So there I was, excited at using my rotary table my X2/C6 (Grizzly 0516) lathe/mill for the first time when without warning the spindle just slowed to a stop. Checked the speed control & emergency stop - still OK & the green "power" light was still on? Did the logical thing and turned it off then on again (because that usually fixes most electrical things
) - still nothing.
I had only been milling 6061 Al with a 3mm mill & fairly light cuts - but I had been going for 1/2 or so. Maybe the motor has overheated? - turned the power off for a length of time but still no signs of life when switched on??
It then occurred to me to check the fuse mounted in the front of the control box below the speed pot - blown! Of course it was a 3.15Amp fuse & the best I could managed in that size was a couple of 5amp ones - Oh well, worth a try. However in my excitement to get back to milling (combined with the el-cheapo fuse holder) on re-inserting the fuse there was that dreaded noise of breaking glass. Several minutes with the pointy nose pliers and some thin wire (& power off) I managed to extract the glass and insert a new fuse successfully.
Powered back up but still nothing - removed the new fuse and sure enough the wire was vapourised - Time to employ the help of Google!!!
After coming across this site http://www.raynerd.co.uk/?p=567 I recognised the symptoms I had - perhaps I had the same issue with a failing bridge rectifier - the electronic component responsible for converting the AC mains into a rectified (but 'rough') DC voltage.
Of course my lathe/mill is located up against the garage wall & the control board is mounted in the enclosure on the back of the machine - but with a couple of stubby screwdrivers & some stretching I managed to remove the board
Testing with a multimeter suggested that the rectifier could well be to blame as I could get continuity (0 ohm resistance) between one AC terminal and the + terminal with the meter leads in either polarity.
I unsoldered the rectifier to confirm the test out of the board & got the same results - so off to the electronics store the next day for a new rectifier (plus some fuses of the right rating)
The new rectifier was soldered into the board & reconnected to the mill & success :big: the mill was back to normal :big:
So there you have it - if you X2 mill stops unexpectedly & before rushing out to spend $160 for a replacement speed controller it might be worth trying to replace the rectifier first (total cost 10A rectifier + fuse $3.65).
Tony.
I had only been milling 6061 Al with a 3mm mill & fairly light cuts - but I had been going for 1/2 or so. Maybe the motor has overheated? - turned the power off for a length of time but still no signs of life when switched on??
It then occurred to me to check the fuse mounted in the front of the control box below the speed pot - blown! Of course it was a 3.15Amp fuse & the best I could managed in that size was a couple of 5amp ones - Oh well, worth a try. However in my excitement to get back to milling (combined with the el-cheapo fuse holder) on re-inserting the fuse there was that dreaded noise of breaking glass. Several minutes with the pointy nose pliers and some thin wire (& power off) I managed to extract the glass and insert a new fuse successfully.
Powered back up but still nothing - removed the new fuse and sure enough the wire was vapourised - Time to employ the help of Google!!!
After coming across this site http://www.raynerd.co.uk/?p=567 I recognised the symptoms I had - perhaps I had the same issue with a failing bridge rectifier - the electronic component responsible for converting the AC mains into a rectified (but 'rough') DC voltage.
Of course my lathe/mill is located up against the garage wall & the control board is mounted in the enclosure on the back of the machine - but with a couple of stubby screwdrivers & some stretching I managed to remove the board
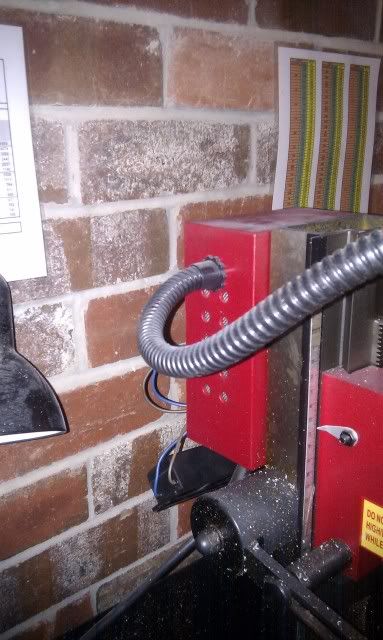
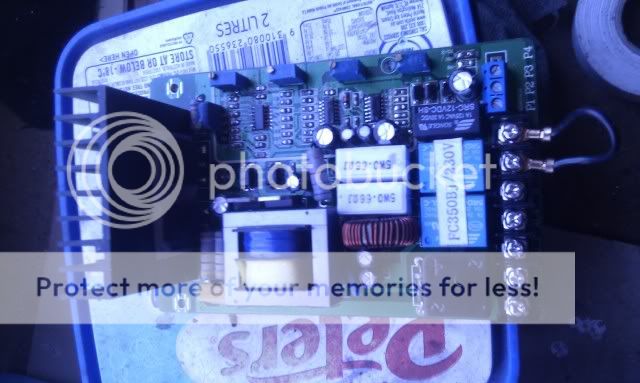
Testing with a multimeter suggested that the rectifier could well be to blame as I could get continuity (0 ohm resistance) between one AC terminal and the + terminal with the meter leads in either polarity.
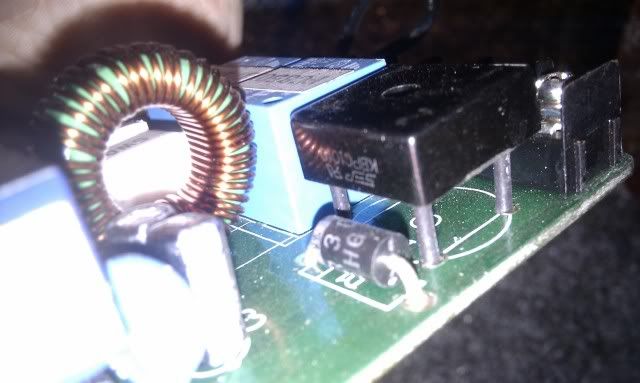
I unsoldered the rectifier to confirm the test out of the board & got the same results - so off to the electronics store the next day for a new rectifier (plus some fuses of the right rating)
The new rectifier was soldered into the board & reconnected to the mill & success :big: the mill was back to normal :big:
So there you have it - if you X2 mill stops unexpectedly & before rushing out to spend $160 for a replacement speed controller it might be worth trying to replace the rectifier first (total cost 10A rectifier + fuse $3.65).
Tony.