Things are changing and evolving as this build progresses. I have come to the conclusion that the miter gears I purchased from the hobby shop simply aren't going to have what it takes for this operation. I had to go across town this morning to Princess Auto to buy a piece of 5/8" cold rolled round stock, and while I was there I checked out their inventory of chains and sprockets. They had a pair of "weld on hub" 12 tooth sprockets for #35 pitch chain, which look to be just about perfect for the walking beam model, scale-wise. This will save me some headaches, and still guarantee that the head and tail-shafts turn at the same rpm. I will update the model this afternoon. I woke up to what is probably bad news. My lathe is DEAD!!! I checked the fuse, and checked the prox. switch which prevents the lathe from running if the gear cover on the end is removed. Nothing wrong there. I checked the electrical wall outlet, and I have power there. And there simply isn't much else I can check. I see a trip to BusyBee in Toronto in my immediate future. The trip doesn't bother me, it's less than an hour away. The problem comes in getting that big bastard of a lathe out of my shop, thru my office, into the garage and into my pickup truck. I paid some local machinery movers the outrageous sum of $400 for 30 minutes of work to put it in there from my truck when I bought it. This time it will be me and a helper that moves it.
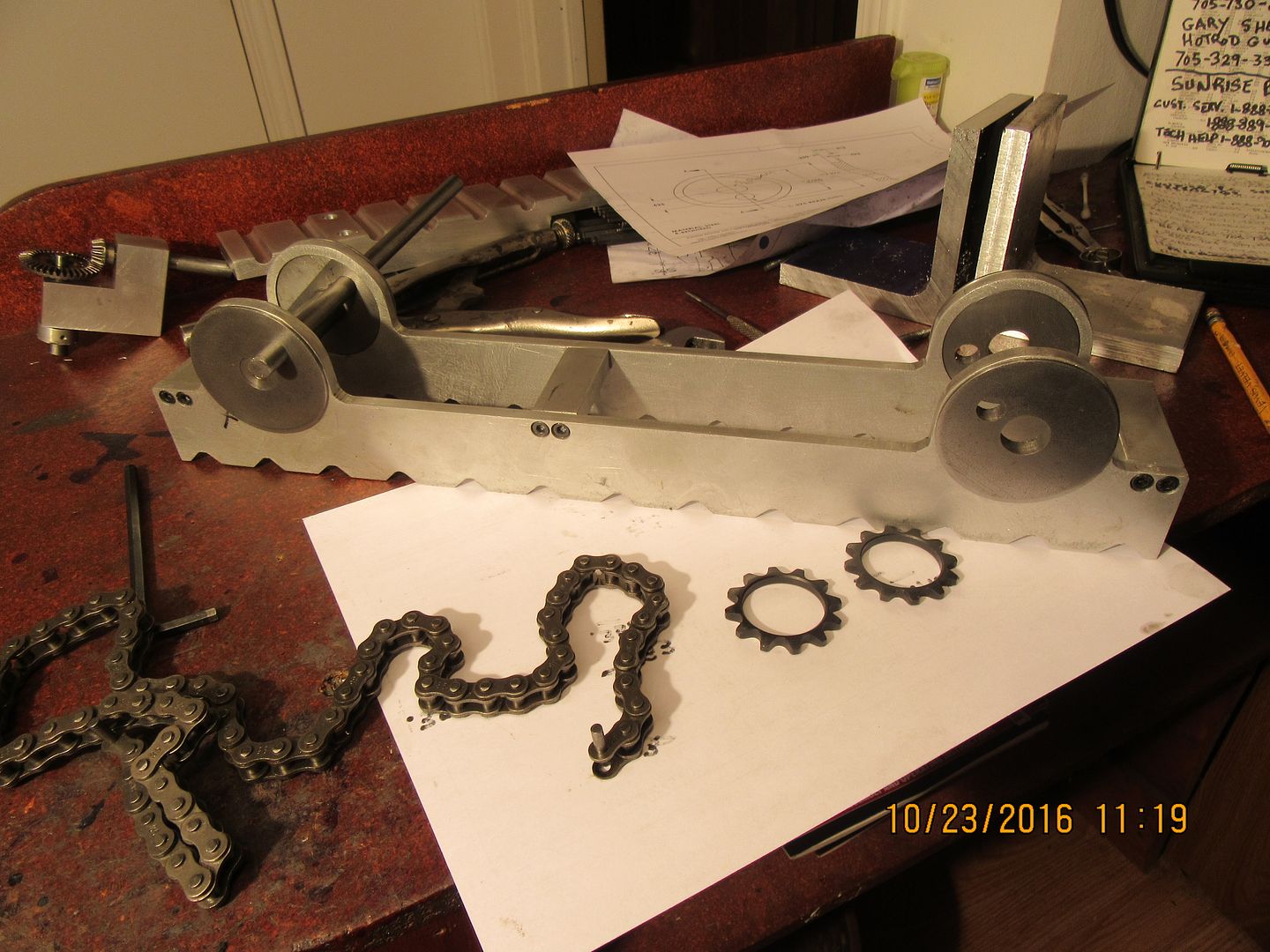