Now we are going to get into a subject in which I claim no expertise at all. Although I am a fair framing carpenter, having built a couple of houses and cottages over a lifetime, fine cabinetry is not my forte' in any way. However, I want the Rupnow engine to be portable for display purposes. It will have an upper and lower compartment and be made so that the engine is mounted and displayed in the "upper compartment" when the top of the box is removed, while the battery pack and CDI unit will be hidden underneath in the "lower compartment". The material for the box will be clear pine with some kind of mahogany stain on it and a few coats of Varathane for water and oil-proofing. I haven't totally sussed out the latch mechanisms yet, but they will probably be 4 threaded rods with knurled brass knobs that pass thru clearance holes in the removable top section of the box and screw into threaded inserts into the bottom section of the box. The removable top section will have a carry handle on the top of it. Since these engines have a tendency to get dirtier than Paddy's Pig after being ran for an hour, I would like to be able to spray it down with Varsol and then blow it off with compressed air while it is still bolted to the bottom of the display box in order to clean it. Of course this means that any seams in the bottom of the display box will have to be sealed so that varsol doesn't leach thru into the area where the battery pack and the cdi reside.---And yet I still have to be able to access the battery pack and cdi. to recharge the batteries. Its plain that there will be a few challenges along the way. I am not going to use biscuit joints or anything fancy, as I have neither the equipment nor the know how to do this. All joints will be square or mitered at 45 degrees and glued with Elmers wood glue. You are welcome to follow along and watch me bumble my way through this.---Brian
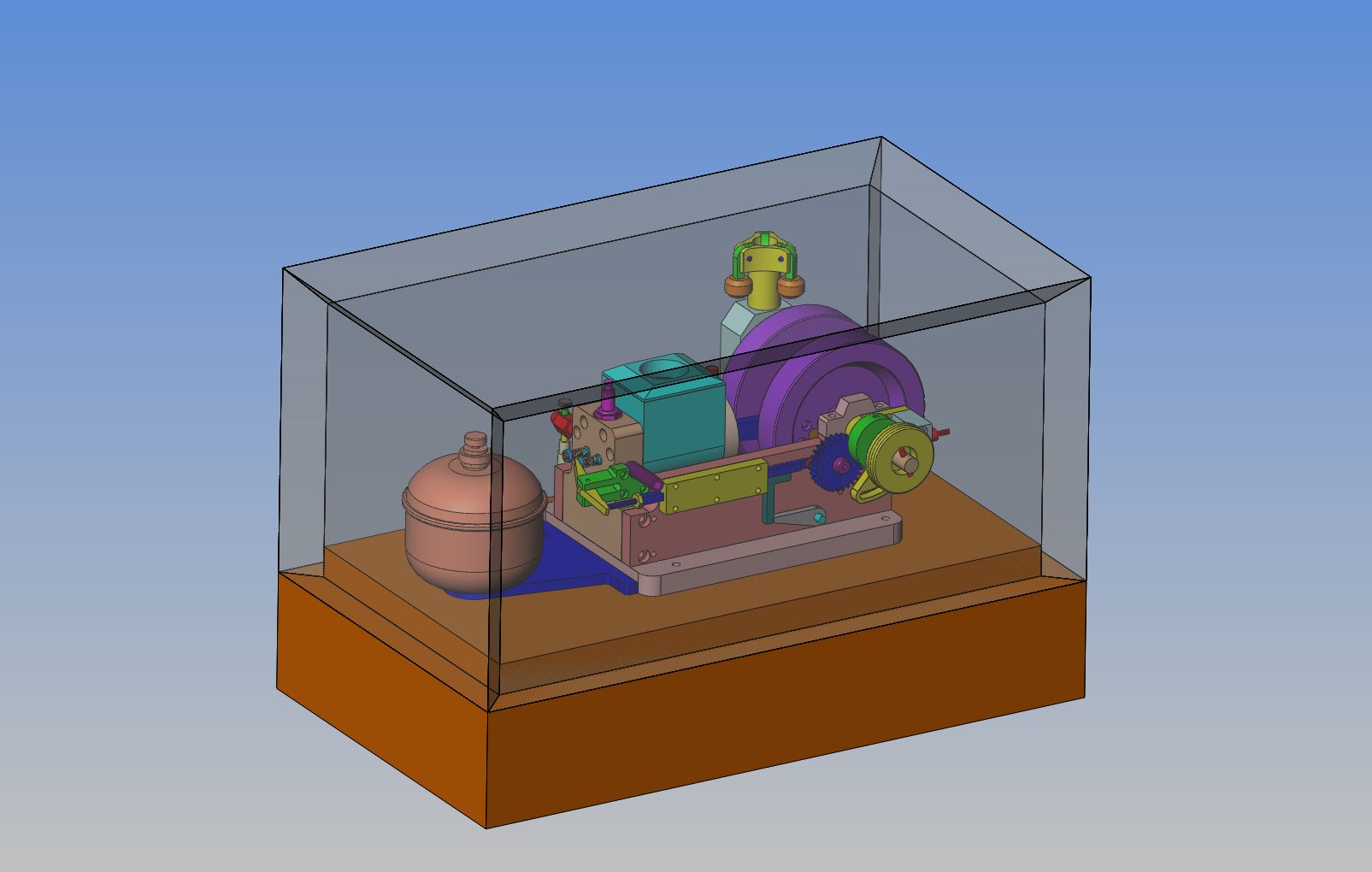
Last edited: