Little_Freddie
Member
- Joined
- Dec 18, 2009
- Messages
- 16
- Reaction score
- 0
Hiya again,
not been on much since my intro,.... I thought my time would be better spent 'tweaking' the lathe, and practicing marking, cutting, drilling, tapping, etc...Getting my eye in, so to speak
I also dare not come on without a picture, (Congratulations, Zeep, BTW! :bow: nice engine!!) so have also been playing (poorly!) with a digital camera, I am a lot happier with my Cannon T90,... but cant find the USB port on it.....
So, attached (hopefully!) are a couple of piccys of my first engine build, and first play on a lathe!!
I used stainless steel, (50mm x 6mm) for the base/chassis, mainly because I am going to have to learn how to drill/cut/tap it, and because I had a 10 foot length of it handy!! The valve body and cylinder body are cut from a piece of 2" x 3/4" Ali bar.
I marked, drilled and tapped the base without blunting too many drills, didn't snap a single tap!, then set about the valve and cylinder body. I cut them, marked them out, but had a lot of trouble trying to get a parallel hole through them with the pillar drill, ( ??? ???) the holes seemed to drift all over the place, so having read up online, decided to take the feared step of removing the 3 jaw chuck, and fitting the (still in its box!) 4 jaw independant on my chinese 7 x 14.
Fellow Newbies, dont fear it, do it!!! :big: :big: After centre drilling, away I went, drilled out the valve body to 5.5mm, then reamed to 6mm. Cylinder next, drilled out to 12 mm, then reamed out to 1/2", (Imperial, metric, bring 'em on!!! Things were going so well, I fear no man!!!! ;D)
As you can see, the bits so far seem to be somewhere near,... Soon, on to turning some brass bits!!
Cheers Guys, Fred
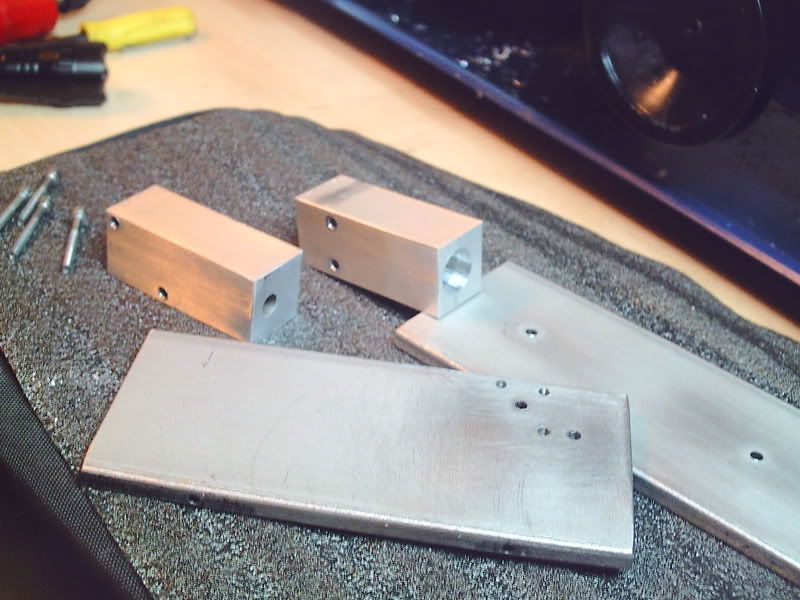
