- Joined
- Jul 16, 2007
- Messages
- 2,986
- Reaction score
- 1,055
At the time I built my 4 cylinder engine there weren't any commercial spark plugs available. The supply of plugs built in the 60's had just about dried up and they weren't the right length for my engine anyway. The solution, build your own, which I have been doing for years. With the new supply of spark plugs manufactured by Rim Fire I wanted to try them out in my engine but the problem is that when I made my engine I tapped the head for 1/4-28 threads and the new plugs are 1/4-32. My engine runs well enough with my Teflon plugs but with the high rpm it starts to erode the Teflon at the tip. There is no way to make the 32 thread plugs fit in my 28 thread holes so I decided to make a new head. My original head is cast iron, Durabar to be more exact. It is an extremely fine grained iron which cuts very nice and holds nice sharp corners. I like it for the fact that I don't need to make valve guide/seat inserts for the head, everything is just machined into the head. The first few pictures show the piece of iron and my steps in machining it. I always face the widest face first. This gives me a larger surface to locate my edge cuts to. After cutting this face I rotate the block 90 degrees in the vise and cut the narrow edges. You can see in the one picture I use a piece of heavy copper wire as a backup to put even pressure on the irregular surface. My final step is to use pinch down clamps to hold the piece tight against the parallels for the finishing cut.
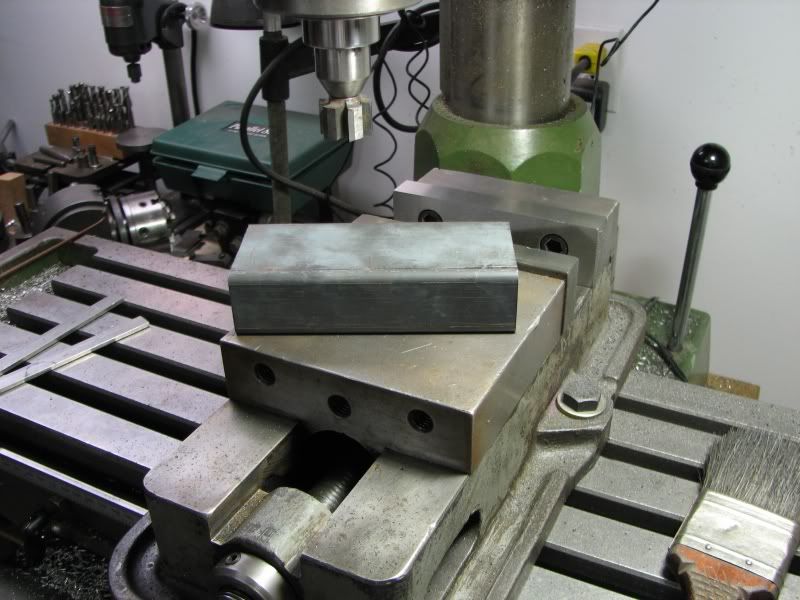
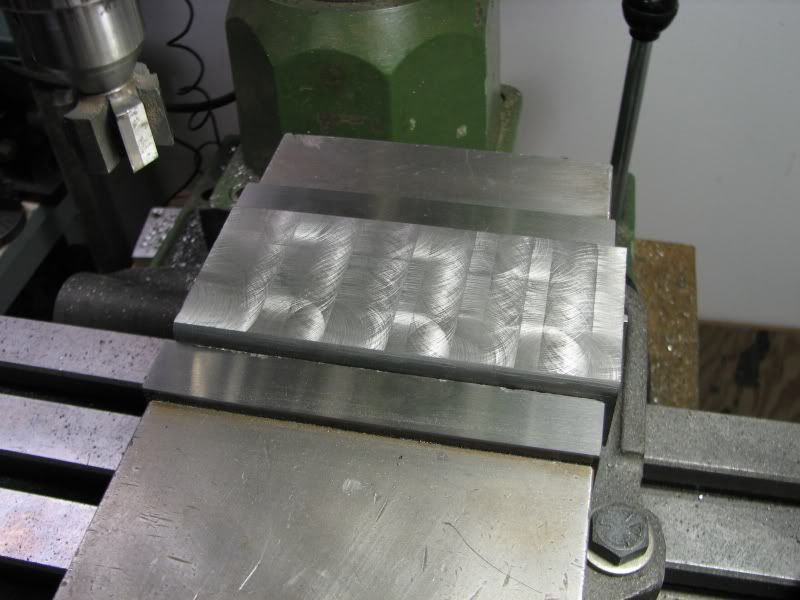
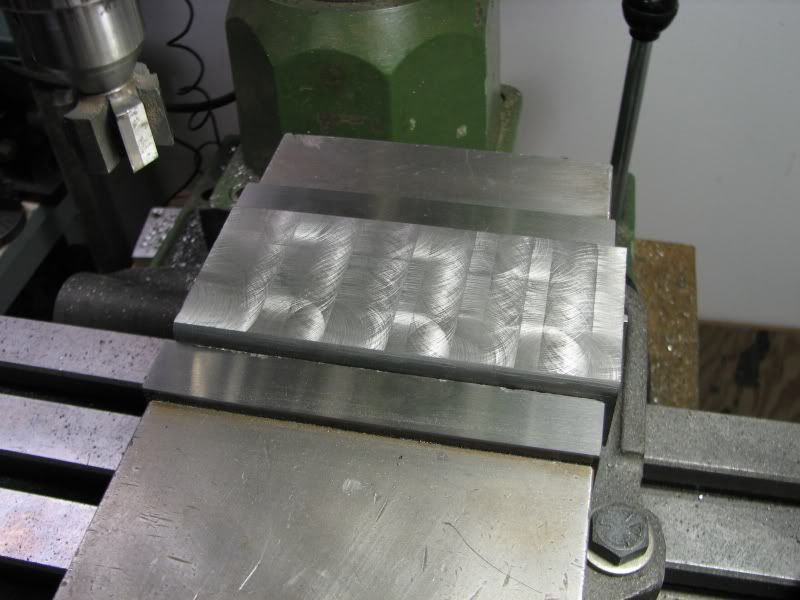
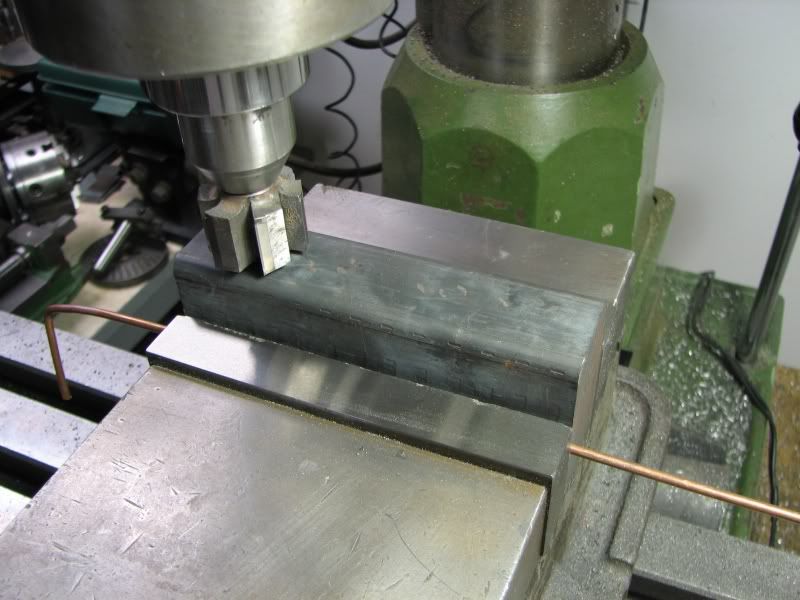
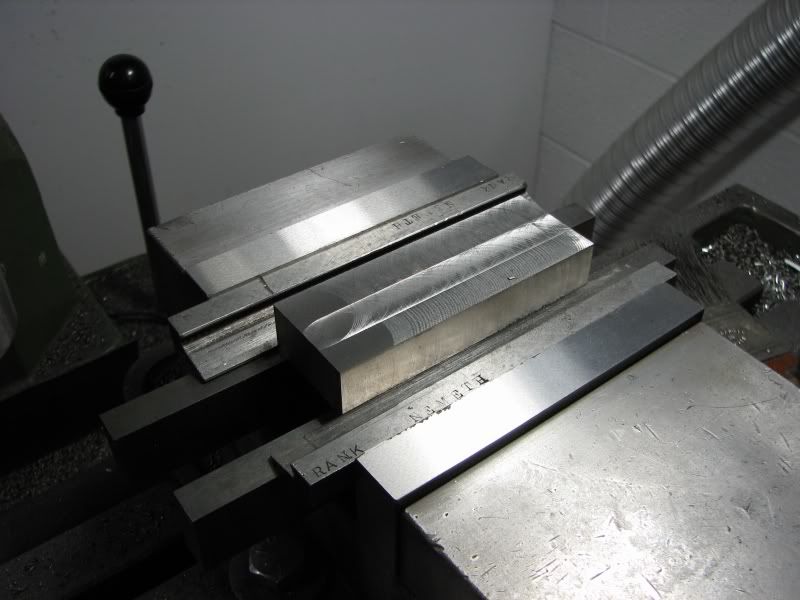