Hello folks;
As if I didn't have enough irons in the fire, I figure I would add one more. Since I started doing the CNC conversions on the Mill and Lathe last winter, my 14 old son has kinda taken an interest in what I'm doing down there in the basement shop. Every time I run into a glitch with the computer, I would have to have him come down and help me figure it out. He is into sports and video games like most kids that age, but when I was working on the Mill steppers I asked him if I would like to learn how to solder wires and connections for the project, he said he would try. Not knowing much about that myself and the extra "hands" in my case, I was excited. So after he done the research on the net I let him at it. He done a great job. Now he is in the shop checking stuff out all the time. Couple nights ago we where ready to make the first "CNC" cut piece, so I let him set it up and hit the go button.
Any how............We where both smiling ear to ear.
I ask him If he like to start a project with me and this is what we came up with for our first attempt at Father/Son project.
Received the book today and did a quick look through, and seems to be very straight forward, but a very complex. Should make for a interesting build.
Matt
As if I didn't have enough irons in the fire, I figure I would add one more. Since I started doing the CNC conversions on the Mill and Lathe last winter, my 14 old son has kinda taken an interest in what I'm doing down there in the basement shop. Every time I run into a glitch with the computer, I would have to have him come down and help me figure it out. He is into sports and video games like most kids that age, but when I was working on the Mill steppers I asked him if I would like to learn how to solder wires and connections for the project, he said he would try. Not knowing much about that myself and the extra "hands" in my case, I was excited. So after he done the research on the net I let him at it. He done a great job. Now he is in the shop checking stuff out all the time. Couple nights ago we where ready to make the first "CNC" cut piece, so I let him set it up and hit the go button.
Any how............We where both smiling ear to ear.
I ask him If he like to start a project with me and this is what we came up with for our first attempt at Father/Son project.
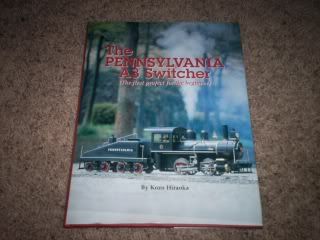
Received the book today and did a quick look through, and seems to be very straight forward, but a very complex. Should make for a interesting build.
Matt