I have a project where I need to mill a bowl into a plate of aluminum. I needs to have a diameter of 3". I have a mill and a boring head and I was thinking of grinding a tool with an arc of 3". Any ideas on how I could do this better?
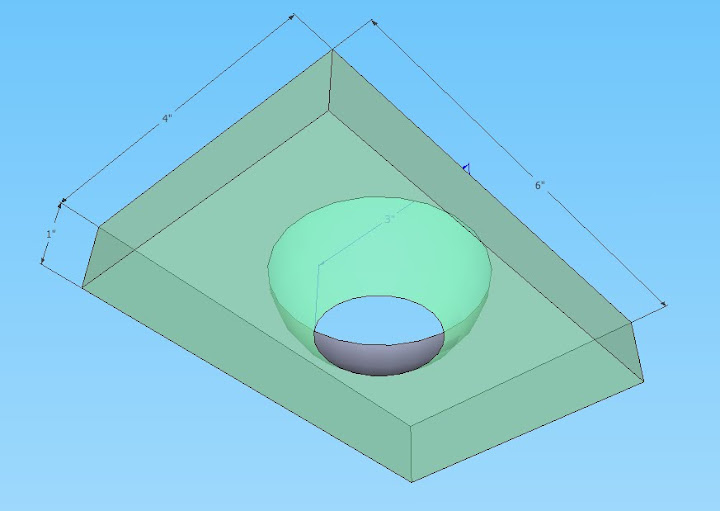
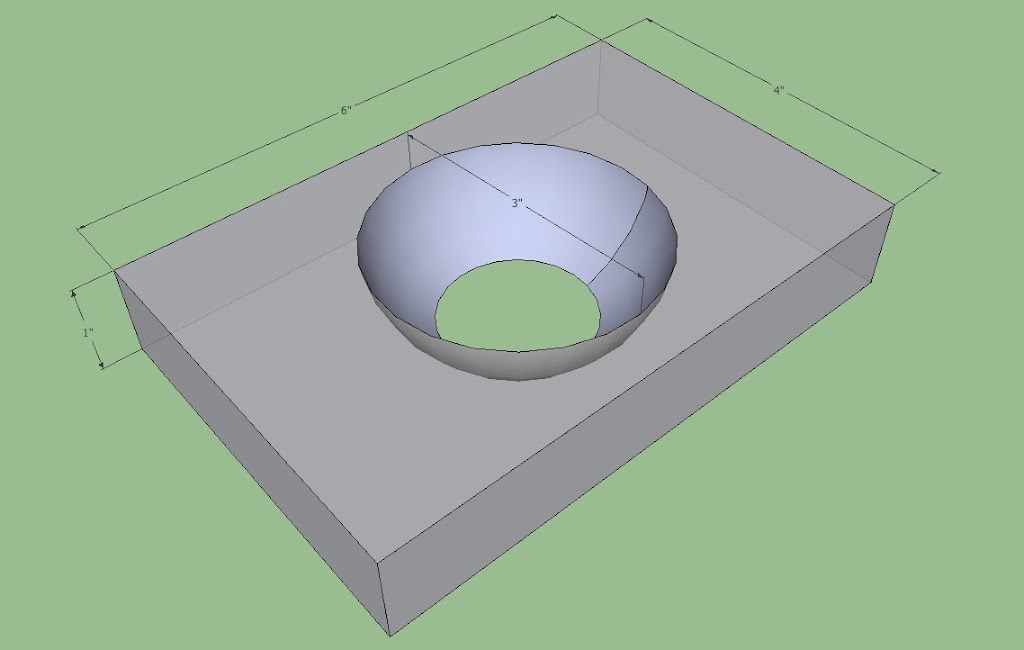
Fixed.Flipping the drawing over helps as well
Enter your email address to join: