- Joined
- Jul 16, 2007
- Messages
- 2,985
- Reaction score
- 1,052
This time we'll do the camshaft. Although this is for the Holt the machining techniques I use can be applied to any camshaft. Eveyone who has made a camshaft has their construction preferences. The earliest way that I read about was the separate lob and shaft type. The shaft is just a piece of steel of choice. The lobes are made from a hardenable steel, O-1, W-1. This piece of stock is drilled and reamed for whatever shaft diameter you are using. The profile is then machined onto it long enough to get the required number of lobes plus cutoff widths. The lobes are then located onto the shaft both lengthwise and radially relative to the timing of that particular valve. This involves some type of fixture to hold the shaft, a degree wheel for indexing and a dial indicator to find the peak lift of the lobe. After locating the lobes are cross drilled through the lobe and shaft for a pin. The lobe is then removed, hardened, replaced, pinned and then the pin is dressed off. It sounds somewhat complicated but at the time home hobbyists were building these they were mainly made for singles and twins. The next way to make a cam is to build a cam grinding fixture. Over the years several variations have been presented in different publications but their function was the same, make a master lobe of the shape required and through a rocking follower grind that shape onto your shaft. The shaft still requires accurate indexing to get the timing of each lobe correct. This is a nice way to go if you first want to build the fixture and second you are planning on making quite a