JAndrew
Well-Known Member
- Joined
- Aug 9, 2013
- Messages
- 113
- Reaction score
- 21
Hello,
Chuck Fellows recently posted his ER-32 collet chuck for a mini-lathe that was backplate mounted. I appreciate his post a lot as he provided some good advice on getting the 8 degree taper for the collet precise.
I'm going to post progress on my collet chuck but be forewarned: "I have little or no idea what I'm doing really."
It's been over 10 years since I machined anything and even then I was billeted as an "Emergency Machinist" on submarines so my experience is minimal.
Here's the cross section collet chuck plan that I drew up in google sketchup:
I would strongly advise that anyone reading NOT use these plans. As I said I'm not really sure I know what I'm doing.
So far:
The first mistake I've made so far was ordering a piece of 12L14 that was 2.50" in diameter instead of 2.75". In order to keep the wall thickness "meaty" enough the flats of the nut will be a little further apart and not meet at pointed angles. I guess I should have finished those plans entirely before ordering the stock! :wall:
I am starting with my stock at a length of 3.50" instead of the 3.00" that is shown on my plans just in case I make any kind of mistake on the 8 degree taper.
Here's the progress:
I placed the stock in the four jaw chuck and dialed in the runout to within 0.005". Then faced the end and flipped it around. I dialed in again at 0.002" (due to the un-even rolled external surface).
The plan is to bore all the way through to a diameter of 1.125". I faced the 2nd end of the stock and center drilled. Then drilled to 0.375". The stepped it up to 0.500". Then stepped it up to 0.625". And finally drilled to 57/64 or 0.890".
The above picture shows the boring bar set up in the Aloris style tool holder with a 1/4" HSS bit. The boring to 1.125" went well each time advancing the cross feed dial by 0.010". Each time though I did an additional "Spring" cut as I'm in no hurry. It seemed necessary as the boring bar is extended pretty far to bore through the full 3.50" length of the stock.
I had to stop there for the day. (New baby in the house so I only work during Nap-Times or in the early morning).
The plan moving forward is to bore the section for the spindle threads to 1.350" and thread 1.50"x8TPI. I included an extra large thread relief groove as I'm deathly afraid of running into the work.
Any suggestions or feedback is greatly appreciated. Don't know when I'll get back out to the shop.
Thanks,
-J.Andrew
Chuck Fellows recently posted his ER-32 collet chuck for a mini-lathe that was backplate mounted. I appreciate his post a lot as he provided some good advice on getting the 8 degree taper for the collet precise.
I'm going to post progress on my collet chuck but be forewarned: "I have little or no idea what I'm doing really."
It's been over 10 years since I machined anything and even then I was billeted as an "Emergency Machinist" on submarines so my experience is minimal.
Here's the cross section collet chuck plan that I drew up in google sketchup:
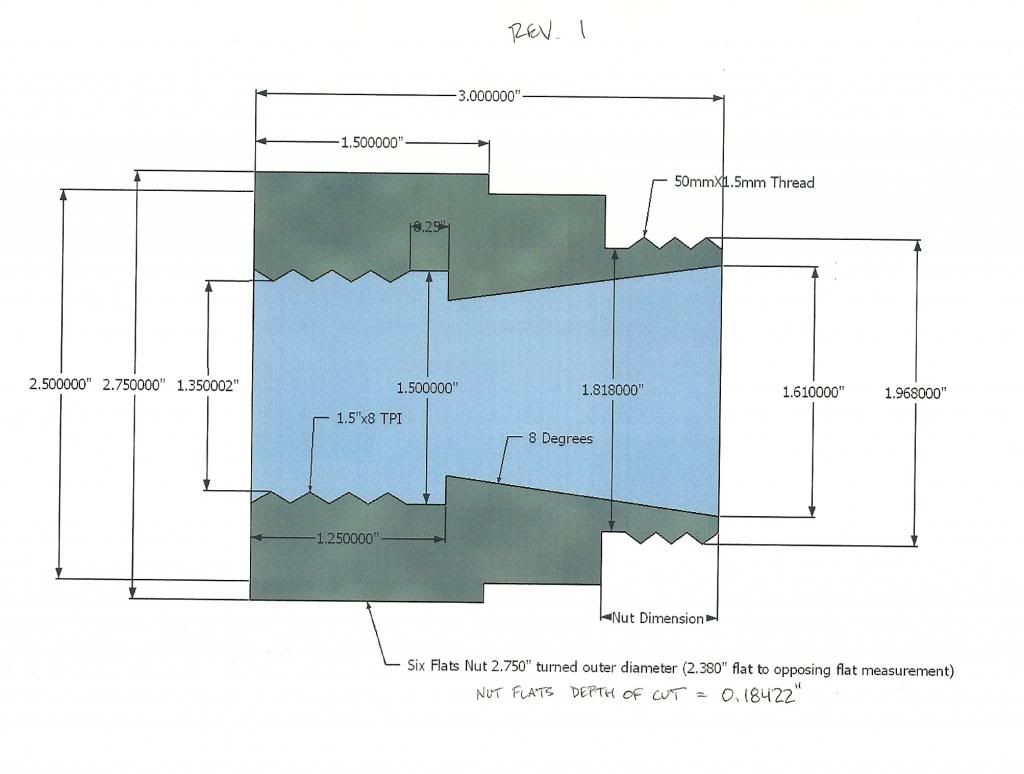
I would strongly advise that anyone reading NOT use these plans. As I said I'm not really sure I know what I'm doing.
