- Joined
- Oct 1, 2010
- Messages
- 1,342
- Reaction score
- 395
Now to post some pictures of my shop. I have a garage that accommodates 3 small cars I play with and whatever else I do that makes noise and a mess. (I work on electronics and other things in the house, which has climate control which the garage does not.)
The 7 x 14 Lathe and mill have benches with storage underneath.
Magnifier Lamp is flange-mounted to lathe bench to cover either machine
"Everything" Workbench is opposite Lathe. I spill things, paint, screw down projects, cut and drill as the work flows, top is made from two-by planks attached underneath so I never worry about hitting a nail with a precision edge. I periodically clean, scrape, and re-plane the top and will replace it when it gets too bad: This one is 20 years old.
Second bench is to left of main bench and the same height: Great for long lengths of whatever. Small Radial-arm saw was bought before miter saws became popular, but it is great to have set up and ready to go.
T-slot rails embedded in this bench (New last year) allow clamping grinders and projects (and hopefully soon an engine).
Most-often-needed tools for all home and shop misc. needs are on the wall. Good Tools are in tool boxes.
QuickieBuilt cabinets under benches hold more tools and supplies close to where they are used.
I like these Durham drawer-boxes for some things plus attachments that may be used somewhere else, like the dremel.
Besides circuits dedicated to things like air compressor, I have two utility circuits that circle the whole place. Ivory and Brown outlets remind me to share the load between the two circuits.
I have more to share, but let's see if photobucket links work :
-----
(Later) Whaddayaknow: I got the wrong code and linked to my entire photobucket album. Gotta make sure to get the IMGs.
:'(
The 7 x 14 Lathe and mill have benches with storage underneath.
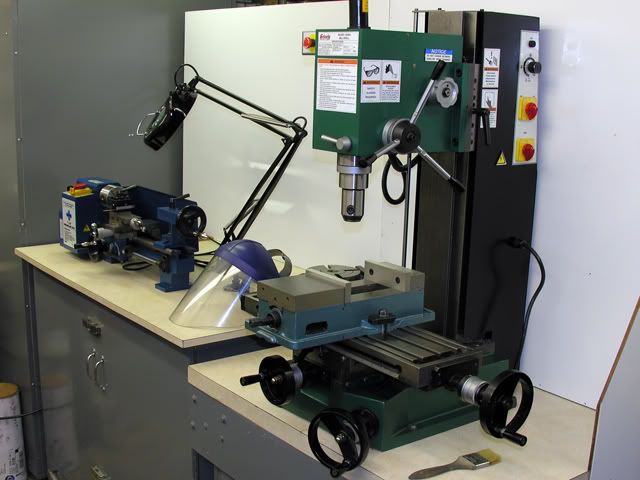
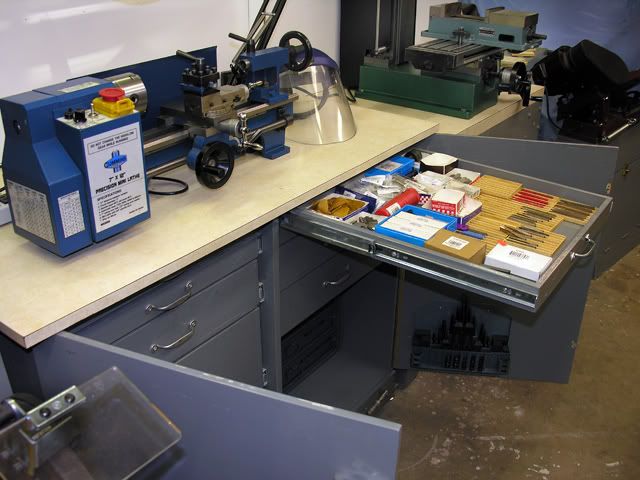
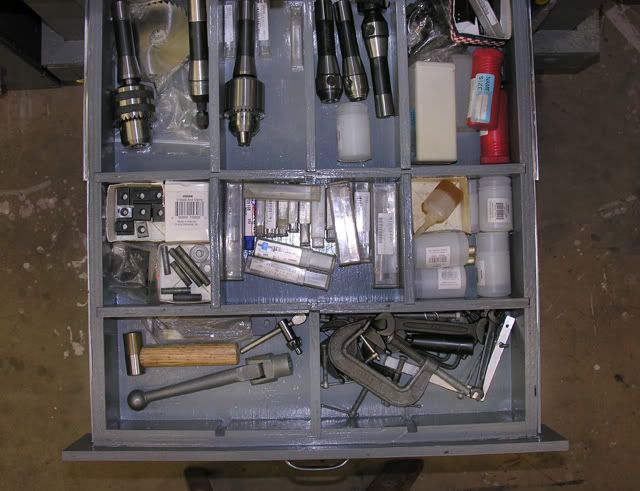
Magnifier Lamp is flange-mounted to lathe bench to cover either machine
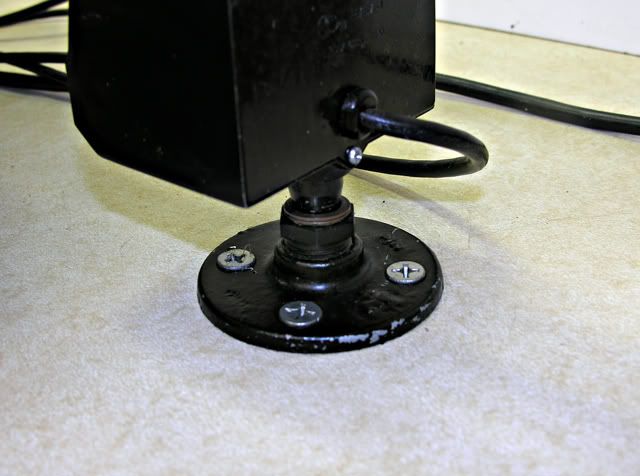
"Everything" Workbench is opposite Lathe. I spill things, paint, screw down projects, cut and drill as the work flows, top is made from two-by planks attached underneath so I never worry about hitting a nail with a precision edge. I periodically clean, scrape, and re-plane the top and will replace it when it gets too bad: This one is 20 years old.
