I discovered (some time ago) a simple way to make plastic gears.
DSCN0196 by aardvark_akubra, on Flickr
A plastic blank is mounted on the lathe spindle and a steel gear of the required gear 'family' is mounted on a spindle on the tool post. The size of the steel gear is not important.
The method is really simple, the lathe is started and the plastic blank brought into contact with the steel gear which begins to turn. Applying a little pressure causes a rumbling noise but after a minute or two that subsides. Apparently the friction of the steel gear running over the blank has heated the plastic which becomes softer. More pressure is applied and again held until the rumbling subsides. This sequence is repeated until teeth are formed of the required depth.
That's it, except for trimming the edges of the plastic gear.
A few notes, the number of teeth is determined by the diameter of the plastic blank which equates quite closely to the PCD. Any size steel gear will create a plastic gear with the correct tooth form regardless of the number of teeth on the steel gear or the diameter of the blank. It is important to withdraw the steel gear from contact before stopping the spindle, otherwise the plastic gear will be deformed where it cools against the gear. Not all plastics are suitable but it is not hard to experiment.
cogs by aardvark_akubra, on Flickr
John
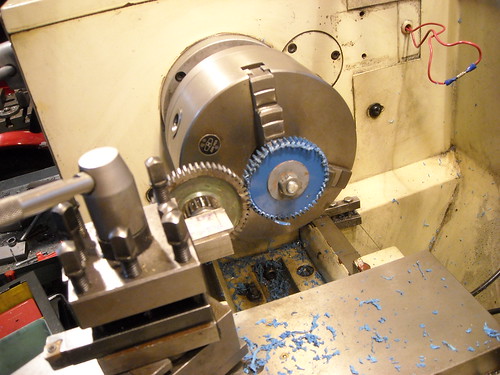
DSCN0196 by aardvark_akubra, on Flickr
A plastic blank is mounted on the lathe spindle and a steel gear of the required gear 'family' is mounted on a spindle on the tool post. The size of the steel gear is not important.
The method is really simple, the lathe is started and the plastic blank brought into contact with the steel gear which begins to turn. Applying a little pressure causes a rumbling noise but after a minute or two that subsides. Apparently the friction of the steel gear running over the blank has heated the plastic which becomes softer. More pressure is applied and again held until the rumbling subsides. This sequence is repeated until teeth are formed of the required depth.
That's it, except for trimming the edges of the plastic gear.
A few notes, the number of teeth is determined by the diameter of the plastic blank which equates quite closely to the PCD. Any size steel gear will create a plastic gear with the correct tooth form regardless of the number of teeth on the steel gear or the diameter of the blank. It is important to withdraw the steel gear from contact before stopping the spindle, otherwise the plastic gear will be deformed where it cools against the gear. Not all plastics are suitable but it is not hard to experiment.
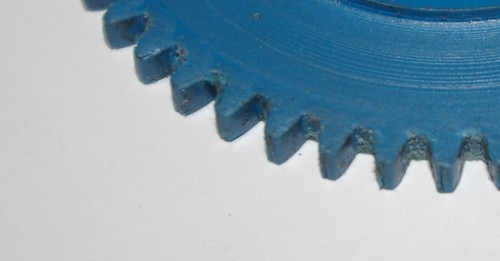
cogs by aardvark_akubra, on Flickr
John
Last edited: