I am pleased with my new CX601 mill from BusyBee, in spite of a few initial "teething" problems. (Which were solved by removing the pin inside the spindle that mates with an R8 shank.) I purchased a set of 2 axis DRO's from DroPro in California, and almost immediately regretted not buying one for the Z or vertical axis. The mill comes equipped with a digital readout on the Z axis, but it is small and very difficult to see. I had some idle time this week, so I set out to solve the lighting issue with an $8 LED light with a semi-flexible "neck". While deciding how to mount it, I made the decision to get rid of the clear lexan chip guard on the front of the machine, and make a bracket for the light which would pick up the holes that had originally held the guard support in place. While I was at it, I decided to add a vertical depth stop similar to the one I had built on my previous bench top mill. I find this a very worthwhile addition to this type of mill. I will take you step by step through what I am doing in case you have a similar mill and wish to add an adjustable depth stop.

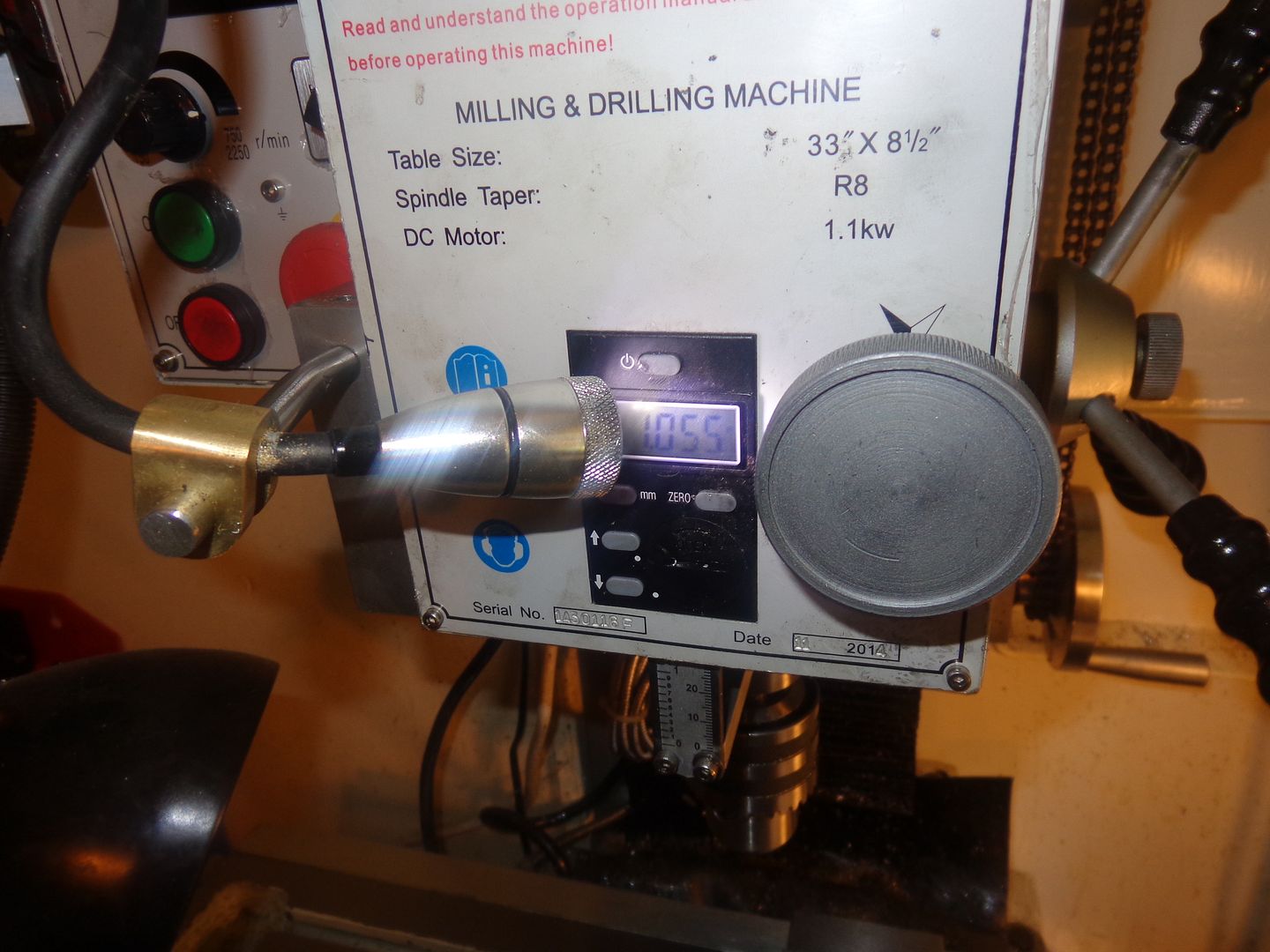
Last edited: