student_Machinist
Feist92
- Joined
- Jan 19, 2008
- Messages
- 86
- Reaction score
- 4
This isn't really related to model engineering but i could do with some help with how to make something that closely resembles this:
Its a linear slide for a rapid prototyping printer that im thinking of making so tolerances need to be very tight. I need two for each axis, around 140mm long to suit a 12mm shaft.
I cant for the life of me work out how to mill the angles (mounting is proving to be a problem) so any advice would be appreciated
Regards
Jonathan
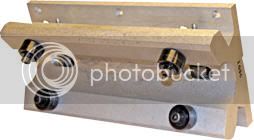
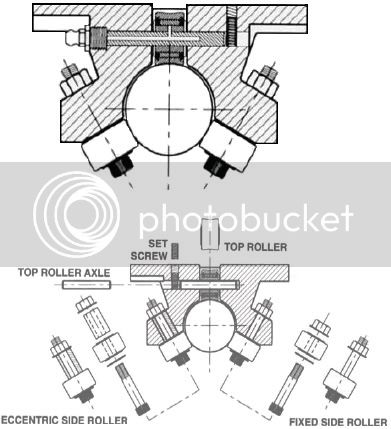
Its a linear slide for a rapid prototyping printer that im thinking of making so tolerances need to be very tight. I need two for each axis, around 140mm long to suit a 12mm shaft.
I cant for the life of me work out how to mill the angles (mounting is proving to be a problem) so any advice would be appreciated
Regards
Jonathan