rythmnbls
Well-Known Member
- Joined
- Jan 14, 2012
- Messages
- 115
- Reaction score
- 31
Time for another update...
The counter-weight is done, I setup my old casting furnace and put it to use as you can see here..
A view inside the furnace after it cooled.
Next up was a mount for the x-axis motor, the first job was to drill four counter-bored holes to accept some SHCS in the table x-axis end plate. These screws will hold the motor mount blocks.
Here's a couple of photos showing the arrangement of the end-plate, the motor mounts and coupling.
I decided to take a break from making parts and assemble the control box. Here's a work in progress pic of installing the internal wiring.
And a photo of testing the control box with Linuxcnc, all axes tested out ok which was a relief.
All that is left to do is make the Z-axis nut and fit the Y-axis handle with a toothed drive pulley, hopefully I'll get those done by next weekend as I'm looking forward to making some chips. ;D
Thanks for reading.
Steve.
The counter-weight is done, I setup my old casting furnace and put it to use as you can see here..
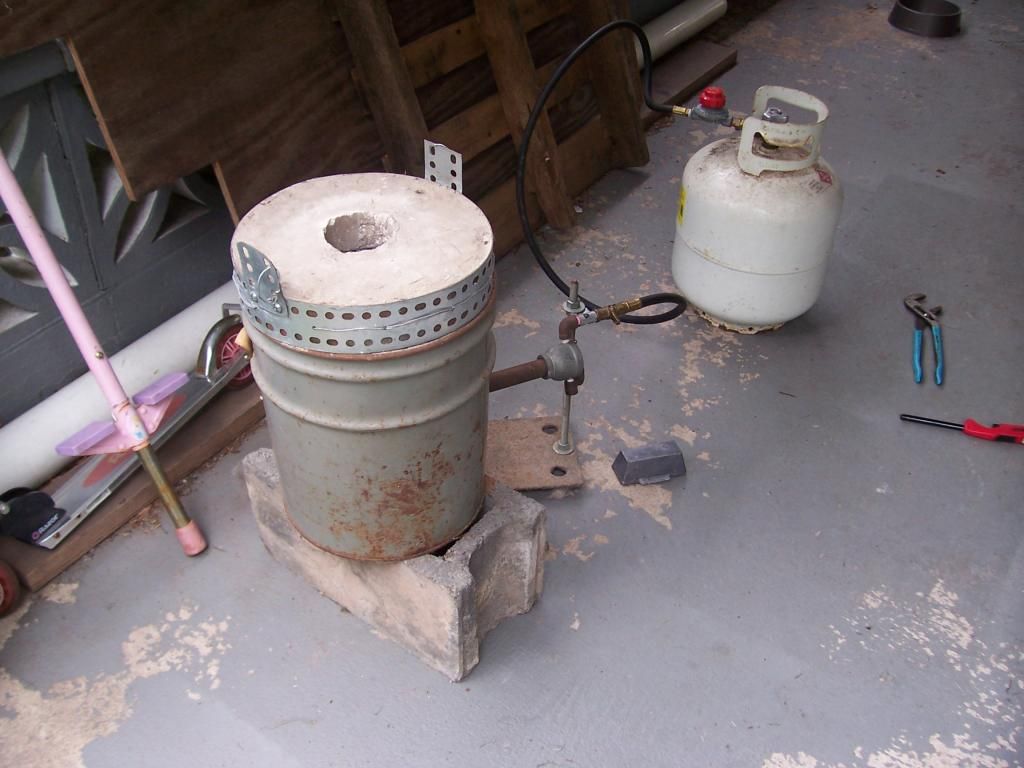
A view inside the furnace after it cooled.
