Had the lathe motor refusing to re-start after being stopped during a cut, to say nothing about the smokes and smells.
A bit later, I could have it turning again, though intermittently. Unusual buzzing sounds coming from somewhere into the HS
Sounds like that 50mm dia. steel rod (a un-machined remnant from sequential gearbox arbor blank of a well known Italian sport cars brand) was a bit too tough for the little thingy.
Decided to dismount it and have a closer look at the inside.
As usual with pulleys, this one wont come out easily: no point into trying to hammer it free (dont ask why I know that) better for me to use a suitable extractor.
Of course, none of the ones I previously made could fit the task, though I could re-use part of the bike clutch extractor by machining an aluminium base from a portion of a once-too-long homemade lathe TS.
Definitely weak, with that (already present) large hole in that position, but it got the job done.
And a picture of the partially dismounted HS.
When I finally managed to open the motor, everything inside of it was covered with a thick layer of black dust from the carbons, but the wires look- OK. The carbons themselves are still long enough to reach their contacts, but the springs are no more acting accordingly to their names. . Maybe I found where the problem was?
I still dunno: wanna clean it thoroughly before reapplying any power. I suppose soaking into alcohol and brushing should do, providing I let it dry before causing any spark in its proximity.
The rotor, the old carbons and a new one (from an identical never used before motor).
Top motor casing, showing a couple of partially melted carbon holders: I suppose I can avoid hunting for replacements, providing I will find no shorts. Of course, should I happen to stumble upon a couple of suitable ones I would not let the occasion escape.
In the meanwhile, I will do with that spare motor. While I am at it, I have ideas about a few (mostly cosmetic) machine modifications, while I have it dismounted.
a) A couple of risers for the entire machine: somewhere between 1 and 2 inches, to ease cleaning the chip tray (to say nothing about reducing the frequency of the task). That might involve reducing the height of the table it is sitting on. Will see..
