vascon2196
Well-Known Member
- Joined
- Oct 2, 2009
- Messages
- 1,026
- Reaction score
- 312
Howdy folks!
Sooooooo....I just purchased a steady rest for my mini-lathe and decided to give it a try. I have used full size steady rests before without any issues.
I fixed the left end of the tubing in the 3-jaw chuck and supported the left end of the tubing with the steady rest. All I planned on doing was facing each end of the tubing to length.
Well once I started facing the tubing started to creep towards the right towards the tool! So I tightened up on the 3-jaw a little more and tried it again...and it kept on creeping towards the right. I even ran the damn thing in reverse and it kept creeping to the right!!! It also appeared to slip on the jaws and it made a mess as you can see in the pictures. Am I missing something? Please tell me I am missing something stupid.:wall:
:wall:
:wall::rant:
Sooooooo....I just purchased a steady rest for my mini-lathe and decided to give it a try. I have used full size steady rests before without any issues.
I fixed the left end of the tubing in the 3-jaw chuck and supported the left end of the tubing with the steady rest. All I planned on doing was facing each end of the tubing to length.
Well once I started facing the tubing started to creep towards the right towards the tool! So I tightened up on the 3-jaw a little more and tried it again...and it kept on creeping towards the right. I even ran the damn thing in reverse and it kept creeping to the right!!! It also appeared to slip on the jaws and it made a mess as you can see in the pictures. Am I missing something? Please tell me I am missing something stupid.:wall:
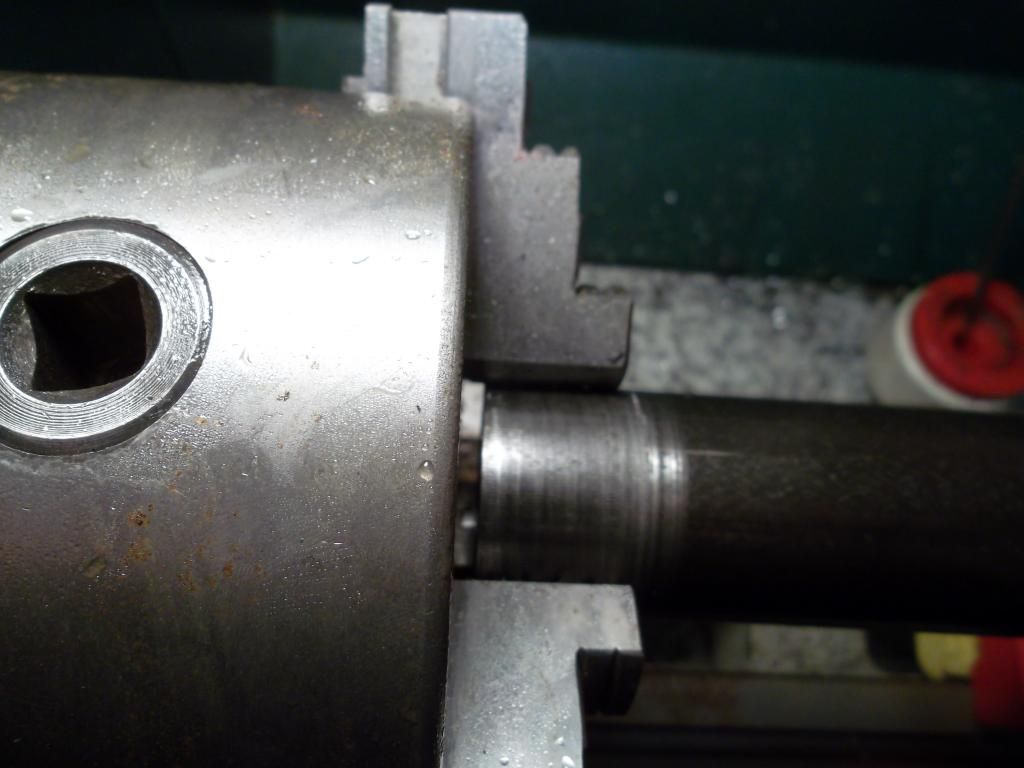
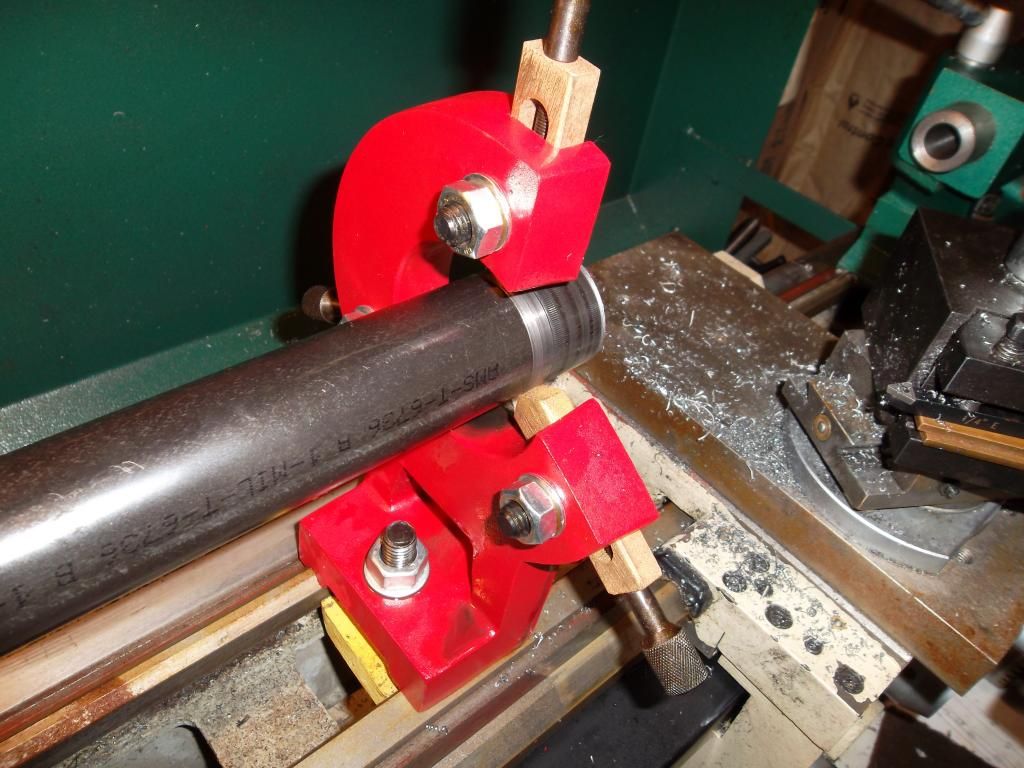
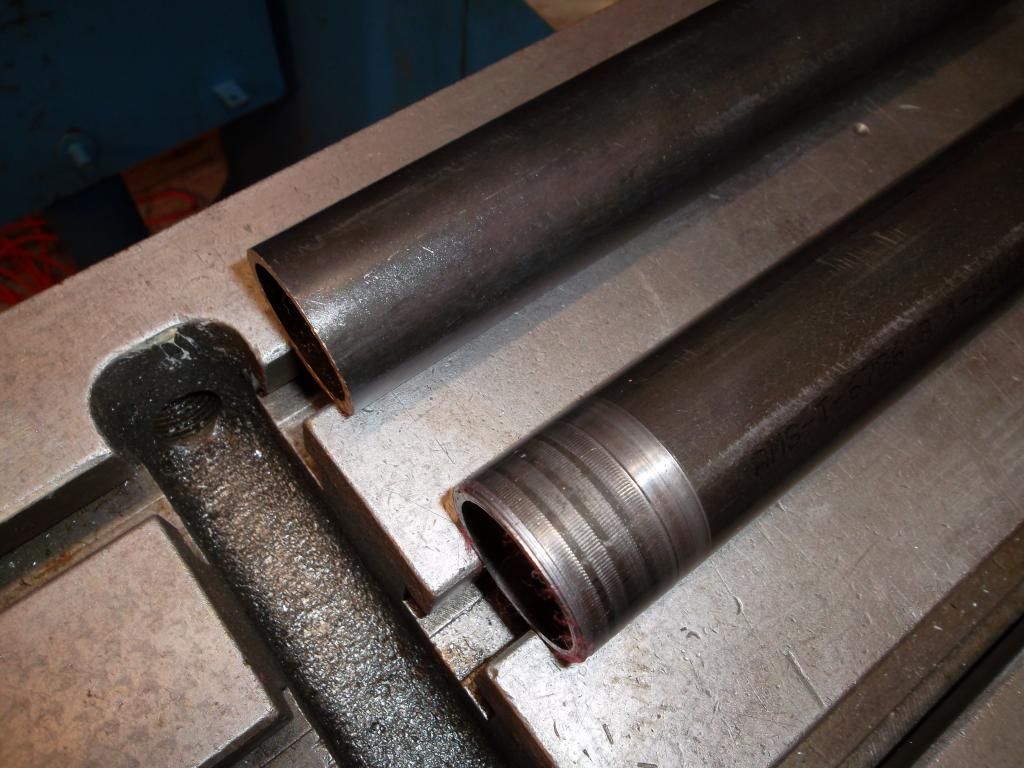