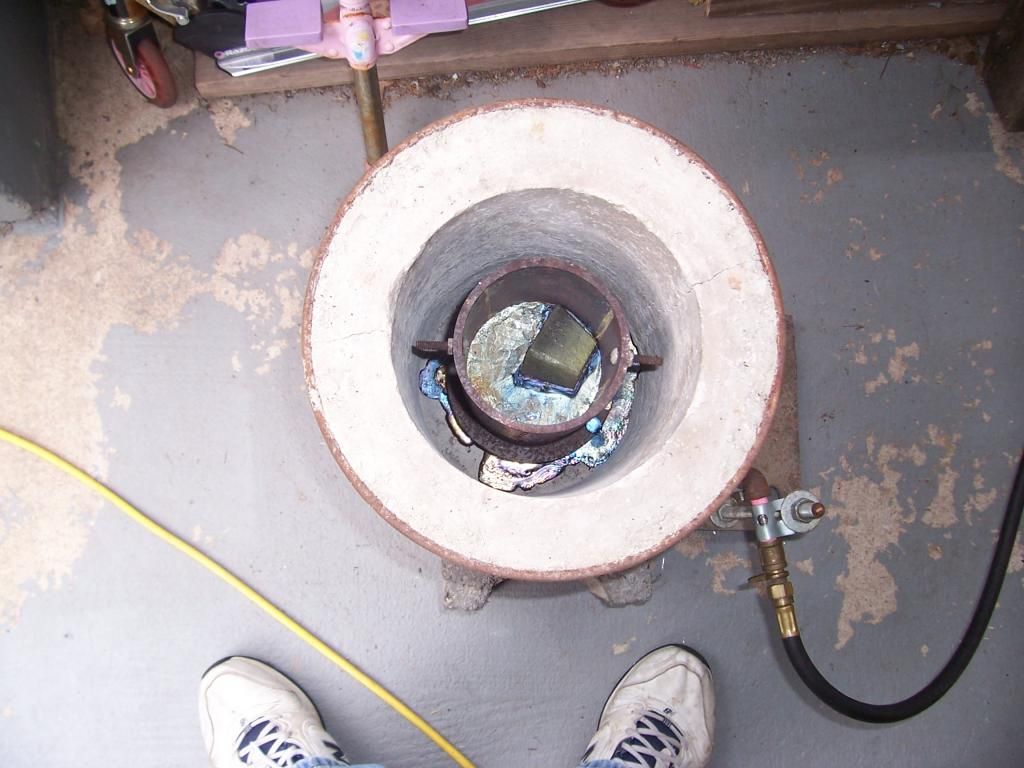
Next up was a mount for the x-axis motor, the first job was to drill four counter-bored holes to accept some SHCS in the table x-axis end plate. These screws will hold the motor mount blocks.
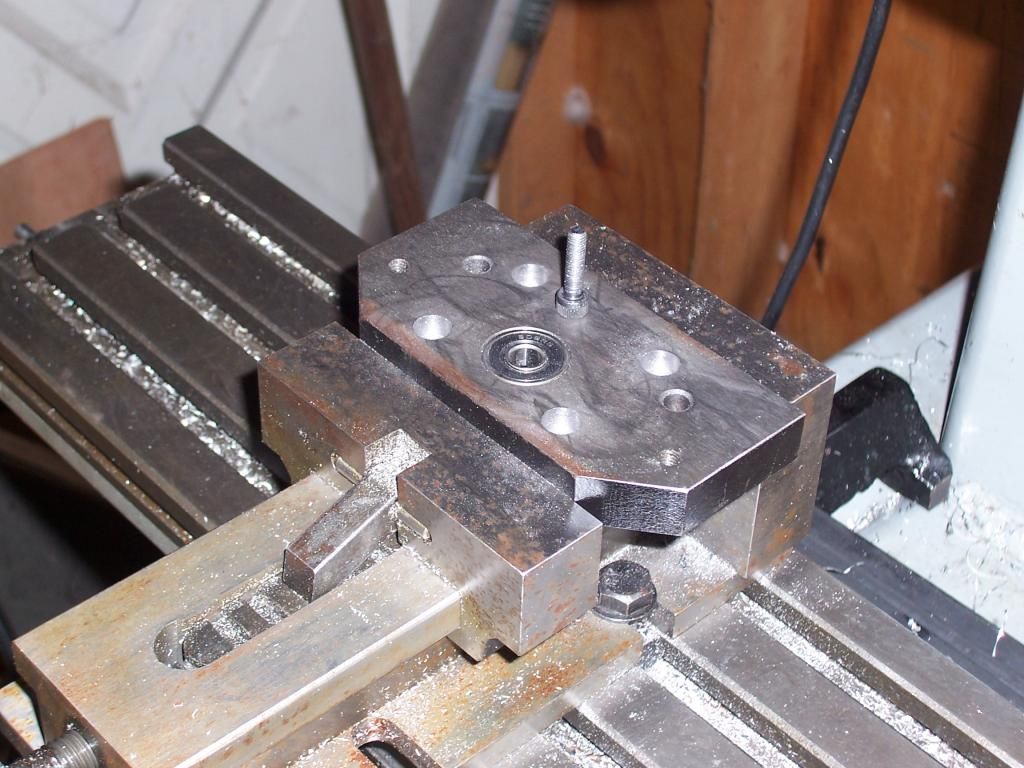
Here's a couple of photos showing the arrangement of the end-plate, the motor mounts and coupling.
