- Joined
- Oct 29, 2011
- Messages
- 287
- Reaction score
- 2
Hi folks
I've been working on restoring a Stuart Beam, and thought that I should put up some photos. I bought this engine along with a 501 boiler on eBay in 2010, before I even had a lathe, and fixing it up was a good excuse to get one ;D
The engine had its share of problems, a really ugly paint job, and some odd modifications. It had obviously seen quite a bit of use, with some notable wear on the conrod big end, a fairly loud knocking when running, and a lot of looseness in the parallel linkage.
My goal is to get it back to a nice quality, smooth-running engine. This is my first real steam project with the lathe (you can see my setup here: http://www.homemodelenginemachinist.com/index.php?topic=16417.msg167565#msg167565).
Here's the engine in its original state:
Stuart Beam by smfr123, on Flickr
I've been working on restoring a Stuart Beam, and thought that I should put up some photos. I bought this engine along with a 501 boiler on eBay in 2010, before I even had a lathe, and fixing it up was a good excuse to get one ;D
The engine had its share of problems, a really ugly paint job, and some odd modifications. It had obviously seen quite a bit of use, with some notable wear on the conrod big end, a fairly loud knocking when running, and a lot of looseness in the parallel linkage.
My goal is to get it back to a nice quality, smooth-running engine. This is my first real steam project with the lathe (you can see my setup here: http://www.homemodelenginemachinist.com/index.php?topic=16417.msg167565#msg167565).
Here's the engine in its original state:
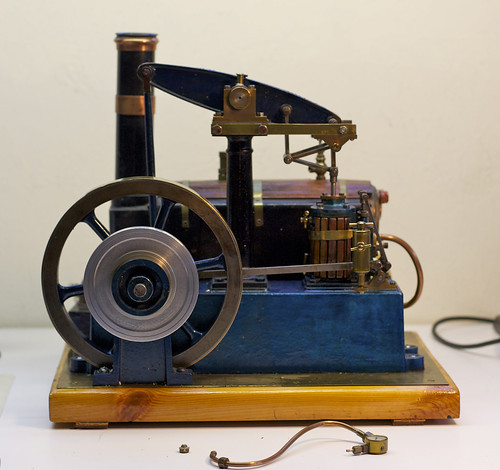
Stuart Beam by smfr123, on Flickr