d-m
Well-Known Member
- Joined
- Mar 20, 2008
- Messages
- 211
- Reaction score
- 5
Hi all
In what little time I have had between side work and my CNC conversion I have had a small project going on the side.Having wanted to do a build post but not having the time to show and write the post I took some pic's today hoping that will give you and ideal of how I thought this finger biter up. I was at a yard sale during the early spring and came across a50 to 1 Boston right angle gear reducer the price was right I took it home. It sat under the bench till about 5 weeks ago, I should add that I own a power hack saw the problem is it is stored at a friends house in Fla. and last time I was there we were unable to find it in the piles of junk (what a waste of a shop) so I have written it off. OK back to the build, I was looking at the gear reducer and the output shaft and started thinking that if I could use the face of the box for the blade arm that would help keep it square and make a good mount area and that is were the fun began. I had an old face plate that won't fit anything I own, I machined a plug from alum and threaded it to fit the 1.500 hole. then squaring it all up in my 4 jaw I and bored it .800. to clear the the .750 shaft then faced the hole thing down so the plate was .250 and machined the other side of the plug to press fit a bearing.Then drilled the hole pattern to match the gear reducer.
The next trick was to start on the saw arm taking a left over of 1.500 X 4.00 bar I started boring a hole for the bearing to fit in.I did this on the mill with a boring head I missed the mark for a press fit and had to drill and tap for grub screws
Then I drilled and taped for 3 5/16 cap screws and cut a nice 18" piece of flat bar 5/8X 1.250 and repeated the hole pattern. Then with a key cutter I made a T slot 15" long
In what little time I have had between side work and my CNC conversion I have had a small project going on the side.Having wanted to do a build post but not having the time to show and write the post I took some pic's today hoping that will give you and ideal of how I thought this finger biter up. I was at a yard sale during the early spring and came across a50 to 1 Boston right angle gear reducer the price was right I took it home. It sat under the bench till about 5 weeks ago, I should add that I own a power hack saw the problem is it is stored at a friends house in Fla. and last time I was there we were unable to find it in the piles of junk (what a