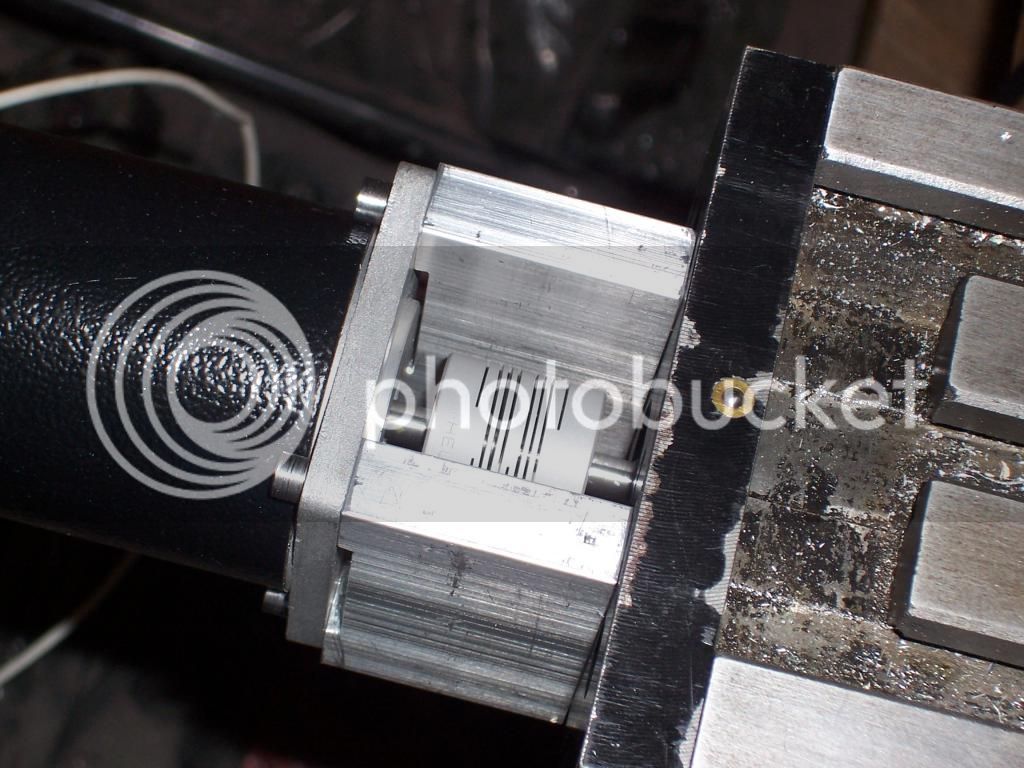
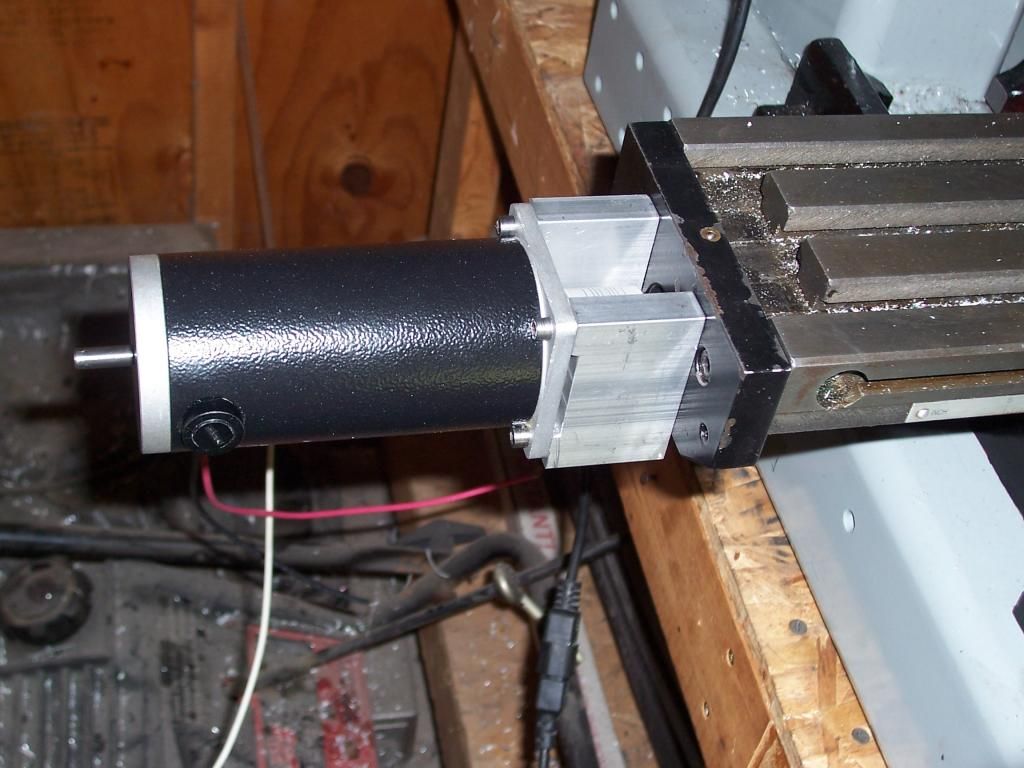
I decided to take a break from making parts and assemble the control box. Here's a work in progress pic of installing the internal wiring.
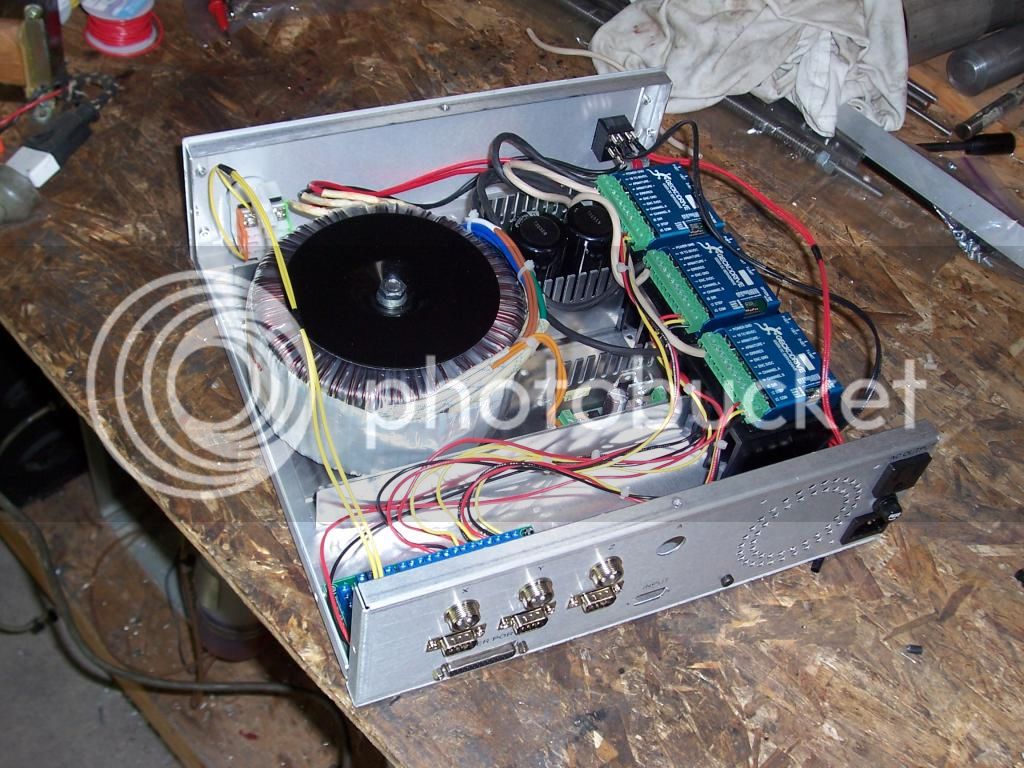
And a photo of testing the control box with Linuxcnc, all axes tested out ok which was a relief.
