Of course, once I get everything removed that I don't need, it becomes obvious why I got it for $5!!!!! Somebody has turned on their wipers with the wiper blades frozen down to the windshield and stripped a spot on the nylon worm gear. Damn!!! However, the worm still engages enough to turn the worm gear---just barely. I have to machine a housing to accomodate both gears, and when I do I will run enough of an interferance that the steel worm will cut a little deeper into the nylon. There won't be nearly as much load as would have been imposed by the electric motor, so it will probably be okay for what I want it to do. Ya just can't trust them greasy buggers at the wreckers--Although in all honesty, I don't think they knew either. That wiper motor has probably been setting around inside the wreckers shop longer than the kids been around who sold it to me.
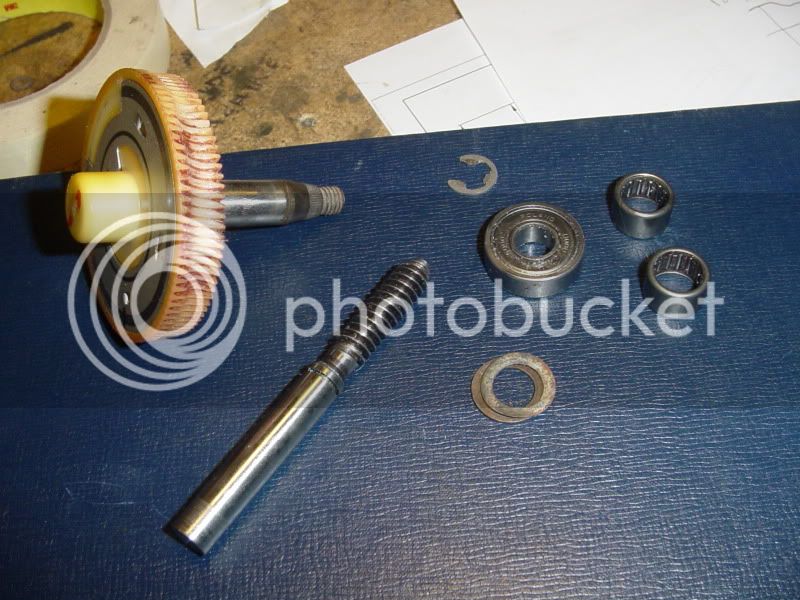
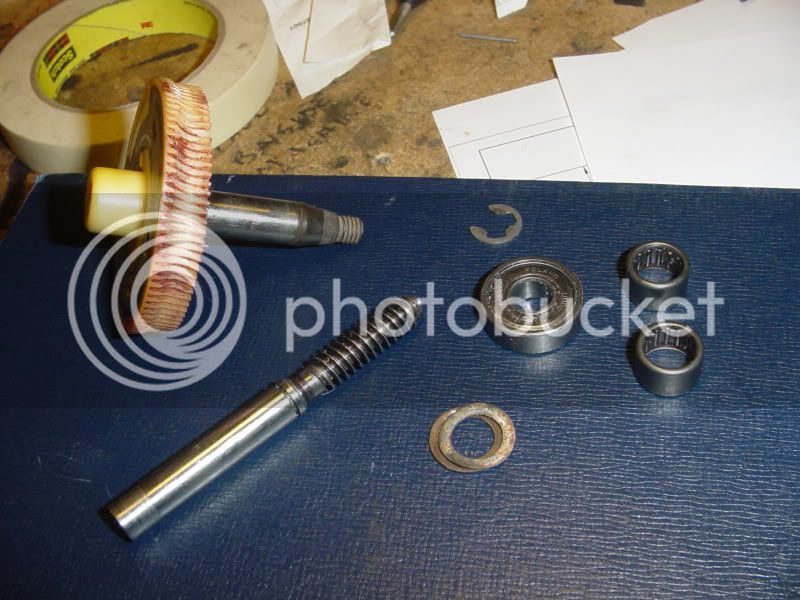