This morning its too cold to play outside, and I'm bored.--Which is not necessarily a bad thing. I have been perusing my booklet "507 Mechanical Movements" by Henry T Brown, looking for some kind of intriguing mechanical "eye candy" to possibly build. This is a little booklet choc full of all kind of nifty mechanical devices that were invented at the beginning of the mechanical revolution. Some of them were great devices, which are still in use today in modern machinery. Some are ideas that worked and were used for a period of time when mechanical things were transitioning from steam power to gasoline power, and some of them were probably only ever built once, just to see if they would work. A device that caught my eye this morning is item #27, which is listed as "Multiple Gearing" with the following description:--"A recent invention. The smaller triangular wheel drives the larger one by the movement of its attached friction-rollers in the radial grooves." There are no measurements nor geometric relationships given, only the picture shown here. I thought "Hmmmm---That's interesting!!! I wonder if I can replicate that and sus out the geometric relationships in Solidworks?" Good wife was still in bed sleeping, so I snuck downstairs to my office, fired up the computer, and found out that "By Golly, I can!!!" Of course the next question was, what do I have to run something like that? A static display just doesn't cut it. In my room devoted to small steam and gasoline engines which I have built over the last five years, there is the sad remains of what once was a very proud "Hit and Miss" air engine originally designed by Chuck Fellows over on HMEM. It ran marvellously, but I had cannibalized parts off it and used them for other purposes, and the main corpse has been laying around for two years now, waiting to be resurrected as something new. A few measurements and some deep thought has suggested that I should be able to use it as the main engine for a dynamic display of this marvelous old "Multiple Gearing" idea. So--as the summer advances and I get downtime from other work and play, I will be building this.----Brian
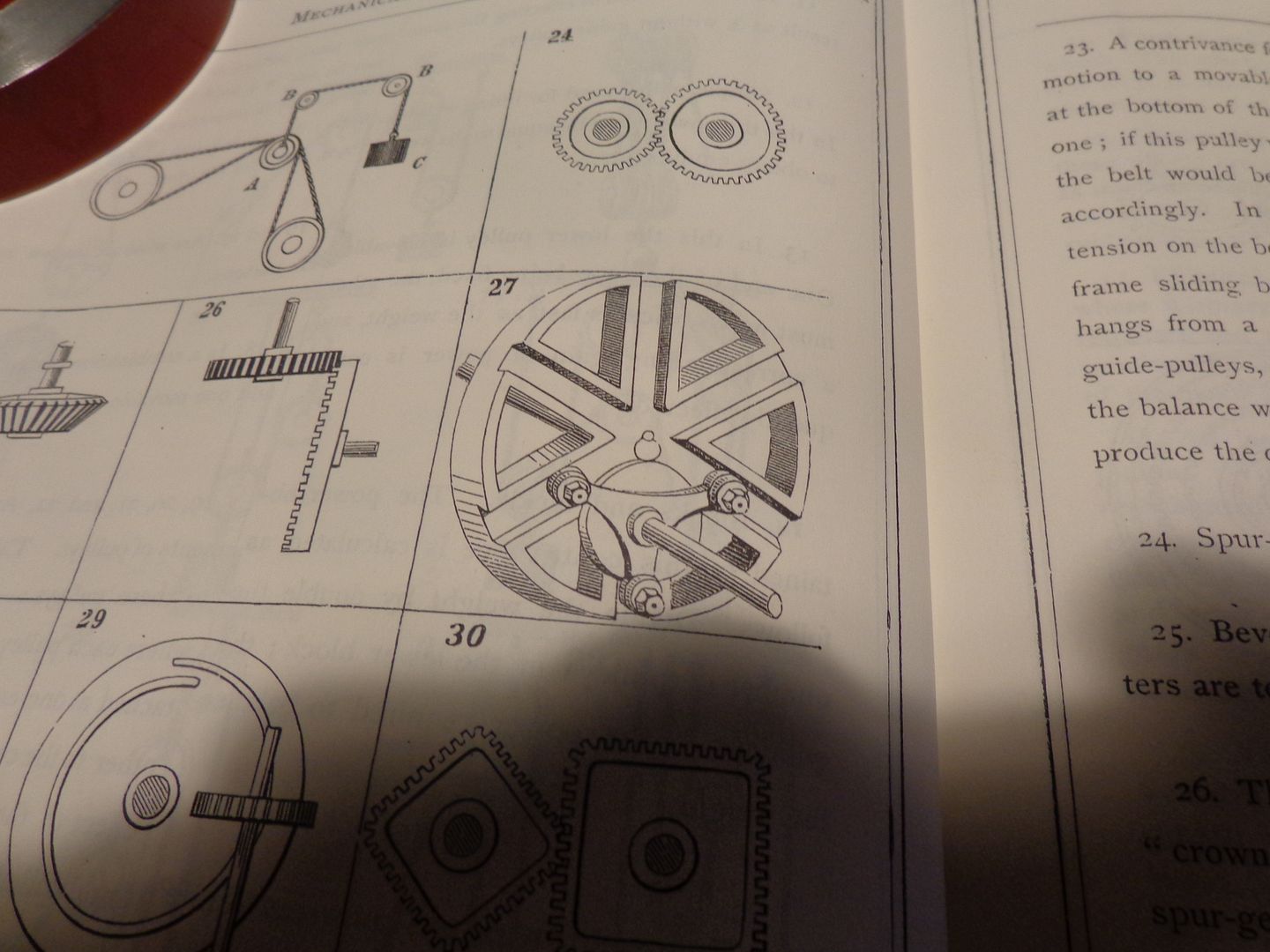
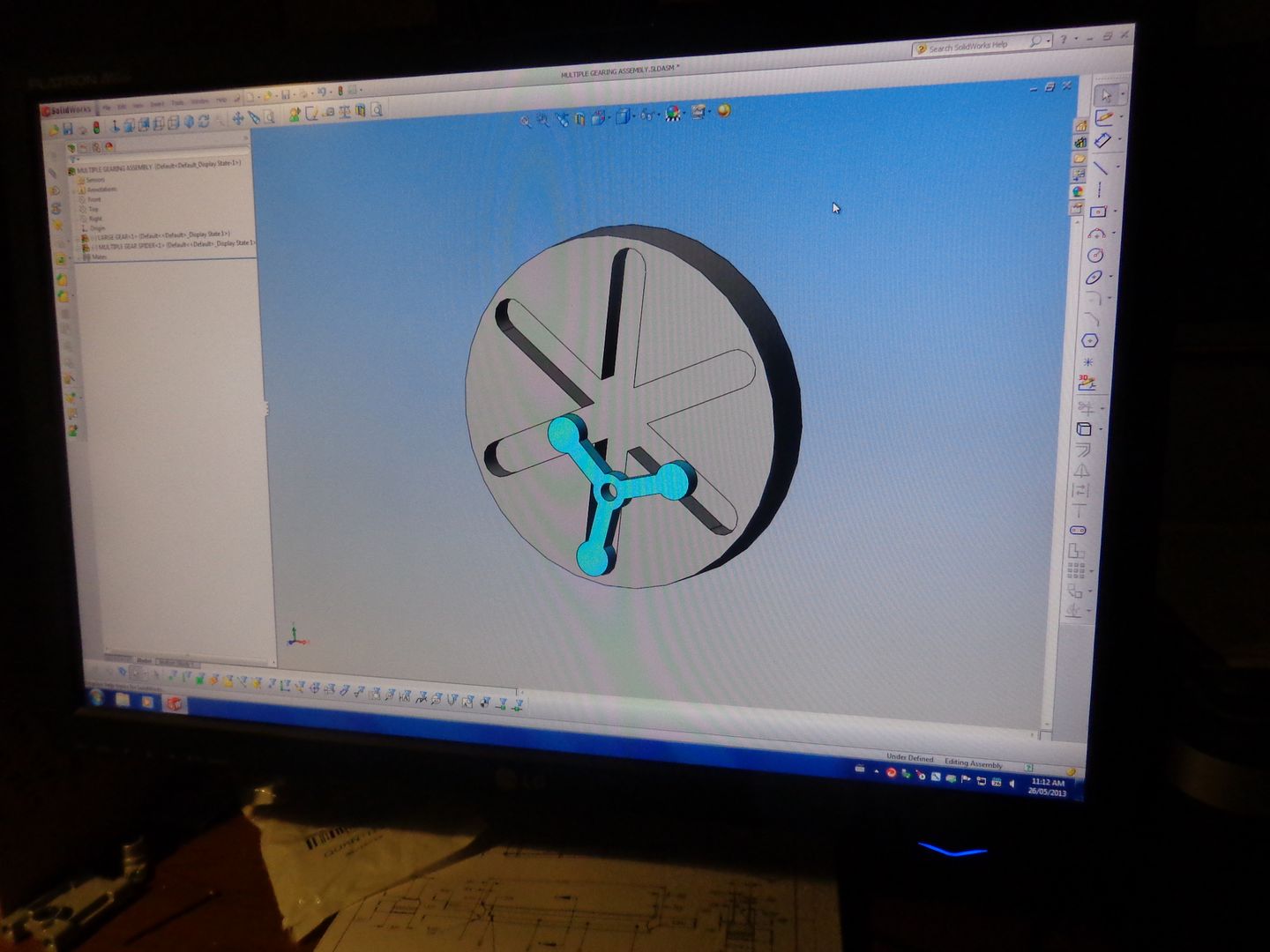
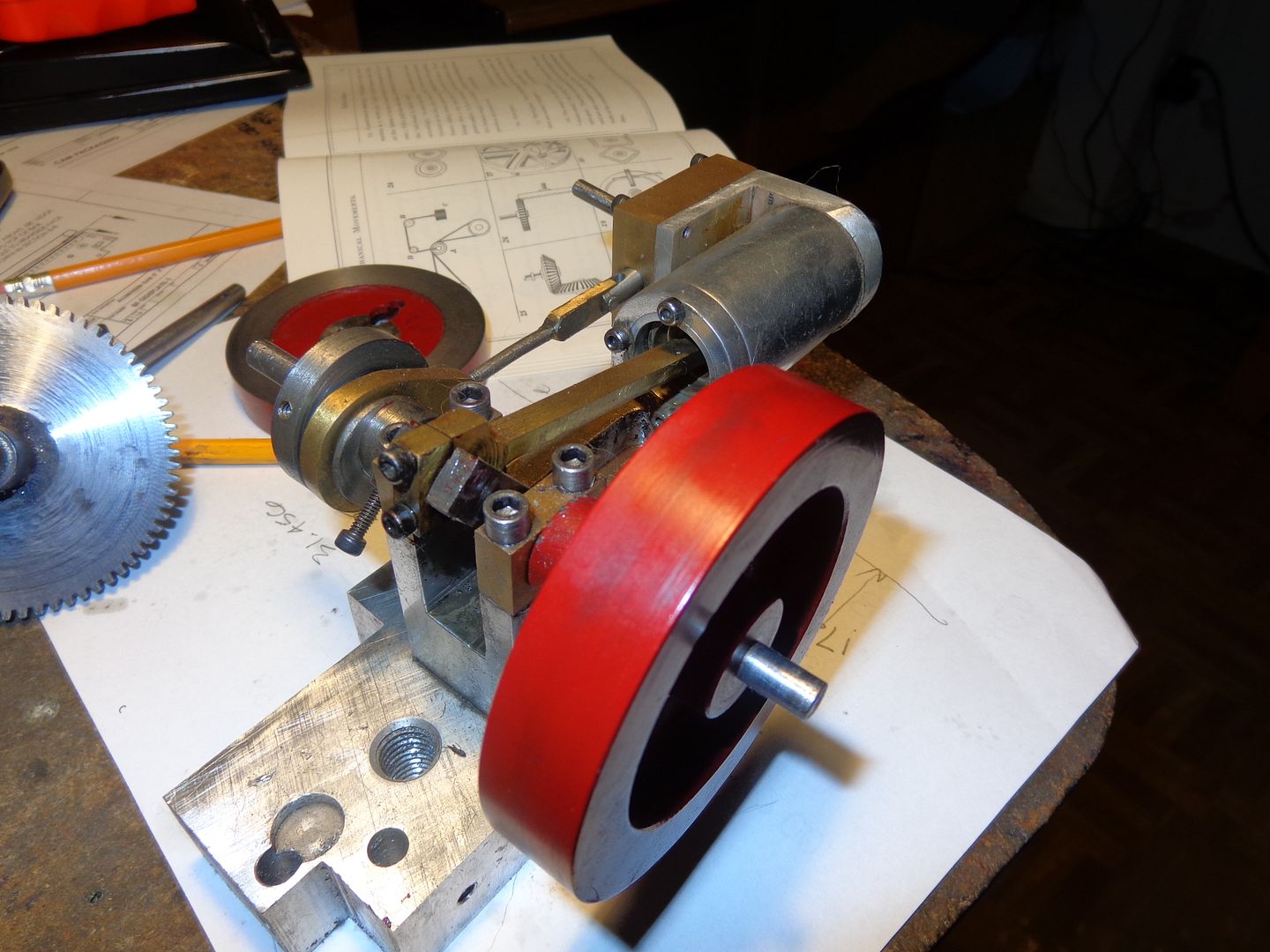