b) Some hinges for the gear cover to pivot on.
c) A new splash screen (easier to remove than the current one) with a separate chip protection for the motor.
d) A new, smaller, motor pulley to reduce the lowest speed and increase the torque.
Marcello
A bit later, I could have it turning again, though intermittently. Unusual buzzing sounds coming from somewhere into the HS
Sounds like that 50mm dia. steel rod (a un-machined remnant from sequential gearbox arbor blank of a well known Italian sport cars brand) was a bit too tough for the little thingy.
Decided to dismount it and have a closer look at the inside.
As usual with pulleys, this one wont come out easily: no point into trying to hammer it free (dont ask why I know that) better for me to use a suitable extractor.
Of course, none of the ones I previously made could fit the task, though I could re-use part of the bike clutch extractor by machining an aluminium base from a portion of a once-too-long homemade lathe TS.
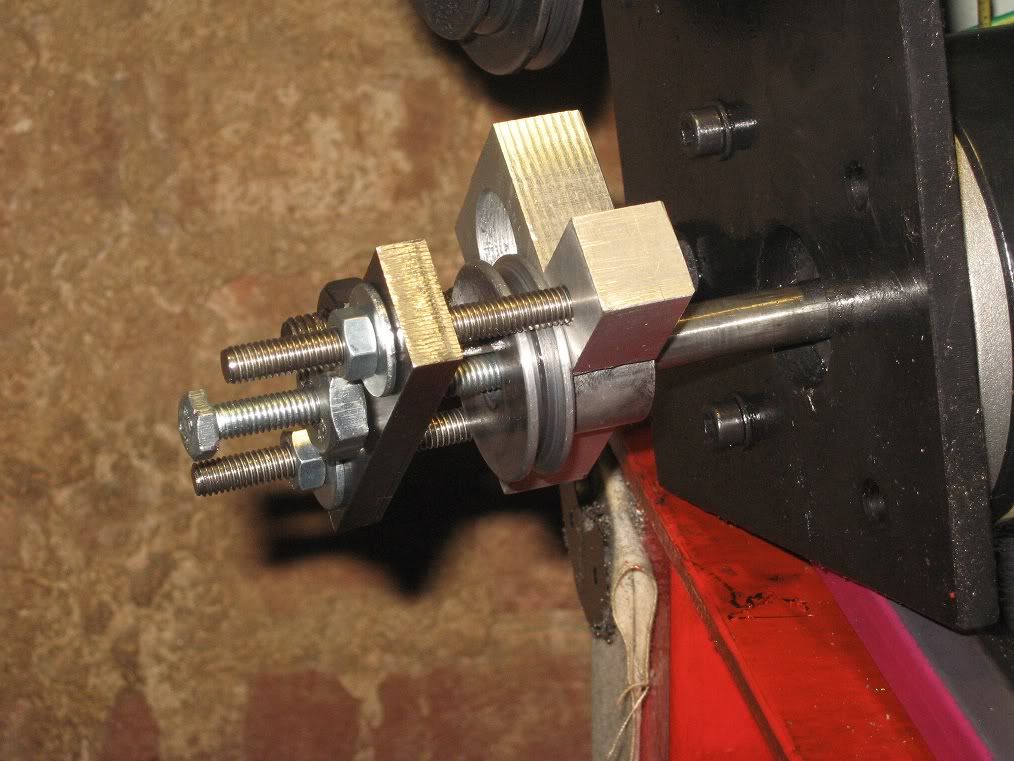
Definitely weak, with that (already present) large hole in that position, but it got the job done.
And a picture of the partially dismounted HS.

When I finally managed to open the motor, everything inside of it was covered with a thick layer of black dust from the carbons, but the wires look- OK. The carbons themselves are still long enough to reach their contacts, but the springs are no more acting accordingly to their names. . Maybe I found where the problem was?
I still dunno: wanna clean it thoroughly before reapplying any power. I suppose soaking into alcohol and brushing should do, providing I let it dry before causing any spark in its proximity.
The rotor, the old carbons and a new one (from an identical never used before motor).
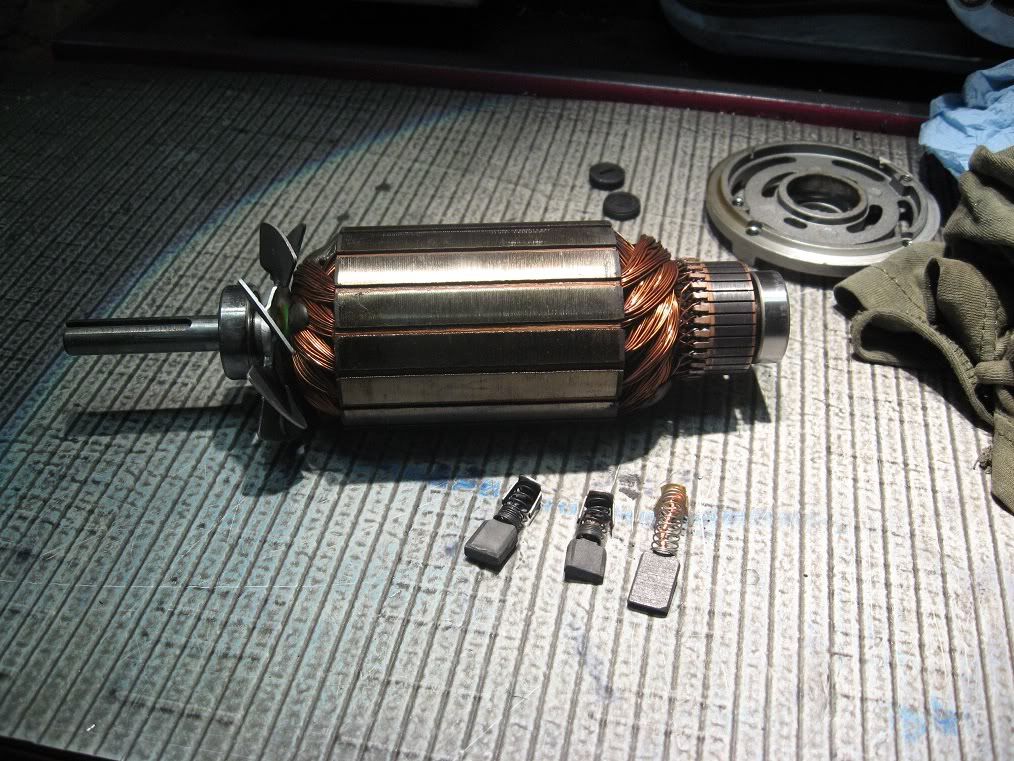
Top motor casing, showing a couple of partially melted carbon holders: I suppose I can avoid hunting for replacements, providing I will find no shorts. Of course, should I happen to stumble upon a couple of suitable ones I would not let the occasion escape.
