- Joined
- Oct 29, 2011
- Messages
- 287
- Reaction score
- 2
Time to fix the cylinder to the new cylinder base that I machined earlier! This meant spotting the holes through somehow (since I had to match the existing holes in the cylinder).
I initially started with annoying little bits of paper:
but then had a better idea. I fixed the cylinder up in the vise with a kind of jig that would let me place the base on top repeatably. Then I could just line up on a hole using a drill that was smaller than threaded hole
by carefully lowering the drill and looking/listening for interference. Then I just put the cylinder base in place, bottom side up, and, without moving the table, spot-drilled with a center drill:
Then I could transfer just the base to the vise, and drill and countersink each hole. Presto, nice fit:
Next will be spotting the holes through from the main casting to the cylinder base, which might be a bit trickier.
I initially started with annoying little bits of paper:
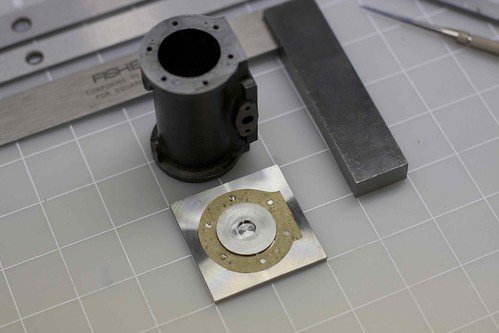
but then had a better idea. I fixed the cylinder up in the vise with a kind of jig that would let me place the base on top repeatably. Then I could just line up on a hole using a drill that was smaller than threaded hole
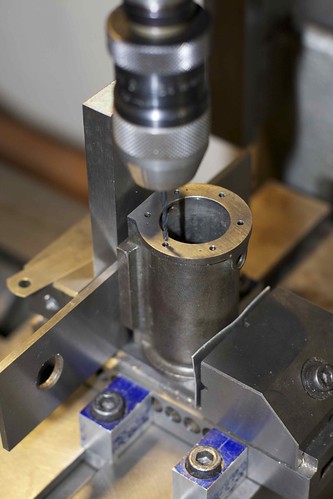
by carefully lowering the drill and looking/listening for interference. Then I just put the cylinder base in place, bottom side up, and, without moving the table, spot-drilled with a center drill:
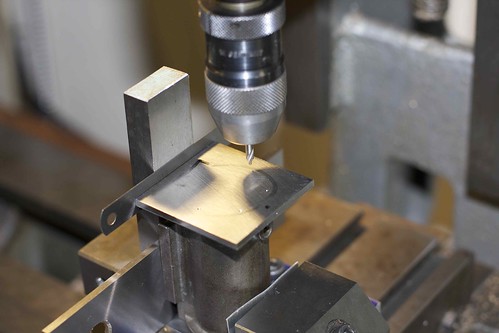
Then I could transfer just the base to the vise, and drill and countersink each hole. Presto, nice fit:
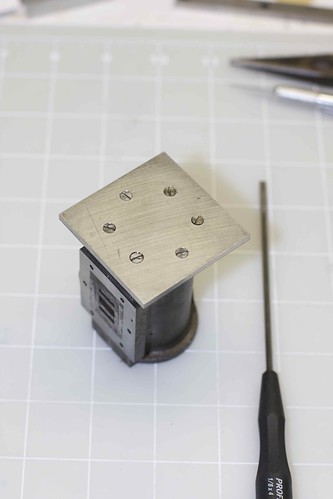
Next will be spotting the holes through from the main casting to the cylinder base, which might be a bit trickier.