- Joined
- Aug 25, 2007
- Messages
- 3,890
- Reaction score
- 715
This small engine is designed after a horizontal mill-style steam engine. It's powered by two, hand-wound magnetic coils driving a piston assembled from 3 or 4 neodymium magnets.
https://youtu.be/oJf7N7hsLk4
The coils are attached to an Arduino micro controller with a motor shield. The valve rod on the engine pushes against a small micro-switch turning it on for half a revolution and off for the other half. The Arduino, sensing whether the switch is on or off, alternately reverses the current through the two coils.
The engine is double acting. In both directions, one coil is pushing on the magnetic piston while the other coils is pulling. Reversing the current at the end of each stroke reverses which coil is pushing and which is pulling. Here is a schematic showing the operation.
If there is sufficient interest, I'll post pictures and descriptions from the build process.
Chuck
https://youtu.be/oJf7N7hsLk4
The coils are attached to an Arduino micro controller with a motor shield. The valve rod on the engine pushes against a small micro-switch turning it on for half a revolution and off for the other half. The Arduino, sensing whether the switch is on or off, alternately reverses the current through the two coils.
The engine is double acting. In both directions, one coil is pushing on the magnetic piston while the other coils is pulling. Reversing the current at the end of each stroke reverses which coil is pushing and which is pulling. Here is a schematic showing the operation.
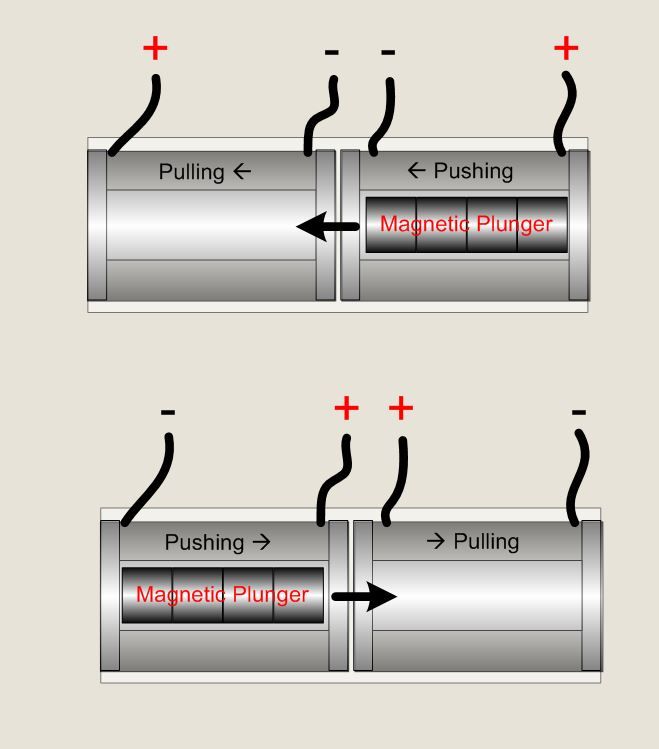
If there is sufficient interest, I'll post pictures and descriptions from the build process.
Chuck