JMI
Well-Known Member
Thought I'd make a engine that allowed a minimum amount of operator interaction and after following Zee's saga Elmer's 43 seemed a natural. Plus it let's me try out my newly purchased el-Cheapo Enco 5c collets and collet block set. So far - so good...
Crosshead build:
7/16ths? Close enough:
Drill and ream:
Remove, cut, mount in collet block and indicate:
Finish cylinder head end:
Some more drilling and milling:
Good to go...
Will start on the cylinder next.
Jim
Crosshead build:
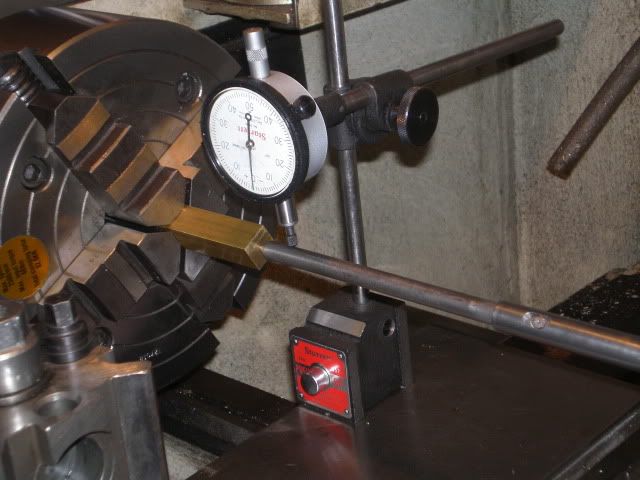
7/16ths? Close enough:
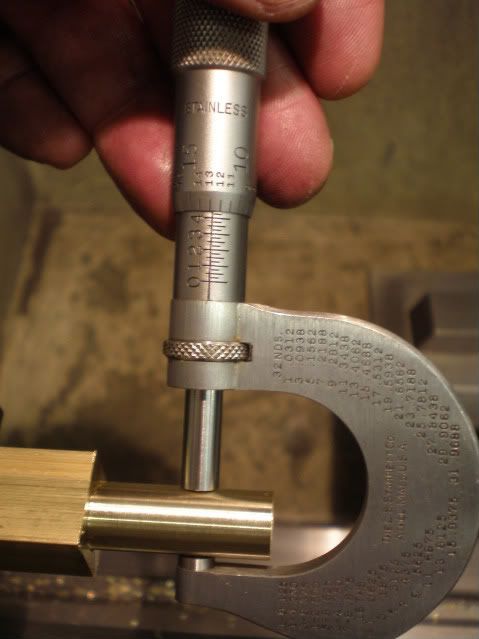
Drill and ream:
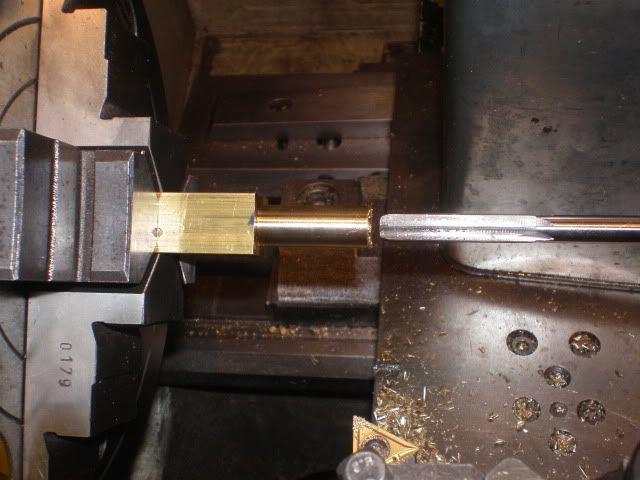
Remove, cut, mount in collet block and indicate:
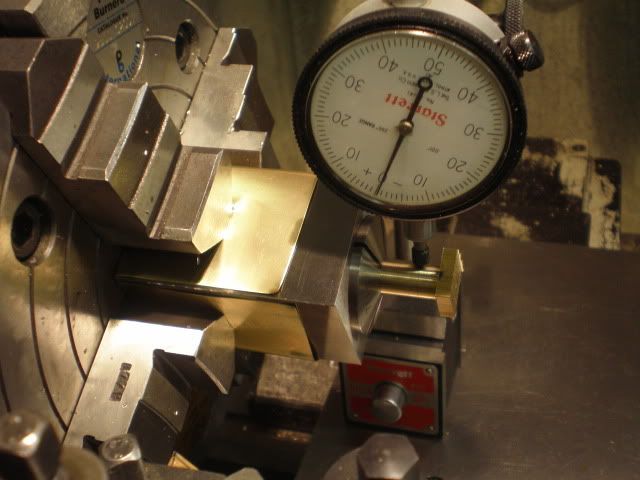
Finish cylinder head end:

Some more drilling and milling:

Good to go...
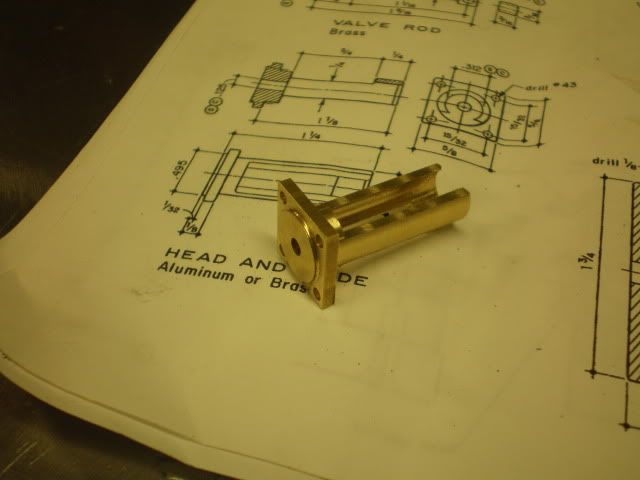
Will start on the cylinder next.
Jim