Some of you might have noticed from another thread that this hunk of "old iron"
is about to take up residence in my workshop
this lathe could well be older than me
........... certainly takes me back to my schoolboy machining days ;D
I'd been thinking of changing the little 9"x20" to a British version ......... mainly to gain a little more mass and to have the benefit of a gearbox and power feeds. I'd been looking at a lot of Myfords (which seem to command very high prices) but a big thank you to Bogsie :bow: for putting me onto the trail of the Boxfords, they seem a lot more machine and can be had at more sensible prices.
Any way, it's a Boxford AUD Mk2, which is a clone of the 9" Southbend for our American listeners
Spot the similarities
There is a wealth of information about these on the web but some of it is a little conflicting, the AUD is the model "A" (Screwcutting Gearbox and Power feeds in both directions) with UD ....... UnderDrive, the motor is in the base / cabinet. The total weight is over 600lbs so that's the first hurdle.
Transporting it home should be OK, it can be loaded into my van with a fork lift, at my end we can have the use of an engine lift to get it out ......... but ........... to get it into the workshop it has to go through 2 x single doorways up 2 steps, then down one step, so methinks dismantling it may be the best way forward.
In principle it seems straightforward, but two points concern me a little ..............
"1) If the lathe has a gearbox, leave it in place - and try not to remove a lathe from an under-drive stand; a compound was used to stop coolant getting into the wrong places and effectively sticks the lathe down; once broken the hardened sealer has to be chipped off and the joint remade.
2) Apparently the drive belt is continuous and will need to be cut."
So ......... does anyone out there actually have experience of taking one of these apart .......... or ...........am I going to be the HMEM Guinea Pig :
CC
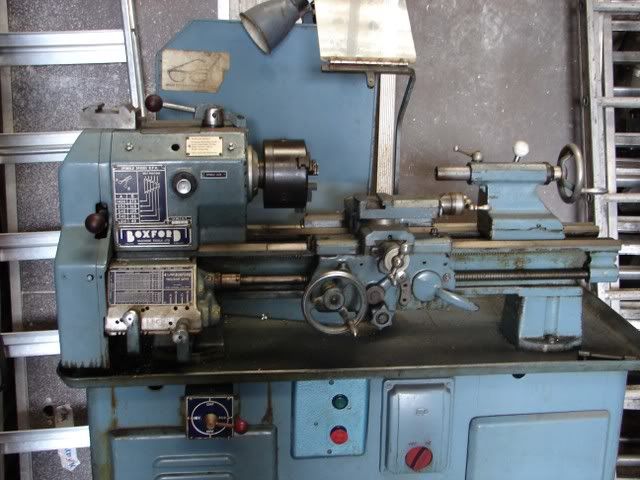
is about to take up residence in my workshop
this lathe could well be older than me
I'd been thinking of changing the little 9"x20" to a British version ......... mainly to gain a little more mass and to have the benefit of a gearbox and power feeds. I'd been looking at a lot of Myfords (which seem to command very high prices) but a big thank you to Bogsie :bow: for putting me onto the trail of the Boxfords, they seem a lot more machine and can be had at more sensible prices.
Any way, it's a Boxford AUD Mk2, which is a clone of the 9" Southbend for our American listeners
Spot the similarities
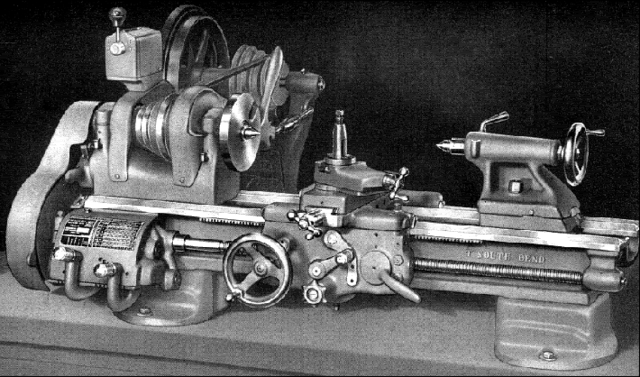
There is a wealth of information about these on the web but some of it is a little conflicting, the AUD is the model "A" (Screwcutting Gearbox and Power feeds in both directions) with UD ....... UnderDrive, the motor is in the base / cabinet. The total weight is over 600lbs so that's the first hurdle.
Transporting it home should be OK, it can be loaded into my van with a fork lift, at my end we can have the use of an engine lift to get it out ......... but ........... to get it into the workshop it has to go through 2 x single doorways up 2 steps, then down one step, so methinks dismantling it may be the best way forward.
In principle it seems straightforward, but two points concern me a little ..............
"1) If the lathe has a gearbox, leave it in place - and try not to remove a lathe from an under-drive stand; a compound was used to stop coolant getting into the wrong places and effectively sticks the lathe down; once broken the hardened sealer has to be chipped off and the joint remade.
2) Apparently the drive belt is continuous and will need to be cut."
So ......... does anyone out there actually have experience of taking one of these apart .......... or ...........am I going to be the HMEM Guinea Pig :
CC