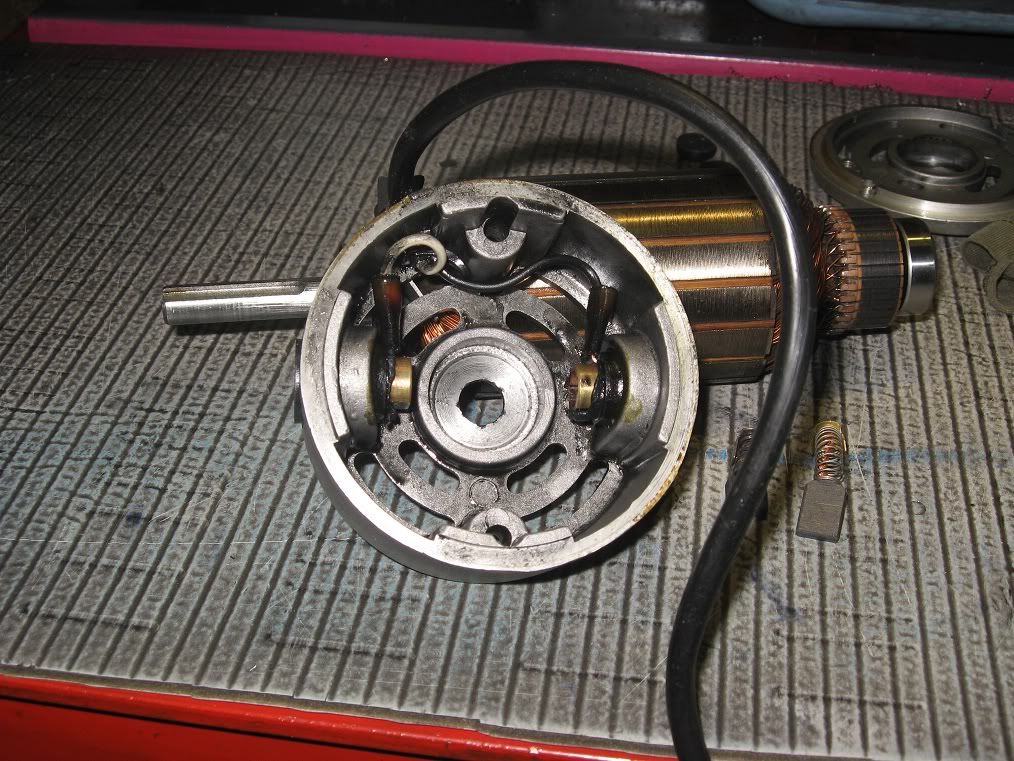
In the meanwhile, I will do with that spare motor. While I am at it, I have ideas about a few (mostly cosmetic) machine modifications, while I have it dismounted.
a) A couple of risers for the entire machine: somewhere between 1 and 2 inches, to ease cleaning the chip tray (to say nothing about reducing the frequency of the task). That might involve reducing the height of the table it is sitting on. Will see..
b) Some hinges for the gear cover to pivot on.
c) A new splash screen (easier to remove than the current one) with a separate chip protection for the motor.
d) A new, smaller, motor pulley to reduce the lowest speed and increase the torque.
Marcello