I had better get my first build log on this forum down on paper or it will end up in finished projects! The inspiration was this advert on the Internet :-
http://www.prestonservices.co.uk/stationary.htm
A great looking engine but not one I copy.
With a 12 ins flywheel, it was too big to do full size and I have no casting facilities. Searching on the Internet, Elmer did both horizontal and a vertical oscillators, but of course, I had to do one my way! Looking at what I had for materials, the flywheel had to be made from a 2.5 ins diameter blank and the body from 2 x ½ ins stock. (In the UK some bar stock is still sold in Imperial sizes.) The throw on the crank was to be 10 mm, so with a stroke of 20 mm, 16 mm seemed about right for the bore.
Using these sizes, I sketched out the rough design :-
This is just a first draught and I am constantly changing it as I make this build.
Ian
http://www.prestonservices.co.uk/stationary.htm
A great looking engine but not one I copy.
With a 12 ins flywheel, it was too big to do full size and I have no casting facilities. Searching on the Internet, Elmer did both horizontal and a vertical oscillators, but of course, I had to do one my way! Looking at what I had for materials, the flywheel had to be made from a 2.5 ins diameter blank and the body from 2 x ½ ins stock. (In the UK some bar stock is still sold in Imperial sizes.) The throw on the crank was to be 10 mm, so with a stroke of 20 mm, 16 mm seemed about right for the bore.
Using these sizes, I sketched out the rough design :-
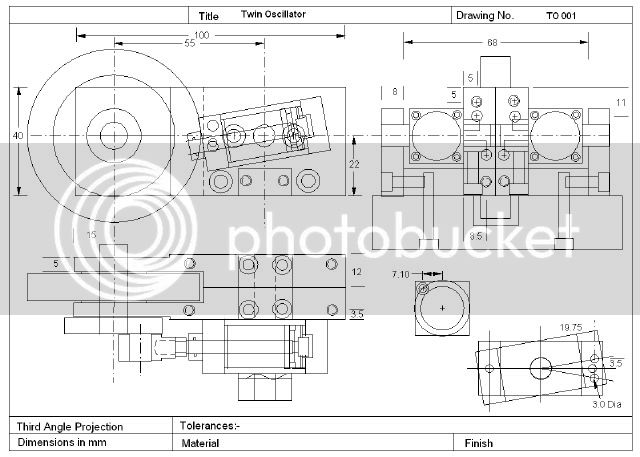
This is just a first draught and I am constantly changing it as I make this build.
Ian