few cams in your career. The next version is the one presented by Steve Huck and others. This involves a lathe fixture with a degree wheel. The shaft is mounted in a fixture on the lathe. It is set off center so that it is turned eccentrically and by rotating the shaft relative to a pre calculated set of degrees the lobe is formed. This procedure will only produce a 'soft' cam. The only way to get a hardened camshaft is to rough out the cam, harden it and grind the profiles or as in the first presentation. I have found for most engines that I have built by just making the cam out of drill rod and leaving it unhardened works fine. I do harden my lifters/tappets so that the wear between the two is kept to a minimum. Now I'll present my way. I'm sure there are others that do it this way but I'll call it my way. I start out with a layout of the lobe shape. In the case of the Holt camshaft the pofile layout is somewhat lacking in information so I took what I thought the author wanted and developed my own profile. I lay out radial lines with tangencies to the pofile that give me 'cusps' of about .0007. You can make them smaller but that involves more steps and more chances of making a mistake. I have found that .0007 is easy to file smooth. When I get these radians layed out I measure how far it is from the center of the shaft out to the flat. I do this for each radian and make a chart of these readings. One number is the angle in degrees the other is the step height.
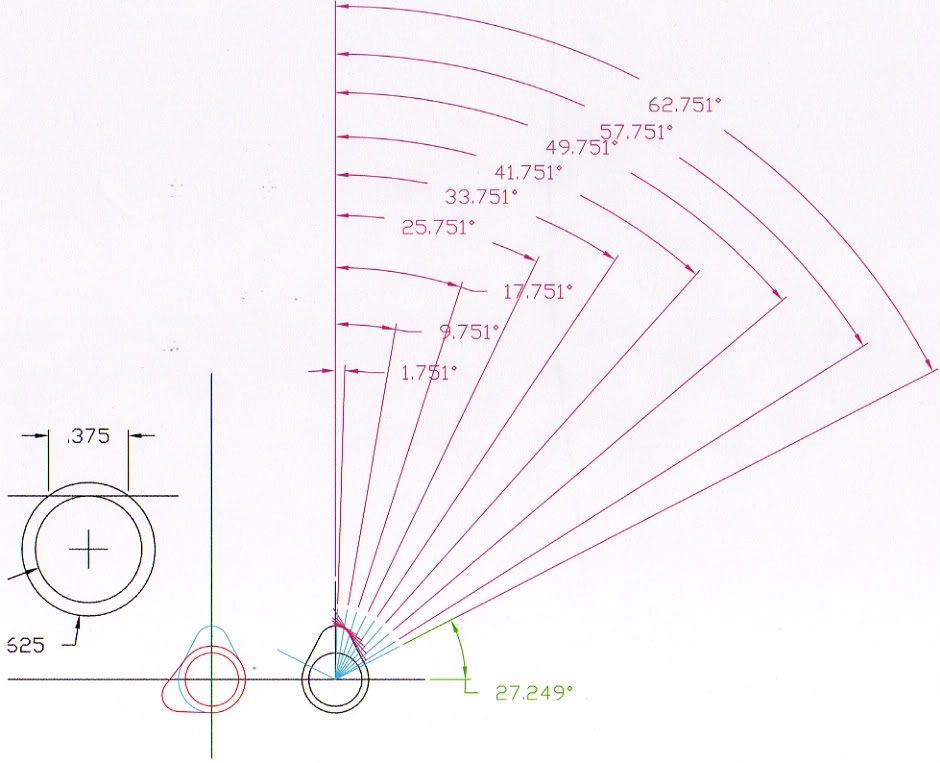
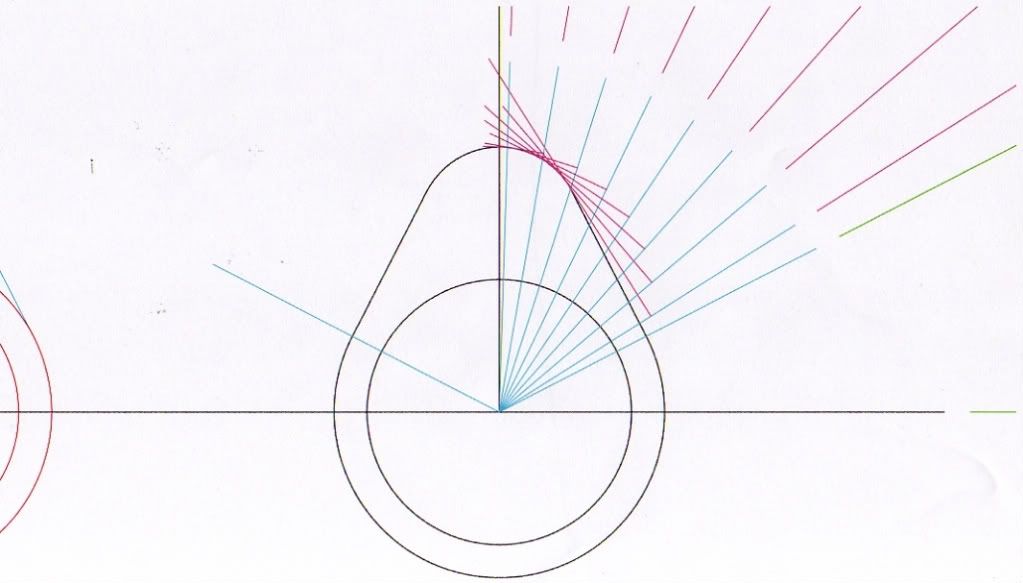
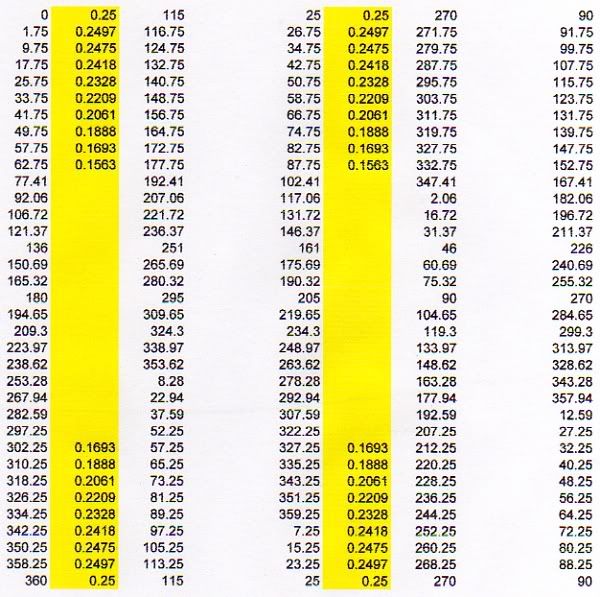
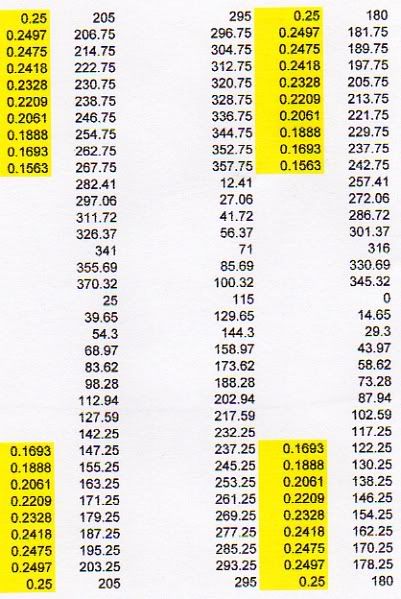