My mill, shown in the attached pictures is a BusyBee CT129 mill, purchased in Canada 5 years ago. It has performed faithfully since I bought it (except for a burned out motor which, thankfully, burned out during the warranty period and was replaced free.) Now, although the mill itself has performed well, a couple of the highly touted "additional features" were pure garbage. The first thing to fail was the digital RPM readout, which failed almost immediately. This hasn't been a big hindrance, since I can tell by the sound of the motor and by looking at the spinning chuck or endmill whether or not it is turning at the required speed for the work I do. The second thing to fail, and it too failed far sooner than it should have, was the digital depth readout. With a bit of ingenuity and a spare 8" digital caliper, I was able to cobble up my own digital depth gauge/readout which works very well when I require it. This mill also came equipped with a swing away plexiglass chip shield, which was such a hindrance to seeing what was actually happening as I milled something that I soon removed and discarded it. NOTE:--IT IS A SAFETY DEVICE. I AM NOT RECOMMENDING THAT YOU REMOVE IT IF YOUR MILL IS SO EQUIPPED!!!
However---There is no provision on this mill for a quill stop. A quill stop is something which you can live without. BUT---If you want to make repetitive plunge cuts as I often do, there is no way to do this without paying very close attention to the digital quill readout---if it works!!! Today I am suffering from terminal boredom, so I have been looking at my mill to see if there is a way to resolve this lack of depth stop issue. there IS!! Hang in there with me, and we will take a look at how i propose to do this to my mill.
However---There is no provision on this mill for a quill stop. A quill stop is something which you can live without. BUT---If you want to make repetitive plunge cuts as I often do, there is no way to do this without paying very close attention to the digital quill readout---if it works!!! Today I am suffering from terminal boredom, so I have been looking at my mill to see if there is a way to resolve this lack of depth stop issue. there IS!! Hang in there with me, and we will take a look at how i propose to do this to my mill.
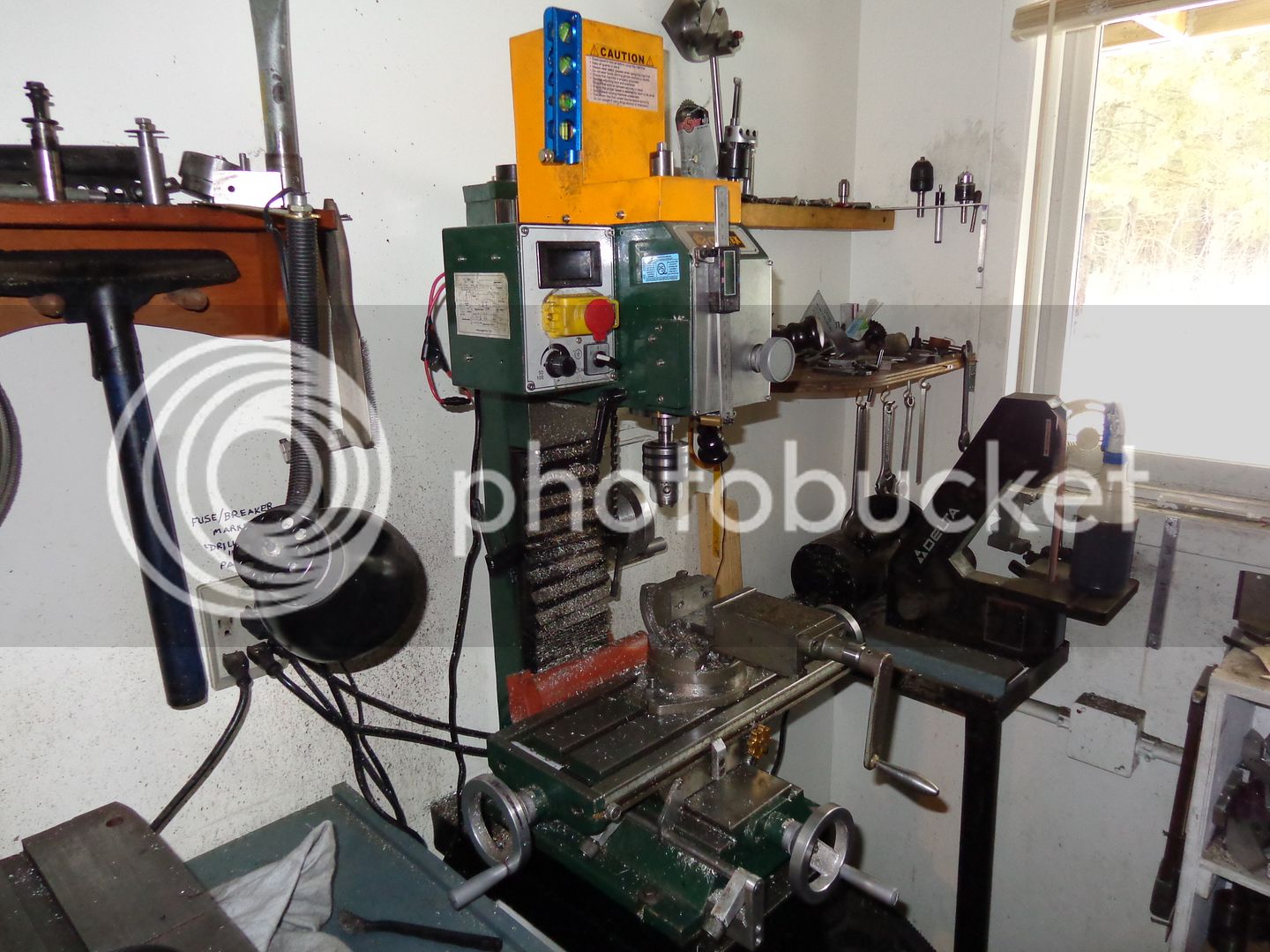
Last edited: