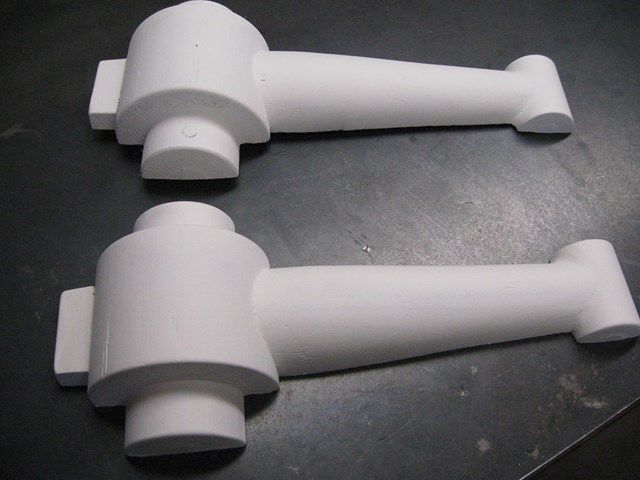
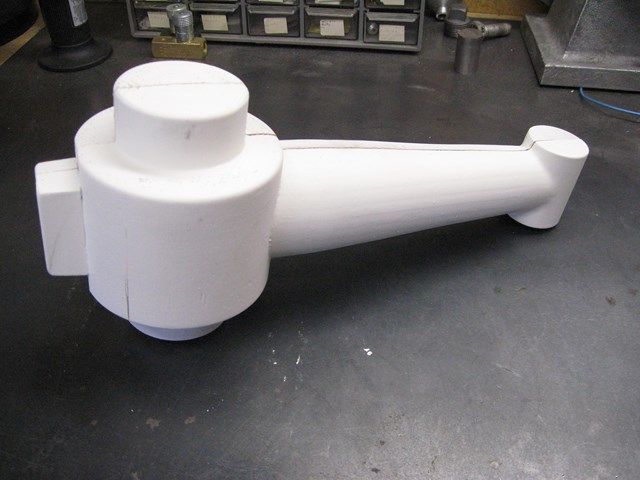
Glued up the core box and drilled out the hole with the same forester bit.
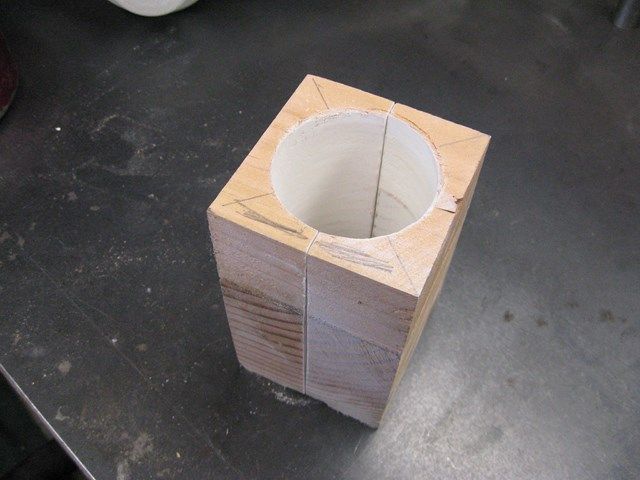
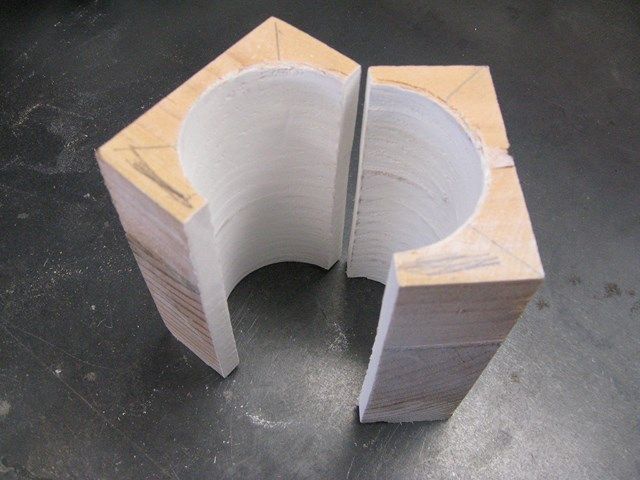
Mixed up some sand and sodium silicate, tamped it into the core box, and put it in a plastic bag with CO2 from my wire feed welder and made the core for the hole in the casting for the drill press column. The hole in the center is to allow the CO2 get into the middle of the core.
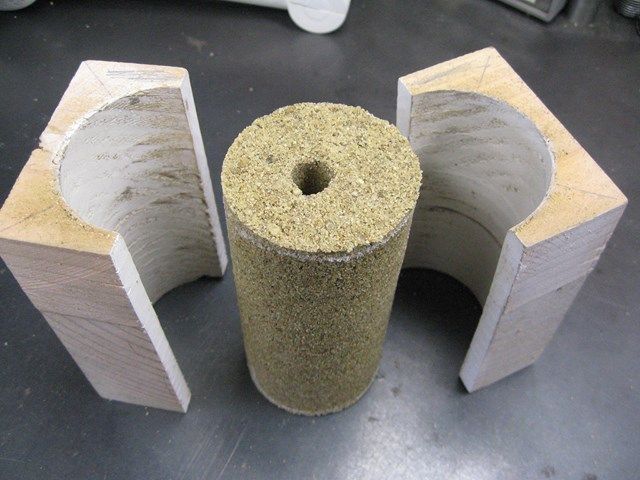
Now that I have the pattern done I hope to ram it up and cast the arm tomorrow. It's a long process to get to this point, but if the pour goes well it is worth it. It's fun to see the casting come out of the sand!
More to come!
Thanks for your interest.