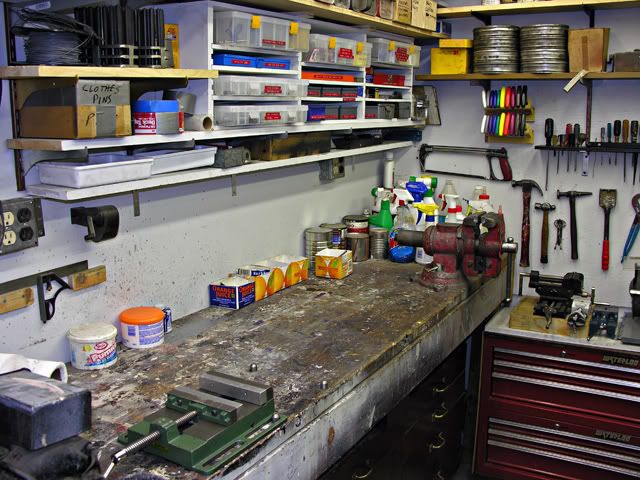
Second bench is to left of main bench and the same height: Great for long lengths of whatever. Small Radial-arm saw was bought before miter saws became popular, but it is great to have set up and ready to go.
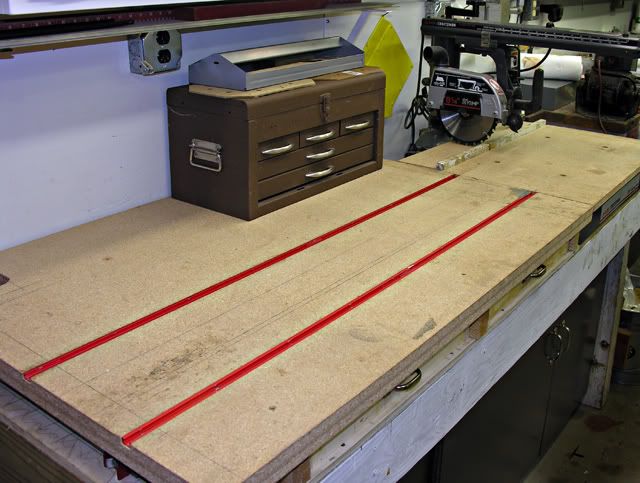
T-slot rails embedded in this bench (New last year) allow clamping grinders and projects (and hopefully soon an engine).
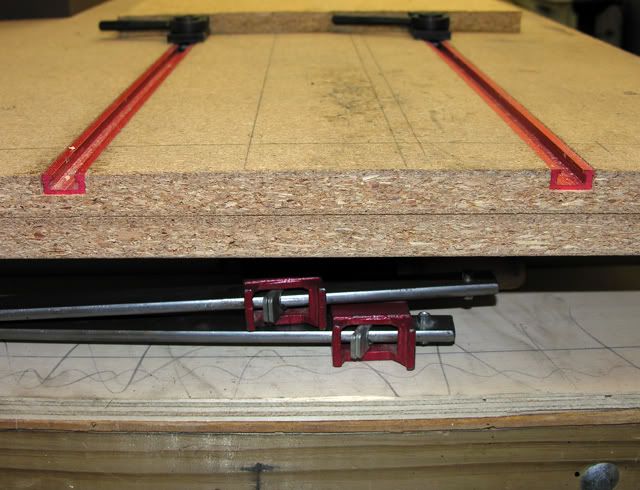
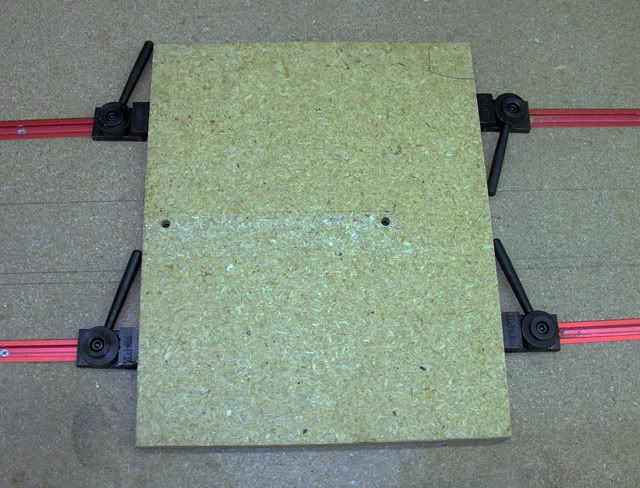
Most-often-needed tools for all home and shop misc. needs are on the wall. Good Tools are in tool boxes.
