kevincoxshall
Member
- Joined
- Feb 20, 2010
- Messages
- 21
- Reaction score
- 0
Hi all,
I have just purchased an ER25 collet chuck and backplate for my lathe. The chuck has 3 tapped holes and the backplate has 4 clear holes. I can't easily drill more holes in the back plate so are there any suggestions how to fix the 2 items together?
I have thought about an intermediate plate between the 2 items.
Are there any other ideas............
[/url][/img]
[/url]
[/img]
I have just purchased an ER25 collet chuck and backplate for my lathe. The chuck has 3 tapped holes and the backplate has 4 clear holes. I can't easily drill more holes in the back plate so are there any suggestions how to fix the 2 items together?
I have thought about an intermediate plate between the 2 items.
Are there any other ideas............
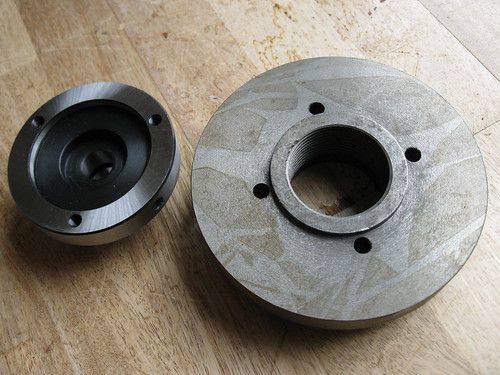
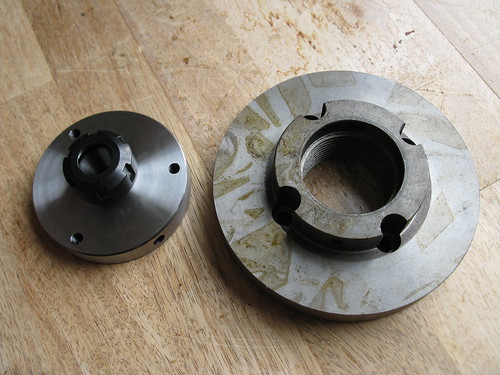
[/img]