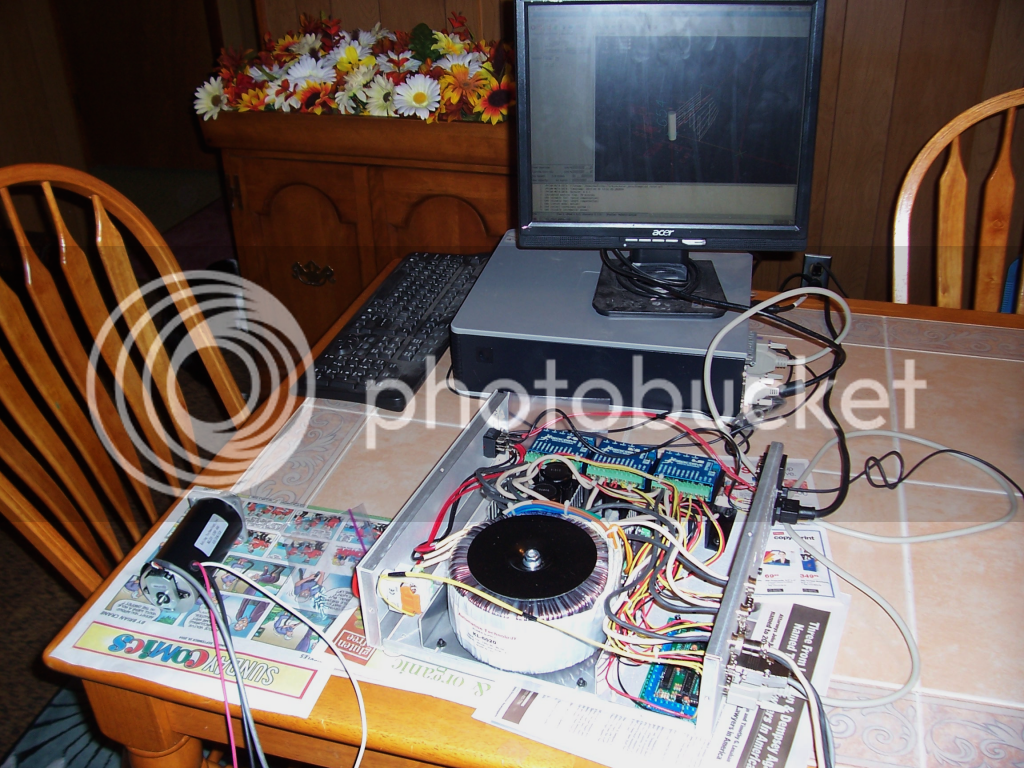
All that is left to do is make the Z-axis nut and fit the Y-axis handle with a toothed drive pulley, hopefully I'll get those done by next weekend as I'm looking forward to making some chips. ;D
Thanks for reading.
Steve.