Sparticusrye
Active Member
- Joined
- Mar 28, 2011
- Messages
- 43
- Reaction score
- 4
Now that I've started to get some free time and after watching everyone else build engines. I've finally started on my first IC engine, the Bill 1906 by Jerry Howell. I purchased the plans about a month ago after I got my lathe. Went out and purchased enough materials to build two (Always nice to have some extra material just in case). And have finally recieved the last of my order of measuring tools so that I could get started.
So I tossed a chunk of 2.5" CR steel in the chuck and started on the initial stages of the crankcase and cover. I would have completed the cover except the temperature outside dropped to zero celsius and I couldn't feel my fingers. So I figured that was a good sign to head into the house and warm up. My shop is in my shed which is not insulated or heated at the moment. I did get a few hours worth of machining done though so I was happy. Some of the internal boring for the crankcase were a challenge for me since I haven't touched a lathe in almost a year. But after a few taps on the stop button and some chin scratching I figured it out and got a satisfactory result. I might make a second crankcase in the future as I am not completely happy with the bearing hole.
So here are couple shots of my start.
And with them together.
Hopefully get some more time and better temperatures tomorrow so I can complete the cover.
James
So I tossed a chunk of 2.5" CR steel in the chuck and started on the initial stages of the crankcase and cover. I would have completed the cover except the temperature outside dropped to zero celsius and I couldn't feel my fingers. So I figured that was a good sign to head into the house and warm up. My shop is in my shed which is not insulated or heated at the moment. I did get a few hours worth of machining done though so I was happy. Some of the internal boring for the crankcase were a challenge for me since I haven't touched a lathe in almost a year. But after a few taps on the stop button and some chin scratching I figured it out and got a satisfactory result. I might make a second crankcase in the future as I am not completely happy with the bearing hole.
So here are couple shots of my start.
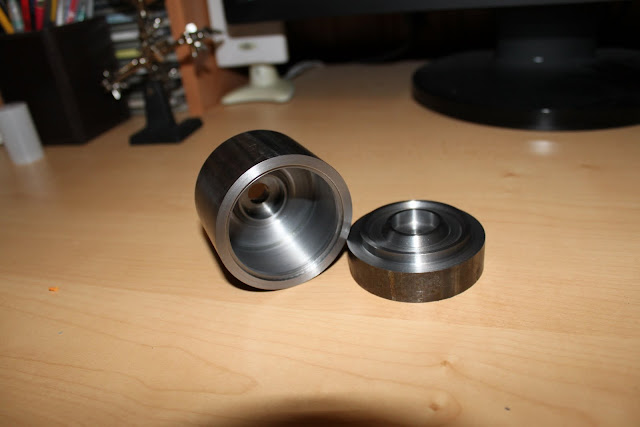
And with them together.
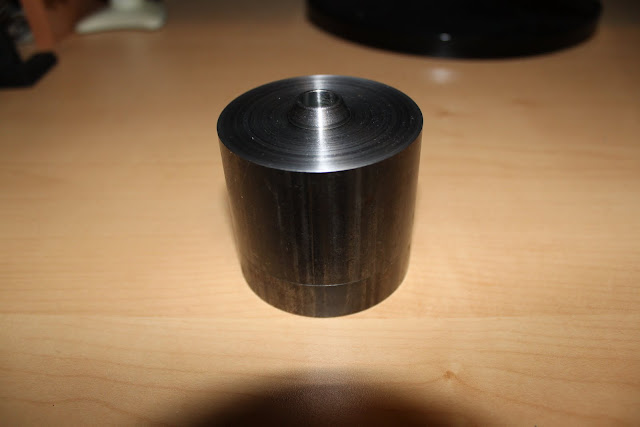
Hopefully get some more time and better temperatures tomorrow so I can complete the cover.
James