So far:
The first mistake I've made so far was ordering a piece of 12L14 that was 2.50" in diameter instead of 2.75". In order to keep the wall thickness "meaty" enough the flats of the nut will be a little further apart and not meet at pointed angles. I guess I should have finished those plans entirely before ordering the stock! :wall:
I am starting with my stock at a length of 3.50" instead of the 3.00" that is shown on my plans just in case I make any kind of mistake on the 8 degree taper.
Here's the progress:
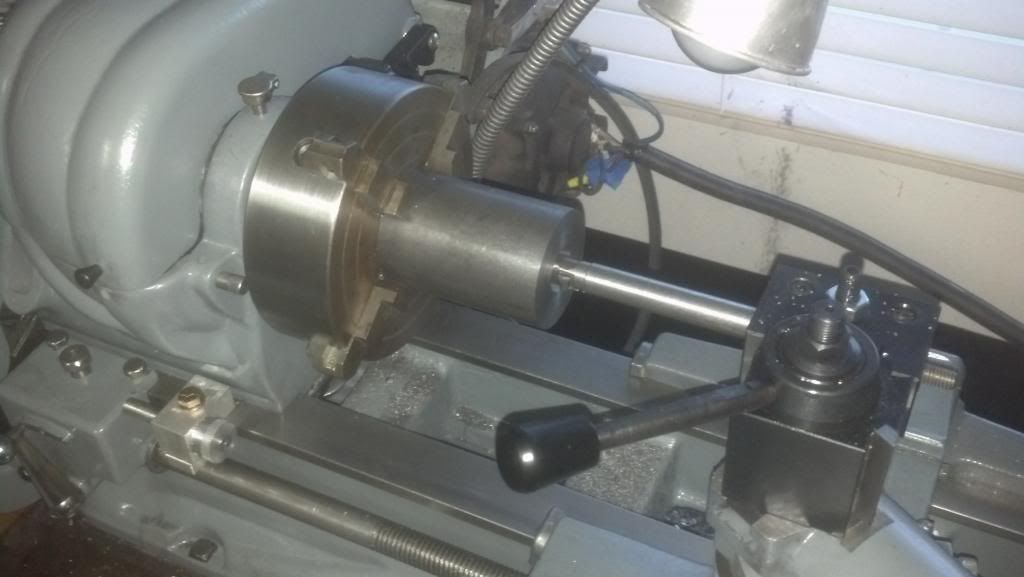
I placed the stock in the four jaw chuck and dialed in the runout to within 0.005". Then faced the end and flipped it around. I dialed in again at 0.002" (due to the un-even rolled external surface).
The plan is to bore all the way through to a diameter of 1.125". I faced the 2nd end of the stock and center drilled. Then drilled to 0.375". The stepped it up to 0.500". Then stepped it up to 0.625". And finally drilled to 57/64 or 0.890".
The above picture shows the boring bar set up in the Aloris style tool holder with a 1/4" HSS bit. The boring to 1.125" went well each time advancing the cross feed dial by 0.010". Each time though I did an additional "Spring" cut as I'm in no hurry. It seemed necessary as the boring bar is extended pretty far to bore through the full 3.50" length of the stock.
I had to stop there for the day. (New baby in the house so I only work during Nap-Times or in the early morning).
The plan moving forward is to bore the section for the spindle threads to 1.350" and thread 1.50"x8TPI. I included an extra large thread relief groove as I'm deathly afraid of running into the work.
Any suggestions or feedback is greatly appreciated. Don't know when I'll get back out to the shop.
Thanks,
-J.Andrew