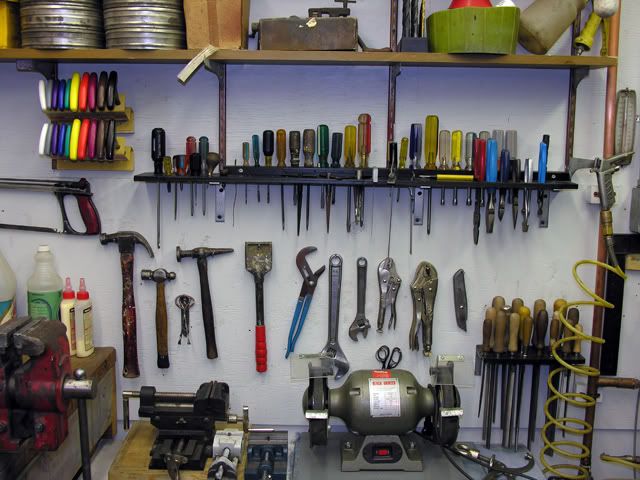
QuickieBuilt cabinets under benches hold more tools and supplies close to where they are used.
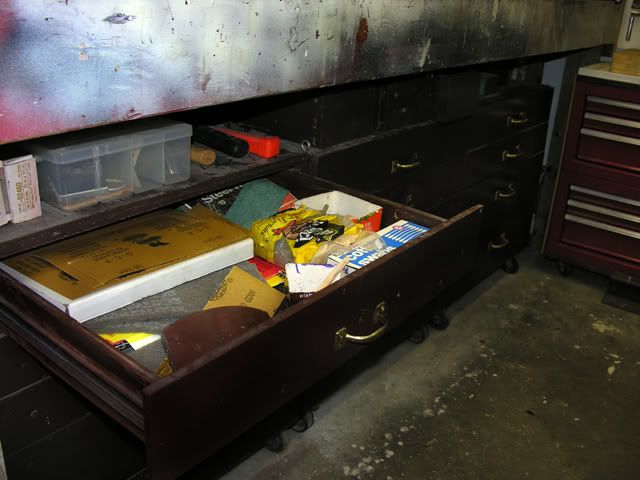
I like these Durham drawer-boxes for some things plus attachments that may be used somewhere else, like the dremel.
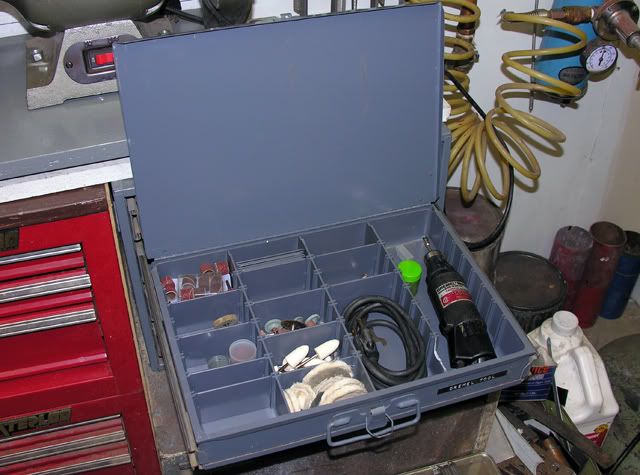
Besides circuits dedicated to things like air compressor, I have two utility circuits that circle the whole place. Ivory and Brown outlets remind me to share the load between the two circuits.
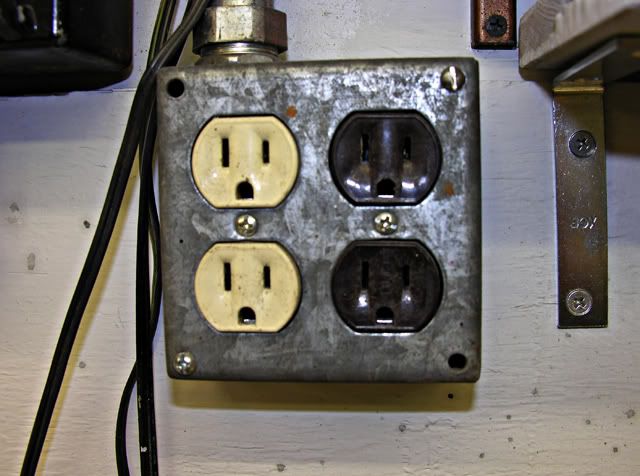
I have more to share, but let's see if photobucket links work :
-----
(Later) Whaddayaknow: I got the wrong code and linked to my entire photobucket album. Gotta make sure to get the IMGs.
:'(