so here is attempt #2.
attempt #1 resulted in a epic fail. but I learned and todays attempt went much smoother.
woke up early stopped off at mr.metal. no small 18guage offcuts to give me so they handed me a large piece for free (enough to start patching the jeep after my practice)
with a nice flat sheet I took out the sawzall (wish I had something better) and cut out a test piece, got out the welder and found its sweet spot.
I know everyone is saying low wire speed and low voltage, but I went with what my welding book suggested (3-4 volts) as bench mark and worked from that.
here are some pictures.
shielding gas was used, compressor to cool down the welds with a blast of air, grinder with grinder wheel, 40 and 80 grit flappers to work it smooth.
I would always start my welds on the big piece of metal and move it to the smaller piece being attached. should I try just following the cut?
attempt #1 resulted in a epic fail. but I learned and todays attempt went much smoother.
woke up early stopped off at mr.metal. no small 18guage offcuts to give me so they handed me a large piece for free (enough to start patching the jeep after my practice)
with a nice flat sheet I took out the sawzall (wish I had something better) and cut out a test piece, got out the welder and found its sweet spot.
I know everyone is saying low wire speed and low voltage, but I went with what my welding book suggested (3-4 volts) as bench mark and worked from that.
here are some pictures.
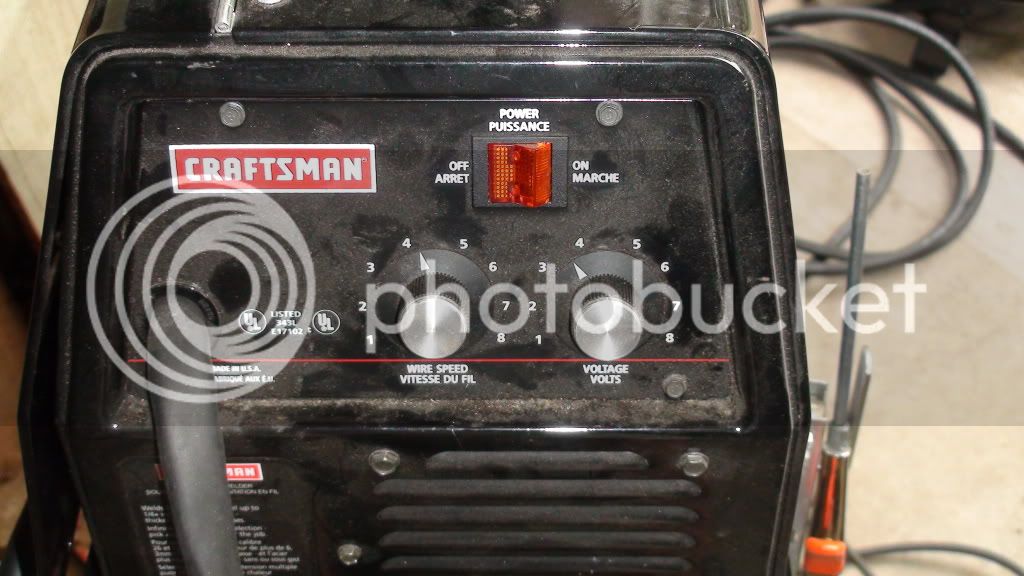
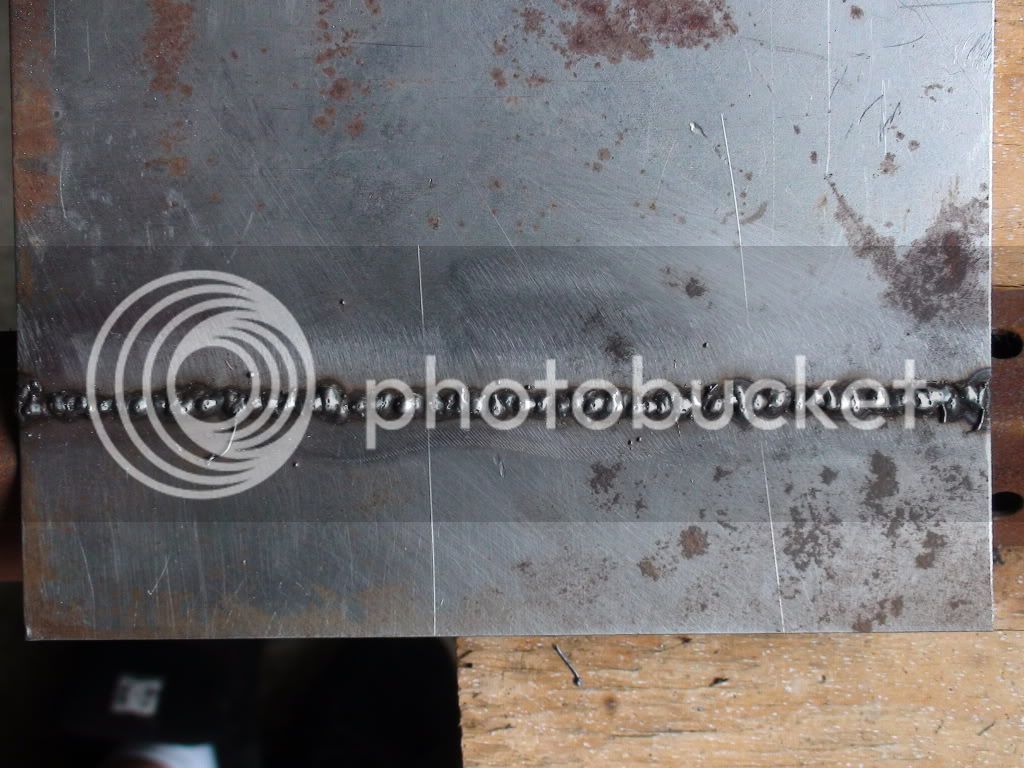
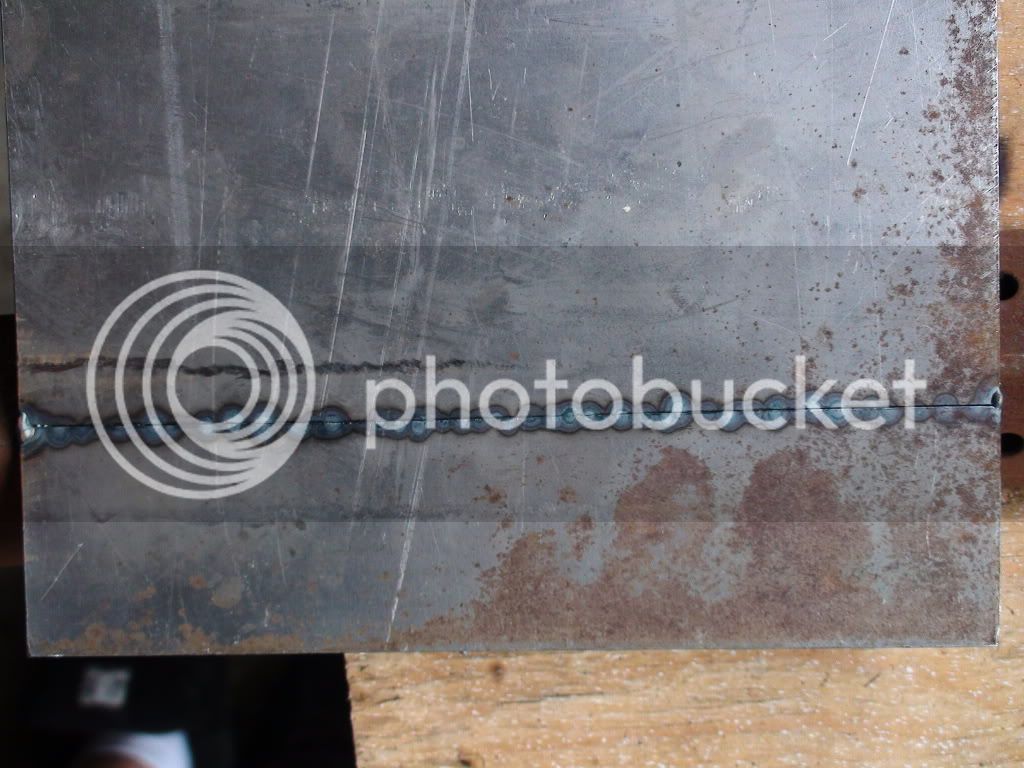
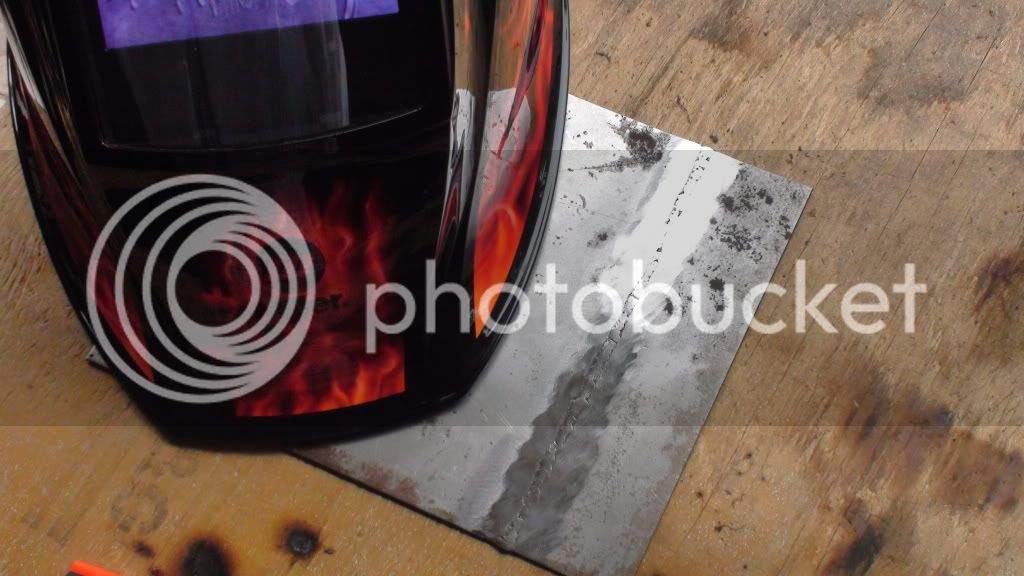
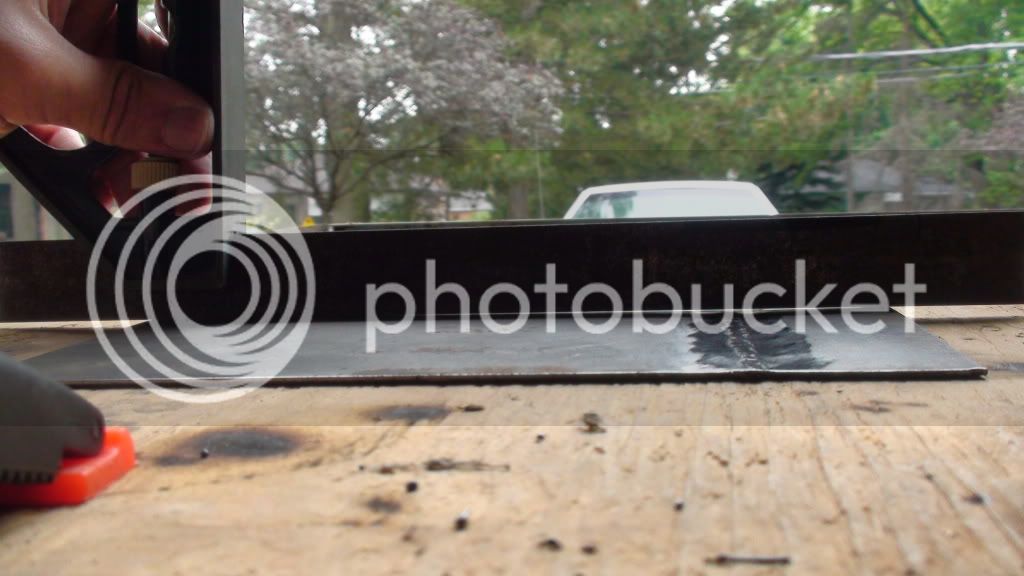
shielding gas was used, compressor to cool down the welds with a blast of air, grinder with grinder wheel, 40 and 80 grit flappers to work it smooth.
I would always start my welds on the big piece of metal and move it to the smaller piece being attached. should I try just following the cut?