Hello All,
I looking to pick some of you tig welding pros out there. As some of you know I've been working on a prosthetic wrist and tools over the last few years. I have my quick change wrist right where I want it, but my wrenches need a little help. I've been milling a slot in an aluminium blank and inserting the tool, then using 2 set screws to hold the wrench in the holder. What I've found out in the last 2 weeks as working as a mechanic for 10hrs a day, using these wrenches exclusively, is that they loosen up after a bit and move some.
What I want to do is get a way from the aluminium blank and use a stainless steel bolt tig welded to the wrench.
Question is what kind of tig welder would I need for this? Could I get away with one that operates on 110volt?
What sort of gas would I need?
Matt
I looking to pick some of you tig welding pros out there. As some of you know I've been working on a prosthetic wrist and tools over the last few years. I have my quick change wrist right where I want it, but my wrenches need a little help. I've been milling a slot in an aluminium blank and inserting the tool, then using 2 set screws to hold the wrench in the holder. What I've found out in the last 2 weeks as working as a mechanic for 10hrs a day, using these wrenches exclusively, is that they loosen up after a bit and move some.
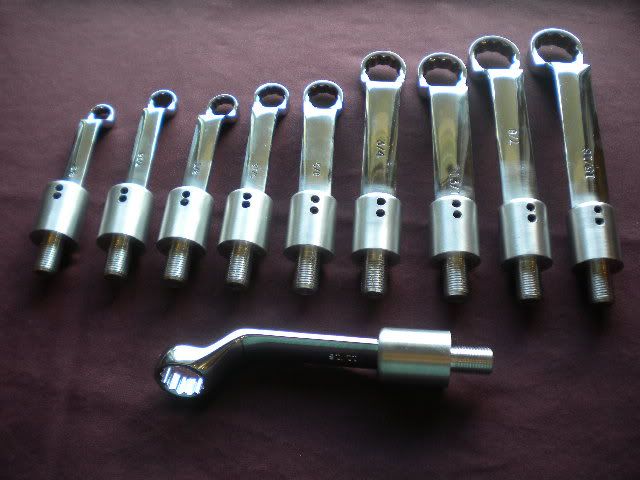
What I want to do is get a way from the aluminium blank and use a stainless steel bolt tig welded to the wrench.
Question is what kind of tig welder would I need for this? Could I get away with one that operates on 110volt?
What sort of gas would I need?
Matt