And another one bites the dust!!! I just finished the clutch activator block and bolted it onto the bearing stand to make sure all the bolts line up-----They did!!! As you can see from the grease around the clutch sliders, I have been "fiddling" with the clutch mechanism and now have it working much smoother. I did put a small compression spring inside the winch shaft which bears against the cross pin to ensure that the clutch disengages each time it has been engaged and it works much better now.
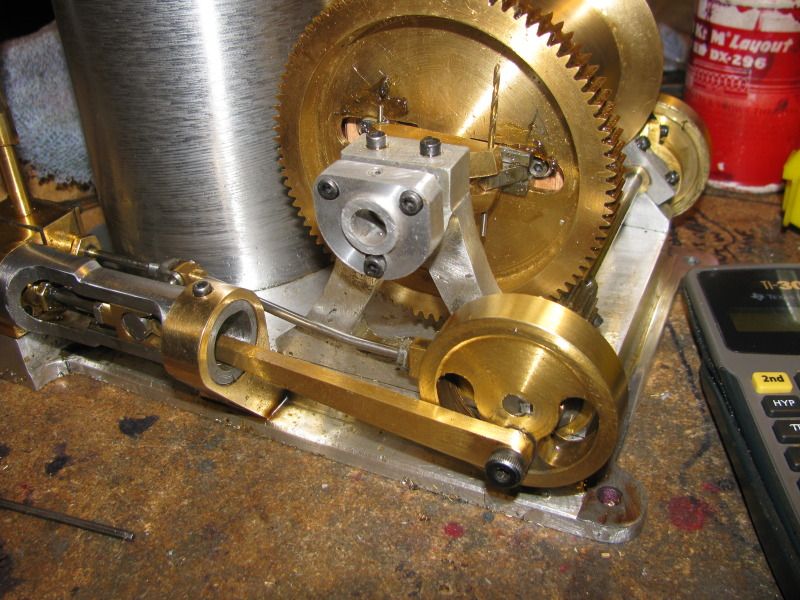