waste of a shop) so I have written it off. OK back to the build, I was looking at the gear reducer and the output shaft and started thinking that if I could use the face of the box for the blade arm that would help keep it square and make a good mount area and that is were the fun began. I had an old face plate that won't fit anything I own, I machined a plug from alum and threaded it to fit the 1.500 hole. then squaring it all up in my 4 jaw I and bored it .800. to clear the the .750 shaft then faced the hole thing down so the plate was .250 and machined the other side of the plug to press fit a bearing.Then drilled the hole pattern to match the gear reducer.
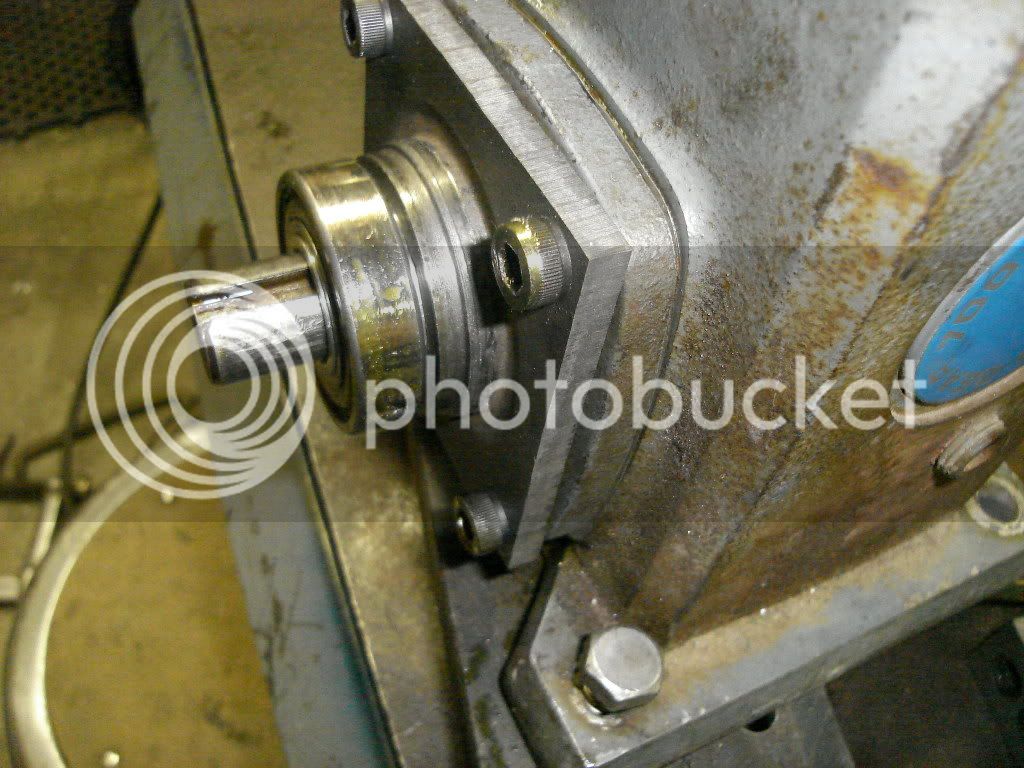
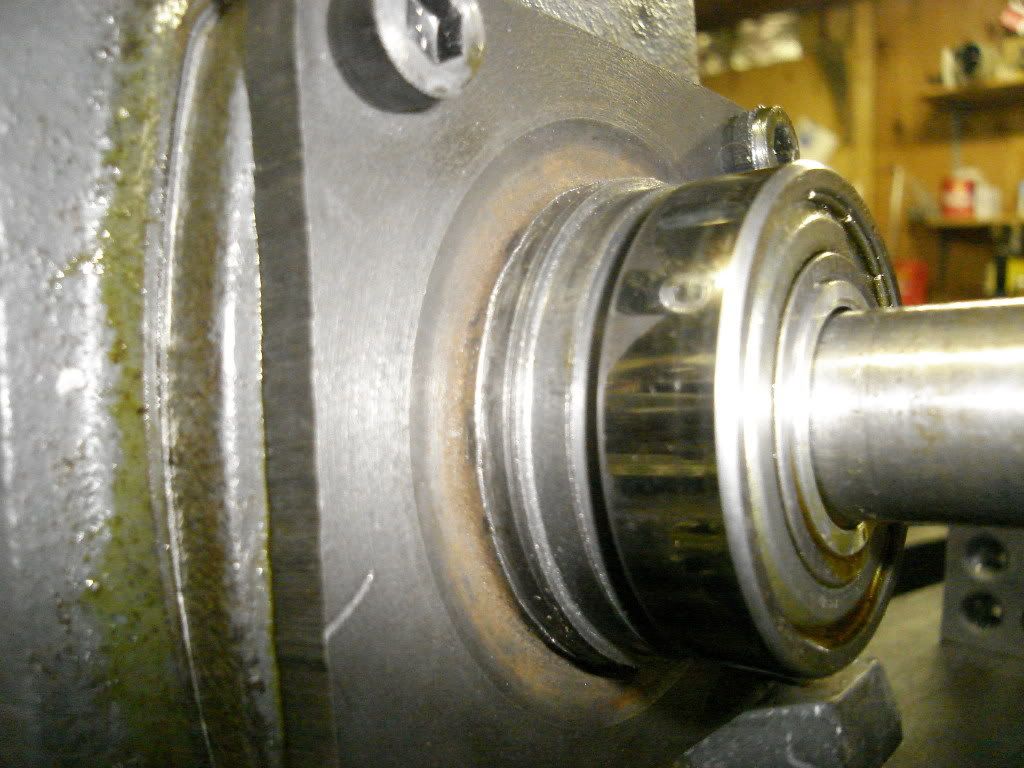
The next trick was to start on the saw arm taking a left over of 1.500 X 4.00 bar I started boring a hole for the bearing to fit in.I did this on the mill with a boring head I missed the mark for a press fit and had to drill and tap for grub screws
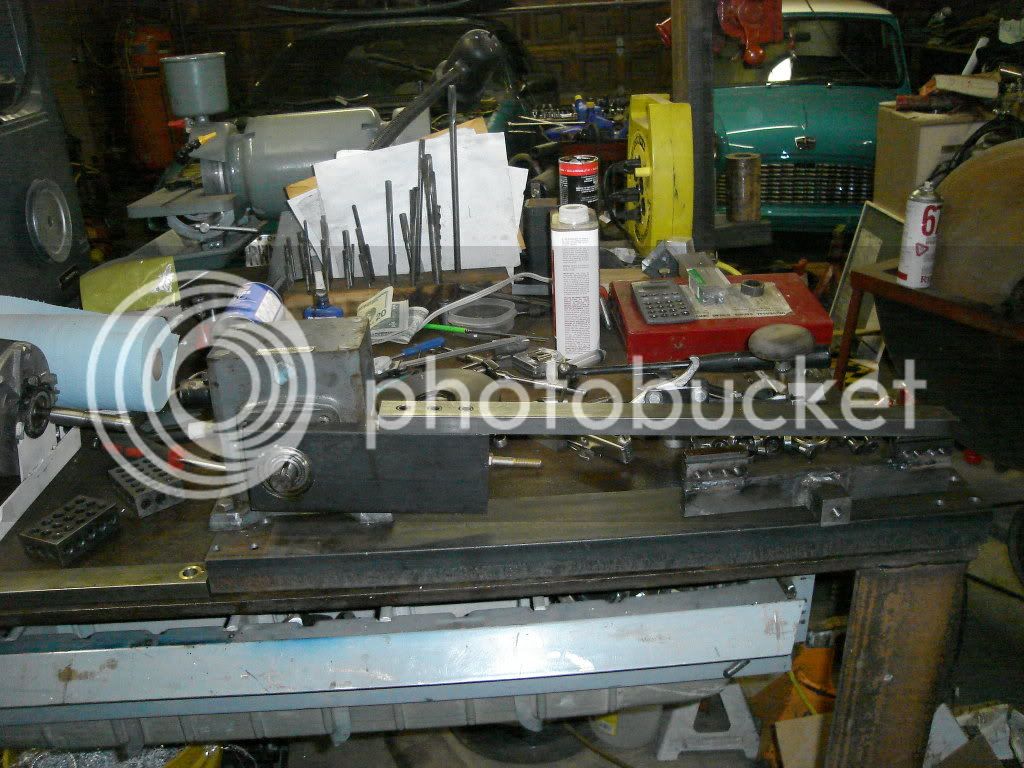
Then I drilled and taped for 3 5/16 cap screws and cut a nice 18" piece of flat bar 5/8X 1.250 and repeated the hole pattern. Then with a key cutter I made a T slot 15" long
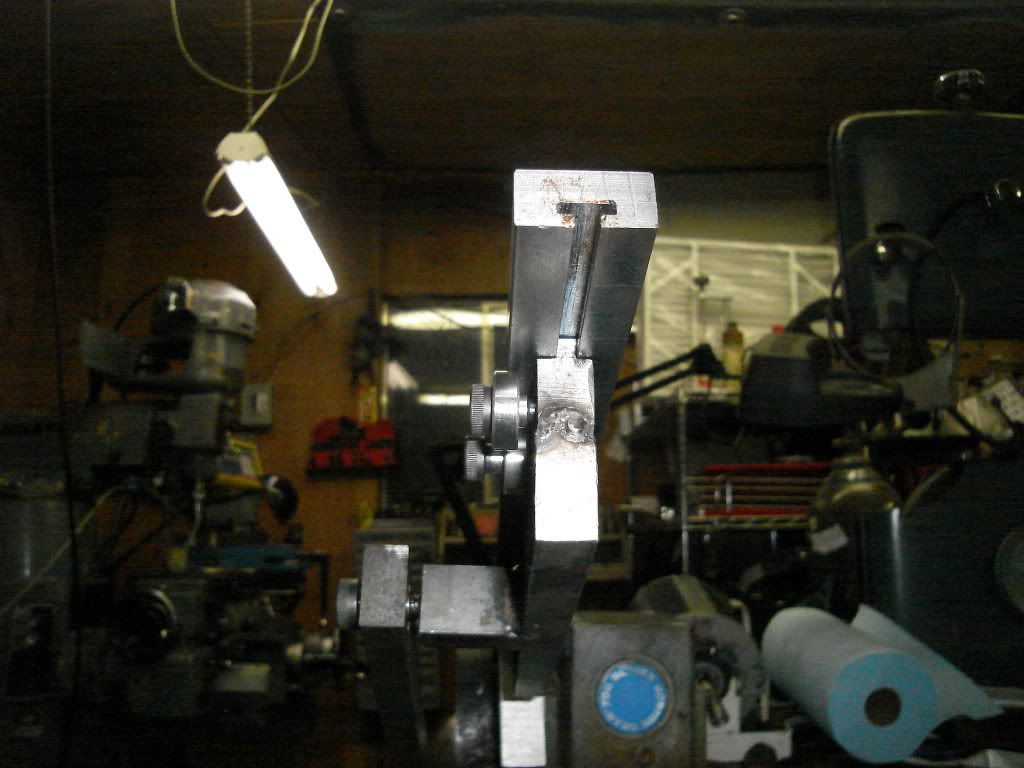