Metal Mickey
Well-Known Member
- Joined
- Jul 5, 2008
- Messages
- 612
- Reaction score
- 6
Well I wasn't feeling at my best so I better say that at the outset....BUT.....have you ever tried to do something you have done before only to have one problem after another? Well I have in the past but today's was a woozy!
All I wanted to do is to drill and tap a hole for a 3mm grub screw in a flywheel I have made for a couple of Christmas gifts. I started by squaring up my rotary table in the upright position and secured the flywheel in the chuck. No problems here. So all I had to do is centre the quill (and therefore centre drill/drill) over the flywheel as in the picture below:-
I thought I was being clever by covering the brass outer flywheel cover with insulation tape. I had tried using masking tape but there was a slight marking so over to the black tape. Next I wanted to find the centre of the boss in which I wanted to drill the tapping hole. My edgefinder of choice is the electronic one as seeing the red light coming on when the circuit is made. But yes, you may have guessed but I couldn't see why it wasn't working. I even replaced the batteries.........insulation tape certainly worked!
Okay then over to my other edgefinder which is a laser, but I couldn't get the laser to stay bright enough to register when it was on either edge. By now I was getting cheesed off so I thought sod it I would put the tapping drill in and do it by eye when the drill was fully lowered and alongside the boss. When I thought it was about right I zeroed the digital readouts and was about to drill when I saw the insulation tape!
So off came the tape and I used thick card to protect the flywheel from the jaws. Then the electronic edgefinder was put back and the process started again, only to find that now I couldn't lower the edge finder low enough as it was fouling the chuck!
I then had to get the parallels out to move the flywheel away from the chuck. By now an hour had passed and I stopped for a cup of tea! When I returned the edge's were found, allowing the centre position registered and would you believe it I was only 0.0012" out from the position I found with my eye!!!!!
I was now really cheesed off (I am being really polite). I lost count of the amount of times I tightened and undid the draw bar on the mill.
The rest of the session went like clockwork when it came to milling the 6 holes.
Grrrrrrrrr......... :'(
:'( :'(
happy days............................
All I wanted to do is to drill and tap a hole for a 3mm grub screw in a flywheel I have made for a couple of Christmas gifts. I started by squaring up my rotary table in the upright position and secured the flywheel in the chuck. No problems here. So all I had to do is centre the quill (and therefore centre drill/drill) over the flywheel as in the picture below:-
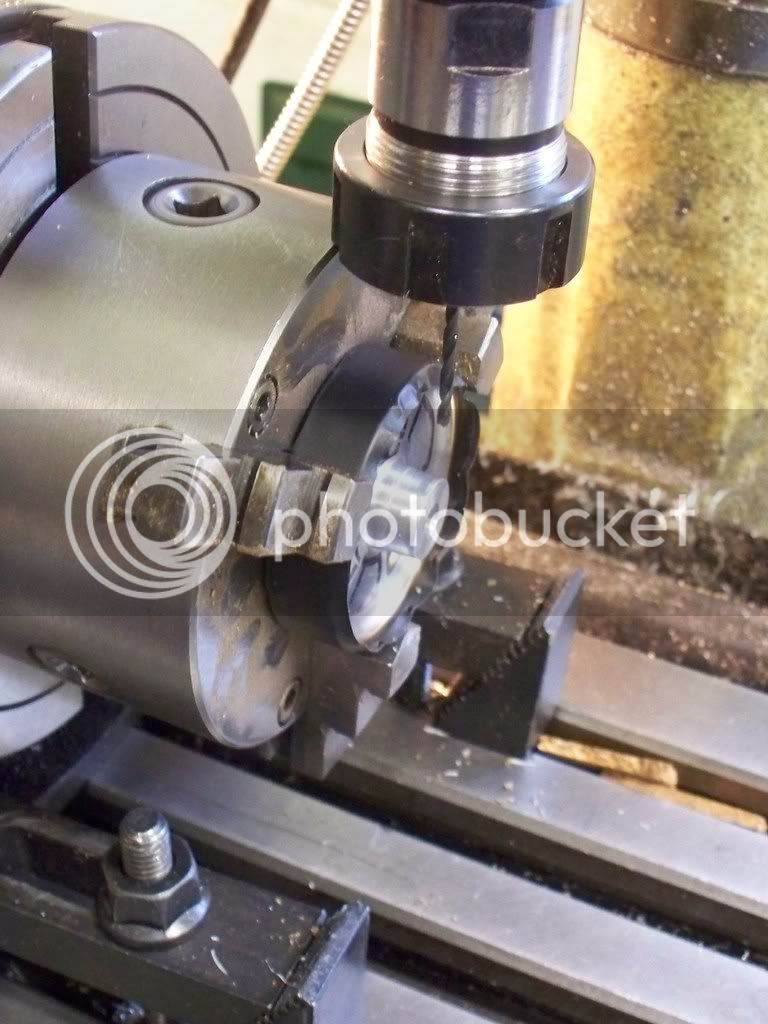
I thought I was being clever by covering the brass outer flywheel cover with insulation tape. I had tried using masking tape but there was a slight marking so over to the black tape. Next I wanted to find the centre of the boss in which I wanted to drill the tapping hole. My edgefinder of choice is the electronic one as seeing the red light coming on when the circuit is made. But yes, you may have guessed but I couldn't see why it wasn't working. I even replaced the batteries.........insulation tape certainly worked!
Okay then over to my other edgefinder which is a laser, but I couldn't get the laser to stay bright enough to register when it was on either edge. By now I was getting cheesed off so I thought sod it I would put the tapping drill in and do it by eye when the drill was fully lowered and alongside the boss. When I thought it was about right I zeroed the digital readouts and was about to drill when I saw the insulation tape!
So off came the tape and I used thick card to protect the flywheel from the jaws. Then the electronic edgefinder was put back and the process started again, only to find that now I couldn't lower the edge finder low enough as it was fouling the chuck!
I then had to get the parallels out to move the flywheel away from the chuck. By now an hour had passed and I stopped for a cup of tea! When I returned the edge's were found, allowing the centre position registered and would you believe it I was only 0.0012" out from the position I found with my eye!!!!!
I was now really cheesed off (I am being really polite). I lost count of the amount of times I tightened and undid the draw bar on the mill.
The rest of the session went like clockwork when it came to milling the 6 holes.
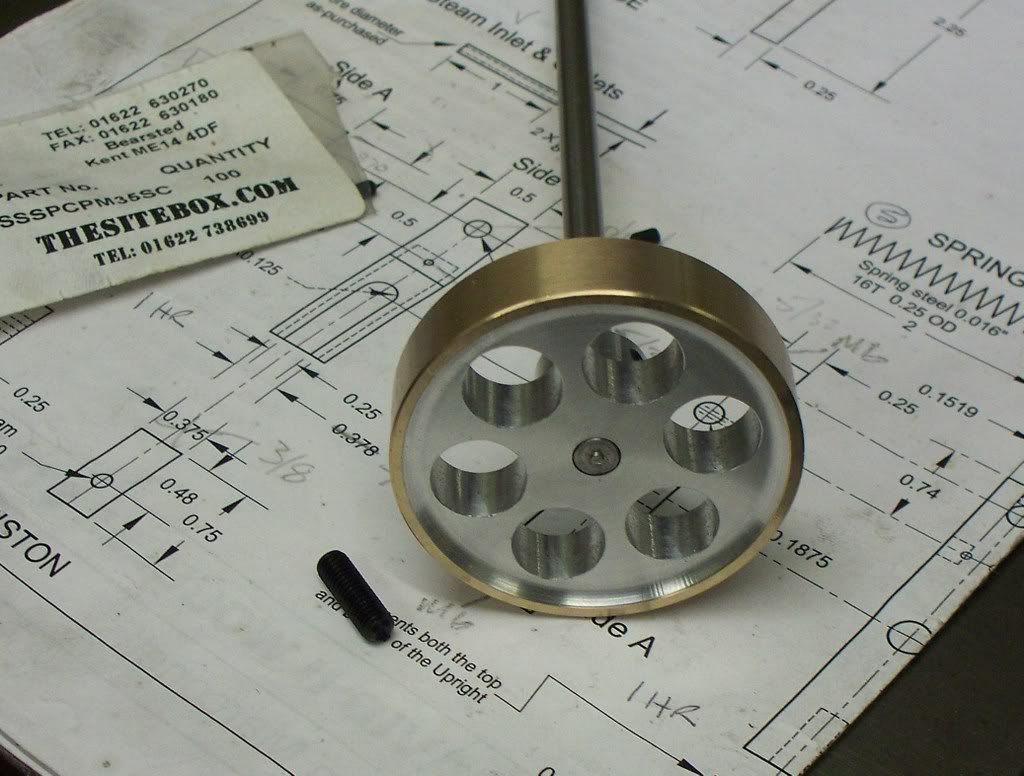
Grrrrrrrrr......... :'(
happy days............................